Settings with the Drive Manager
(Master TwinCAT 2.11 R3)
The data provided in this section as an example refer to an AM3121-0200-0001 servomotor from Beckhoff Automation. For other motors the values may vary, depending on the application.
![]() | Using the Drive Manager from revision -0019 The Drive Manager is only supported from revision -0019 of the EL72x1. If you use an older version, the settings have to be made manually. See chapters "CoE settings" and "NC settings" |
Table of contents |
---|
The TwinCAT Drive Manager is available for download from the Beckhoff website.
The TwinCAT Drive Manager for parameterizing an EL72x1 servo terminal is integrated in the System Manager, so that no separate configuration tool is required. Once a servo terminal has been detected or entered, the TwinCAT Drive Manager is available in the Configuration tab.
The following instructions are intended to enable you to start up the servo terminal relatively quickly. More detailed information on the Drive Manager can be found in the corresponding documentation "AX5000 Introduction in the TC Drivemanager"
Start-up with the Drive Manager
- The terminal must already have been added manually under I/O devices or have been scanned in by the system (see section "Configuration set-up in TwinCAT")
- The terminal must already be integrated in the NC (see section "Integration in the NC configuration")
- Select the Configuration tab for the EL72x1.
- Select the connected voltage under Power Management.
- Then select the connected motor under Motor and Feedback. Click on Select Motor.
- Select the suitable motor in the selection window and confirm with Ok.
- Confirm the next dialog box with OK. All required parameters are automatically entered in the NC, and the scaling factor is calculated. If this is not confirmed, these settings have to be entered manually. See section "NC settings".
- The scaling can be determined under Scalings and NC Parameters. A motor revolution is defined as 360° as an example. All required parameters are adjusted automatically. The setting only becomes active once the configuration is activated.
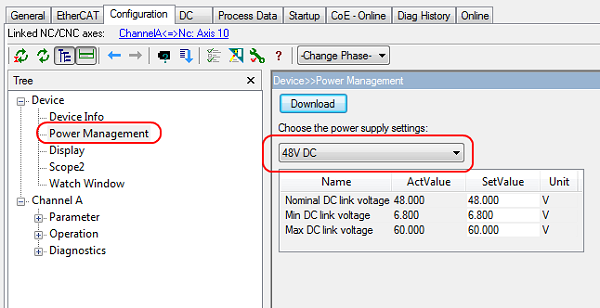
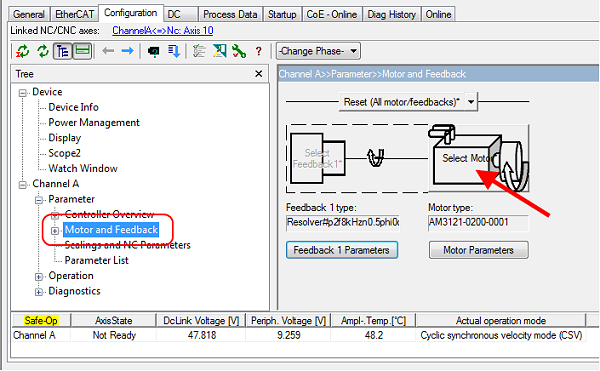
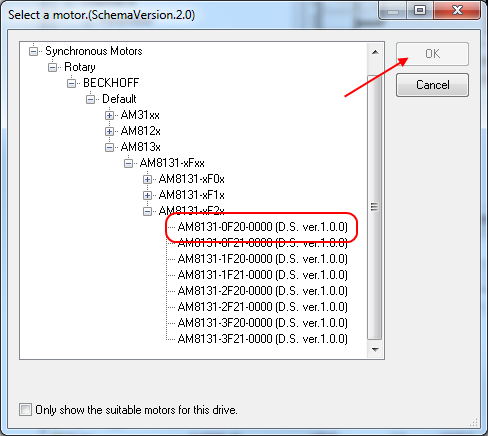
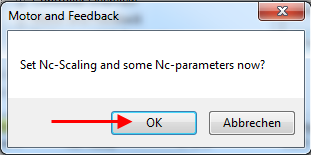
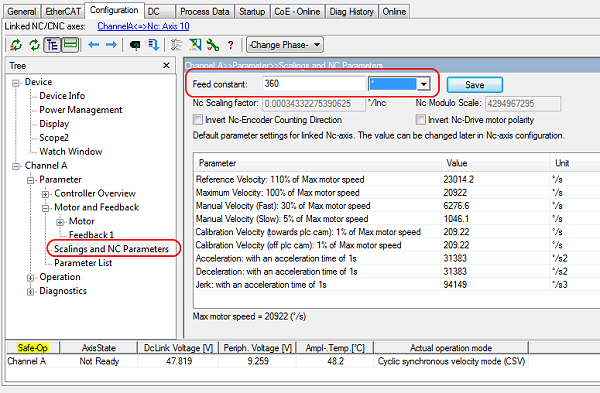
All main parameters for the commissioning the motor are now set. The motor can now be commissioned with the NC, for example. A brief description can be found in section "Commissioning the motor with the NC". Or the NC can be addressed from the PLC. A small (download: (example program)) is included in the documentation.
Some parameters can be adjusted manually for your particular application.
Setting further parameters with the Drive Manager
The values specified here are exemplary, although in most cases they have led to excellent results. Depending on the application, other values may yield better results.
These values can be changed during operation. Click on Download to apply the values.
Integral velocity controller component Tn
- Reduce the value, until the motor starts to oscillate slightly. Then increase the value by 10%.
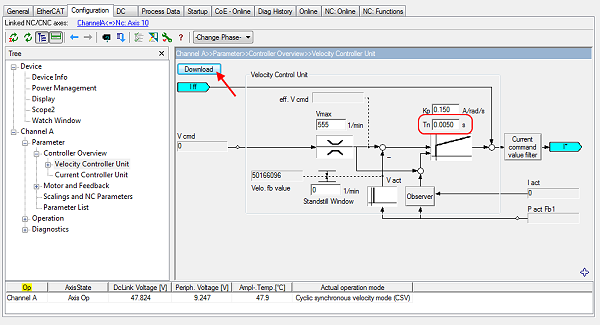
Proportional velocity controller component Kp
- Increase the value, until the motor starts to oscillate slightly. Then reduce the value by 80%.
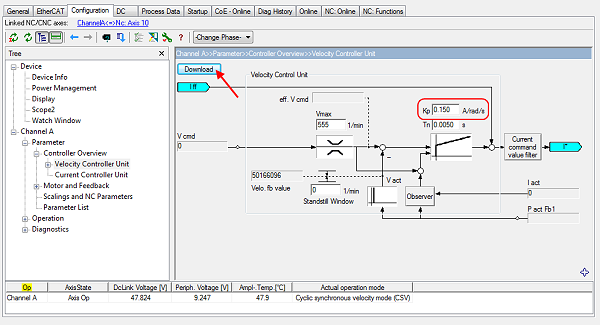