BAC_AC_CasCtrlT_02
Application
The template is a cascade controller for the supply air temperature, consisting of two master controllers for set value calculation for heating, cooling and energy recovery.
Interface
Plant diagram 01
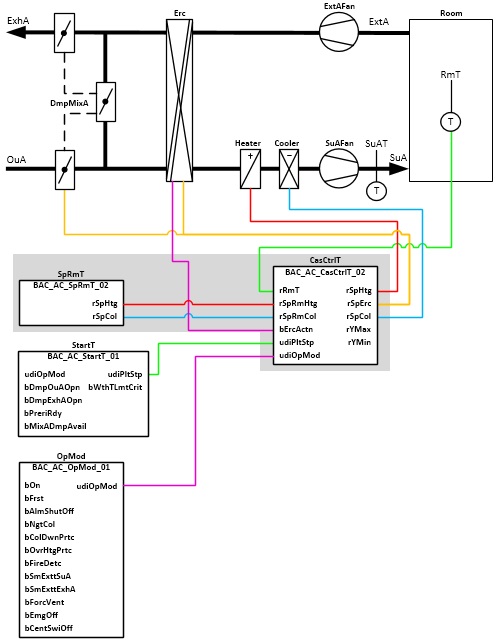
Plant diagram 02
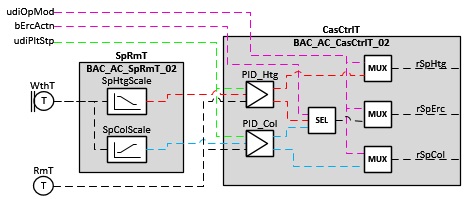
Block diagram
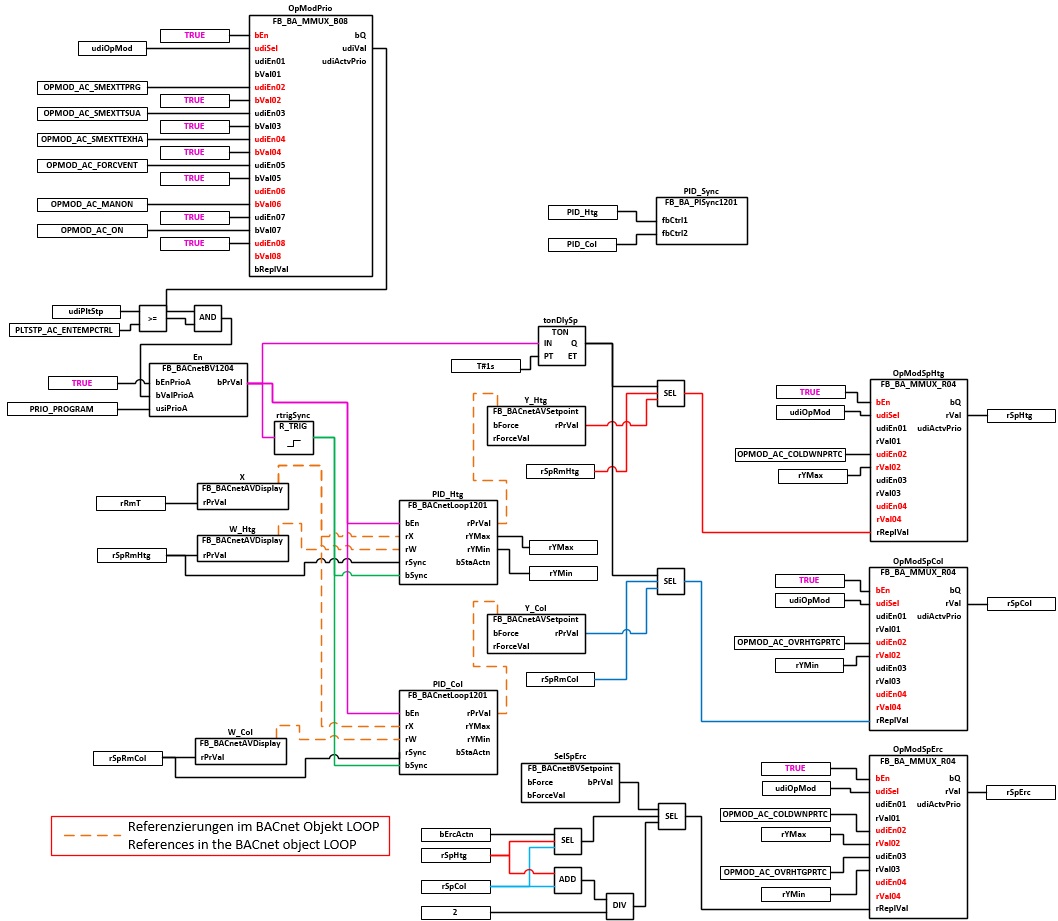
VAR_INPUT
rRmT : REAL;
rSpRmHtg : REAL;
rSpRmCol : REAL;
udiPltStp : UDINT;
udiOpMod : UDINT;
rRmT: Input variable to which the room temperature is applied. The room temperature is the control value of the PID master controllers. If no room temperature is available, the outlet air temperature of a ventilation system can be used as control value.
rSpRmHtg: Input variable for the room temperature set value for heating, see template BAC_AC_SpRmT_02.
rSpRmCol: Input variable for the room temperature set value for cooling, see template BAC_AC_SpRmT_02.
bErcActn: Input variable to which the direction of action for the energy recovery is applied. The set value for the energy recovery is determined depending on the direction of action.
TRUE = direct = cooling; FALSE = reverse = heating
udiPltStp: Steps during startup of the air-conditioning plant. See also BAC_AC_Start_01
udiOpMod: Plant operation mode. See also BAC_AC_OpMod_01
VAR_OUTPUT
rSpHtg : REAL;
rSpErc : REAL;
rSpCol : REAL;
rYMax : REAL;
rYMin : REAL;
rSpHtg: Calculated set value of the supply air temperature for heating
rSpErc: Calculated set value of the supply air temperature for energy recovery
rSpCol: Calculated set value of the supply air temperature for cooling
rYMax: Upper value of the controller output limitation
rYMin: Lower value of the controller output limitation
VAR CONSTANT
PLT_NUM : BYTE := 1;
PLT_NUM: all alarms and events of all plant components within a controller are included in a global alarm and event list. The assignment of events and alarms to a plant is defined by the assignment of a PLT_NUM plant number.
The recording and processing of an alarm from an aggregate or a device takes place within the templates by means of the alarm function block FB_BA_Alarm.
The evaluation of the alarms of a plant, e.g. for the generation of a collective message or for plant shutdown in case of relevant faults, takes place within the template BAC_PltAlm_01 by means of the function block FB_BA_AlarmPlt.
The evaluation of different plant events within the templates of a plant, takes place within the template BAC_PltComnMsg_01 by means of the function block FB_BA_ComnMsg.
Important! The assignment and evaluation of the alarms and events of a plant can only be done correctly if all templates of a plant have the same plant number!
The plant number can be assigned in the Project Builder in the parameter menu for the templates or via a column in the Excel import.
Program description
Instance | Type | Task | ||||
---|---|---|---|---|---|---|
X | The input variable rRmT is connected to the AV object. | |||||
W_Htg | The input variable rSpRmHtg is connected to the AV object. | |||||
W_Col | The input variable rSpRmCol is connected to the AV object. | |||||
OpModPrio | The multiplexer defines the enable conditions of the two PID master controllers depending on the plant operation mode udiOpMod. | |||||
udiOpMod | Enable cascade control | |||||
OPMOD_AC_SMEXTTPRG | Smoke extraction program | TRUE | ||||
OPMOD_AC_SMEXTTSUA | Smoke extraction supply air | TRUE | ||||
OPMOD_AC_SMEXTTEXHA | Smoke extraction exhaust air | TRUE | ||||
OPMOD_AC_FORCVENT | Forced ventilation | TRUE | ||||
OPMOD_AC_MANON | Manual on | TRUE | ||||
OPMOD_AC_ON | On | TRUE | ||||
En | The BV object is used to display the controller enable in the MCL or in a local operator display. | |||||
| >=, AND | The result of this network is the enable of the two PID master controllers. The enable depends on the plant operation mode udiOpMod and the plant steps udiPltStp during startup of the ventilation system. | ||||
PID_Htg | Master controller for a room temperature control via room supply air cascade. It provides the supply air temperature setpoint for heating. | |||||
PID_Col | Master controller for a room temperature control via room supply air cascade. It provides the supply air temperature setpoint for cooling. | |||||
rtrigSync | R_TRIG | Upon receipt of the controller enable En, rtrigSync triggers synchronization of the two master controllers PID_Htg / PID_Col with the input value lrSync. | ||||
Y_Htg | The AV object is referenced to the control value output of the BACnet loop object PID_Htg. It shows the supply air temperature setpoint for heating. | |||||
TLogY_Htg | Trend logging of the supply air temperature setpoint for heating Y_Htg. | |||||
Y_Col | The AV object is referenced to the control value output of the BACnet loop object PID_Col. It shows the supply air temperature setpoint for cooling. | |||||
TLogY_Col | Trend logging of the supply air temperature setpoint for cooling Y_Col. | |||||
PID_Sync | The function block synchronizes the parameters for the two master controllers PID_HTG / PID_COL. | |||||
tonDlySp | TON | Upon receipt of the controller enable En, this network forwards the supply air temperature setpoints to the downstream multiplexers with a delay. | ||||
OpModSpHtg | The multiplexer defines the heating setpoint rSpHtg depending on the plant operation mode udiOpMod in certain cases. | |||||
udiOpMod | Setpoint | |||||
OPMOD_AC_COLDWNPRTC | Support operation, cooling protection | rYMax, upper setpoint of the controller output limitation | ||||
OpModSpCol | The multiplexer defines the cooling setpoint rSpCol depending on the plant operation mode udiOpMod in certain cases. | |||||
udiOpMod | Setpoint | |||||
OPMOD_AC_OVRHTGPRTC | Overheating protection | rYMin, lower setpoint of the controller output limitation | ||||
SelSpErc | Selection strategy setpoint energy recovery. TRUE: average of rSpHtg and rSpCol; FALSE: depends on the control direction, defined by input bErcActn | |||||
| SEL, ADD, DIV, SEL | The result of this network supplies two setpoints for energy recovery. Which value is used depends on the energy recovery setpoint strategy, see SelSpErc | ||||
OpModSpErc | The multiplexer defines the energy recovery setpoint rSpErc depending on the plant operation mode udiOpMod in certain cases. | |||||
udiOpMod | Setpoint | |||||
OPMOD_AC_COLDWNPRTC | Support operation, cooling protection | rYMax, upper setpoint of the controller output limitation | ||||
OPMOD_AC_OVRHTGPRTC | Overheating protection | rYMin, lower setpoint of the controller output limitation |
Version history
Version number | Comments |
---|---|
1.0.1 | First release |