Bottle Neck Detection
If the cutter radius is not considered when a part program is created, the cutter may inadvertently process the opposite side of the workpiece. This leads to a contour collision with the workpiece, or, in other words, a bottleneck was programmed.
Command | CDON |
Cancellation | CDOF |
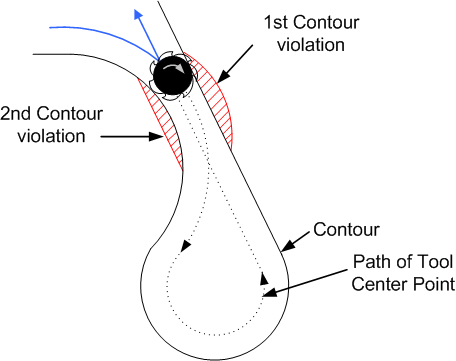
In this form, this behavior can only occur in combination with cutter radius compensation (G41/G42). In order to prevent such contour collisions, monitoring can be switched on from the part program via CDON. For it to be active, cutter radius compensation must also be selected.
The response of the NCI when a bottleneck is detected can be parameterized via the PLC. 3 cases are distinguished:
- Error and abort
If a bottleneck is detected, TwinCAT generates a runtime error and aborts the program execution. - Notification and modification of the contour
If a bottleneck is detected, the contour is modified such that a contour collision is avoided (see Figure 1: blue line). However, this also means that segments may be left out, depending on the program. Furthermore, a note is entered in the application viewer to say that a bottleneck was detected. - Notification and contour collision
If a bottleneck is detected, the contour is not changed and no error is generated. Only a message is entered in the application viewer.
Significant computing resources are required for contour collision monitoring. It should therefore only be selected if it is actually required. Furthermore, the amount of look-ahead for the bottleneck detection should be specified. This requires the number of future segments to be determined that are monitored relative to the n-th segment, in order to check for bottlenecks. The selected number of segments should not be too large, since this would put unnecessary strain on the system. The value for the look-ahead is also parameterized from the PLC.
Function blocks for parameterizing the bottleneck detection:
Sample:
N10 G0 X0 Y0 Z0
N20 CDON
N30 G01 G41 D3 X100 F6000 (cutter radius 30mm)
...
N40 G01 X200
N50 G02 X220 Y-74.641 I0 J-40
N60 G01 X300 Y-104
N70 G01 X230 Y120
N80 G40 D0 Y200
N90 CDOF
...
M30