AX2xxx-B200 Drive
The Beckhoff AX2000 and AX2500 drive is available with different (in the case of AX2000 optional) fieldbus interfaces. The following dialogs are for an AX2000 with Beckhoff Lightbus interface (e.g. part no.: AX2003-B200). Nevertheless, the dialogs and descriptions is also suitable for AX2500, since these drives are fully software compatible to the AX2000.
"AX2000" Tab
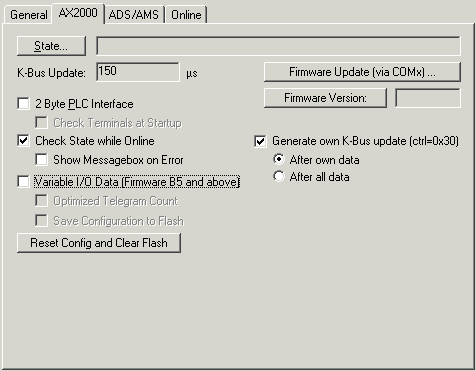
State: The variable "State" of the AX2000-B200 Servo drive can be linked to a variable of another process image (e.g. with TwinCAT PLC) here.
K-Bus Update: Optionally, Beckhoff Bus Terminals can be hooked up to an AX2000 drive. Based on the attached terminals, the K-Bus update time is calculated and displayed here.
Firmware Update: The Firmware of the -B200 Lightbus interface can be updated through the serial COM port of the PC, if this button is pressed.
Firmware Version: After pressing of this button, the current Firmware version of the -B200 Lightbus interface is read and displayed in the field next to it..
2 Byte PLC Interface: After checking of this box, input and output variables for the PLC Interface will be inserted below the drive symbol in the tree view.
Check Terminals at Startup: Checks during initialization phase, whether configured Bus Terminals (optional) are really connected to the K-Bus extension of the drive). It has no function at drives without K-Bus extension.
Check State while Online: Evaluates cyclical the -B200 "State" variable if checked. On error condition, a message will be brought to the System Manager Logger View.
Show Message Box on Error: Fires on error conditions, additionally to the Logger View and Event viewer entry, a Message Box to the surface.
Generate own K-Bus update: Activates own des K-Bus cycle if 0x30 telegram arrives to the Lightbus interface and the master card sends no broadcast telegram. This checkbox is activated by default at AX2xxx-B200 drives.
After own data: The K-Bus update is done directly after own data was sent.
After all data: The K-Bus update is done after all data of the current CDL were sent.
Variable I/O Data: From Firmware version "B5" of the -B200 Lightbus interface for the AX2000 drive on, the Lightbus telegram structure to the drive can be optimized (at AX2500 drives at all Firmware revisions). To allow the optimization, this and the following checkbox must be activated. For compatibility reasons, this checkbox "Variable I/O Data" is not checked by default, when a new AX2000 device is added to the System Manager configuration.
Optimized Telegram Count: See:. Variable I/O Data
Save Configuration to Flash: If this box is checked, the configuration is going to be saved to the Flash memory of the drive with each TwinCAT start (only, if at least one parameter has changed).
Reset Config and Clear Flash: The Flash memory of the drive can be cleared by pressing this button.
"Nominal Channel" Tab
For further information about this tab, see: "AX2xxx Drive Tab - Outputs"
Diagnosis Inputs (optional)
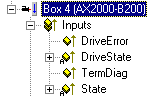
If the variables DriveError,DriveState (alternatively DriveState2 and DriveState3) are added to the Variable I/O Data (described above), they can be used for diagnosis purposes (e.g. if they are linked to a TwinCAT PLC process image, they can be evaluated inside the PLC run-time system).
For further information about the error and warning codes of the AX2xxx drive, see: "AX2xxxx Drive - Status and Error Codes"