Spindle
Spindle programming is performed in accordance with the conventional standard syntax defined in ISO resp. ISO + extensions. This is required in particular for reasons relating to compatibility and owing to certain standard functionalities such as turning, tapping and gear changing etc.
To comply with the requirements of new machine concepts and production technologies in flexible spindle programming, each spindle present on the channel also features the option of axis-specific programming. This syntax allows several spindles to be addressed mutually independently in multi-spindle systems in one NC-block simultaneously [1]-20, [6]-8.8. In this case, it must be noted that only one spindle can be programmed at one time, the so-called main spindle, both in the standard syntax and in the spindle-specific syntax. All other spindles can be addressed only via the spindle-specific syntax (Chapter 14.3).
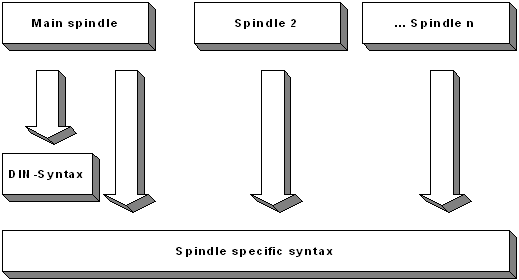
The spindles and the main spindle are defined in the channel parameters list [1]-16. This configuration is available after boot-up of the control system. The main spindle can be changed in the NC-program by means of an NC-command (#MAIN SPINDLE, Chapter 14.4).
The table below shows what NC-commands must be used in conjunction with spindle programming only in the DIN syntax and what NC-commands are also allowed within the extended spindle-specific syntax.
Description | DIN-Syntax | Spindle specific Syntax |
---|---|---|
Spindle-M-Functions | M3, M4, M5, M19 | M3, M4, M5, M19 |
Speed | S | REV |
Position | S.POS | POS |
User specific | Mxx/Hxx | Mxx/Hxx |
Gear change (mechanical) | M40-M45 |
|
Thread cutting | G33 |
|
Tapping | G63 |
|
Turning | G95, G96, G97, G196 |
|
C-axis | #CAX |
|
Gear change (new data) | G112 |
|
Homing | G74 | G74 |
Override 100% | G167 | G167 |
Requesting |
| CALLAX |
Releasing |
| PUTAX |
Taking over new |
| GET_DYNAMIC_DATA |
Feedforward control |
| G135, G136, G137 |
Feed linking |
| FEED_LINK |