Power supply
| |
Risk of injury! The electrical installation must be carried out by a qualified electrician. Before installing and commissioning AX5000 servo drives please read the safety notes in the foreword of this documentation. |
Notice | |
Destruction of the AX5000! The connection sequence of the devices is not arbitrary. The total rated current of the device must decrease from the power supply. The order "AX5112-AX5106-AX5201-AX5103" is correct the order "AX5201-AX5112-AX5203" is wrong. |
| |
Hazard to persons! Note the total current of the connected devices. According to CE the current carrying capacity of power busbars is limited to 85 A. |
| |
Hazard to persons! Please ensure that the connection line for the AX5901 supply module is adequately dimensioned. The dimensioning depends on the total rated current and must comply with EN 60204-1. The connector plugs are designed for a maximum conductor cross-section of 25 mm2. A 3-phase connection must be used if the total rated current exceeds 9 A. |
| |
Hazard to persons! To set up a drive system without AX5901 supply module and AX bridge please note the following: The connector plugs of the wide voltage input are designed for a maximum current of 41 A and a maximum conductor cross-section of 6 mm2. The cable configuration must comply with the requirements specified in DIN VDE 0298 Part 4 / 2003-08 and EN 60204-1.Avoid phase reversal between the devices! |
X01: Main supply connection
NOTICE | ||
![]() | UL Listing It is essential to observe chapter "Product overview-->Guidelines and Standards-->UL-Listing" if you wish to operate an AX5000 in an economic area that requires a UL-Listing. |
Voltage systems ranging from single-phase 100 VAC to three-phase 480 VAC can be connected to the wide voltage input of the AX5000. In single-phase systems the mains phase is connected to terminal point L1 and the neutral conductor to terminal point L3/N.
| Terminal point | Connection | Tightening torque | |
---|---|---|---|---|
3-phase | 1-phase | |||
L1 | Phase L1 | Phase L1 |
0,5 - 0,6 Nm | |
L2 | Phase L2 | not used | ||
L3/ N | Phase L3 | Neutral conductor | ||
PE | Protective conductor | Protective conductor |
Connection to the standard mains supply (TT / TN) with earthed centre
Single phase 100 -10% .- 240 +10% VAC, 50/60 Hz | Three phase 100 -10% .- 480 +10% VAC, 50/60 Hz |
Connection to a IT-mains supply (100 - 240 V) without isolating transformer
Notice | |
EMC Act in europe! Due to electromagnetic emission, in Europe the AX5000 must be operated in conjunction with an isolating transformer. |
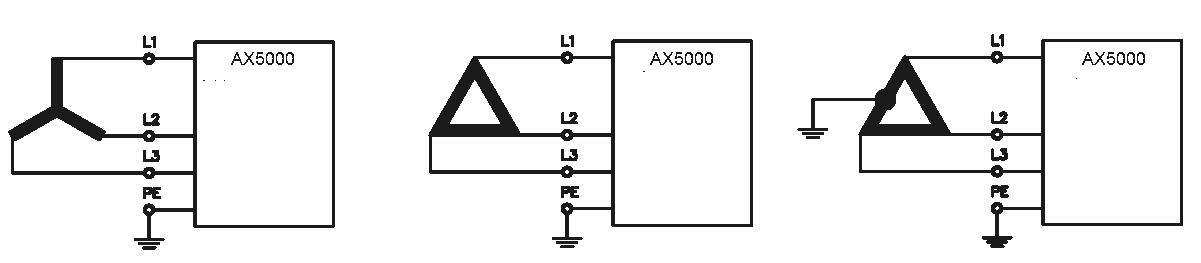
Connection to other mains types (100 - 240 V) without isolating transformer
|
|
Connection to other mains types (100 - 240 V) with isolating transformer
Notice | |
Destruction of the AX5000! For asymmetrically earthed or non-earthed 100...480 V mains an isolating transformer must be used. |
100 - 480 V Isolating transformer | 240 - 480 V Isolating transformer |
Fusing
| |
Fire hazard through cable overload!
|
External protection, CE-compliant
Single-phase:
| AX5101 | AX5103 | AX5106 | AX5201 | AX5203 | AX5206 |
---|---|---|---|---|---|---|
AC supply *) | 10 AT | 10 AT | 16 AT | 10 AT | 16 AT | 20 AT |
24 V supply | 3 AT | |||||
Brake resistor | electronic |
*) Application class "gG" mains fuses according to IEC 60269 or "C" type automatic circuit-breakers must be used.
Three-phase:
| AX5101 | AX5103 | AX5106 | AX5112 | AX5118 | AX5125 | AX5140 | AX5201 | AX5203 | AX5206 |
---|---|---|---|---|---|---|---|---|---|---|
AC supply *) | 6 AT | 6 AT | 10 AT | 20 AT | 35 AT | 35 AT | 50 AT | 10 AT | 10 AT | 20 AT |
24 V supply | 3 AT | |||||||||
Brake resistor | electronic |
*) Application class "gG / gL" mains fuses according to IEC 60269 or "C" type automatic circuit-breakers must be used.
Internal protection, CE-compliant
Circuit | Fuse |
---|---|
24 V system voltage | 3.4 AF |
24 V peripheral voltage | electronic |
Brake resistor | electronic |
External protection, UL-compliant
Integral solid state short circuit protection does not provide branch circuit protection. Branch circuit protection must be provided in accordance with the Manufacture Instructions, National Electrical Code, and any additional local codes.
Suitable for use on a circuit capable of delivering not more than 18000 rms symmetrical amperes, 480 V maximum, when protected by RK5 class fuses.
Single-phase:
| AX5101 | AX5103 | AX5106 | AX5201 | AX5203 | AX5206 |
---|---|---|---|---|---|---|
AC-supply (max.) *) | 6 A | 12 A | 20 A | 12 A | 20 A | 20 A |
24 V-supply (max.) | 3 A | |||||
Brake resistor | electronic |
*) Mains fuses according to type “RK5” must be used.
Three-phase:
| AX5101 | AX5103 | AX5106 | AX5112 | AX5201 | AX5203 | AX5206 |
---|---|---|---|---|---|---|---|
AC-supply (max.) *) | 6 A | 12 A | 20 A | 20 A | 12 A | 20 A | 20 A |
24 V-supply (max.) | 3 A | ||||||
Brake resistor | electronic |
*) Mains fuses according to type “RK5” must be used.
NOTICE | ||
![]() | AX5112 When protected by RK5 class fuses: Rated 20 A, min. 480 V |
Internal protection, UL-compliant
Circuit | Fuse |
---|---|
24 V system voltage | 3.4 AF |
24 V peripheral voltage | electronic |
Brake resistor | electronic |
External drive system protection
Rule of thumb:
Example: | Determine the total device rated current, multiply by correction factor, and round it up to the next higher standard level.
1 x AX5103 + 2 x AX5201 + 2 x AX5203 3 A + 6 A + 12 A = 21 x 1.1 = 23,1 A --> selected 25 A |
NOTICE | ||
![]() | Special requirements for a drive system Please consult our Application Department with respect to the special requirements for a drive system with UL-Listing. |
Residual current circuit breaker
Servo drives with built-in mains filters generate a small leakage current (fault current) due to the capacitors in the filter. This fault current is responsible for malfunctions in standard residual current circuit breakers. For this reason so-called AC/DC sensitive residual current circuit breakers must be used, which also take into account DC currents.
X02: DC link
DC link coupling or external brake resistor is possible via terminal X2.
| Terminal point | Connection | Tightening torque | |
---|---|---|---|---|
DC+ | DC link + | external |
| |
DC- | DC link - |
X03: 24 VDC supply
System and peripheral voltage for the servo drive is supplied via connector X3. The supply is based on two channels in order to offer an option to separate between motor stopping brakes and control electronics. Both channels are connected via a bridge as standard.
| |
Safe operation! The voltage tolerances must be considered when connecting motors with stopping brake. |
| Terminal point | Connection | current consumption | Tightening torque |
---|---|---|---|---|
Up | 24 VDC ± 10% - Periphery (e.g. separate brake supply) | variable (see X06 and X14, X24) |
0,5 - 0,6 Nm | |
Us | 24 VDC -15% + 20% - system supply / control voltage | -12 A = 0,4 A - 0,8 A | ||
GND | GND |
|
Safe system stop in the event of power failure
A power failure can lead to uncontrolled run-out of drive axes, which means that linear axes or lifting axes would hit the limit stop unbraked. The 24 VDC supply of the AX5000 has two channels, so that separate power supplies can be used for the control electronics and the brake control. This enables the supply voltage for the control electronics to be buffered via the UPS of the Industrial PCs until all axes were stopped safely.