Electrical installation
NOTICE | ||
![]() | UL Listing It is essential to observe chapter "Product overview-->Guidelines and Standards-->UL-Listing" if you wish to operate an AX5000 in an economic area that requires a UL-Listing. |
| |
Risk of injury!
|
| |
Risk of injury through electric shock! De-energise all electrical components (servo drive, control cabinet, etc.) before commencing the installation or deinstallation. |
| |
Serious risk of injury through electric shock! Due to the DC link capacitors dangerous voltage may persist at the DC link contacts "X02" after the servo drive has been disconnected from the mains supply. After disconnecting the servo drive wait 5 minutes and measure the voltage at the DC link contacts DC+ and DC-. The device is safe once the voltage has fallen below 50 V. |
| |
Risk of injury through electric shock!
|
| |
Destruction of the AX5000!
|
Connection example
The following diagram shows a typical connection diagram for a two-axis device. Motor 1 features an absolute encoder, motor 2 a resolver:
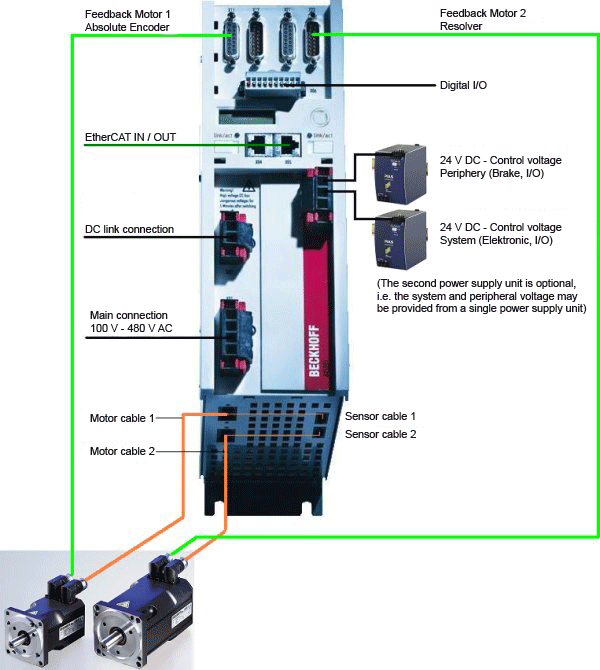