CSP
CSP - cyclic synchronous position (position control)
In the CSP operating mode the EL72x1-xxxx operates in the cyclic position interface. A defined position can be set via the Target position variable.
![]() | Minimum cycle time The cycle times in CSP mode with 2^n * 125 µs (for n =1 to 8) are: |
Step-by-Step
- Add the terminal to the configuration as described in the chapter TwinCAT configuration settings - manual or - Online scan.
- Link the terminal with the NC as described in the chapter Integration in the NC configuration.
- Configure the motor with the help of the automatic configuration (only OCT types), using the Drive Manager or import the motor XML file into the Start-up directory as described in the chapter Settings in the CoE.
- Set the mode of operation in the CoE directory to Cyclic synchronous position mode (CSP), Fig. Selection of the mode of operation.
- Under Predefined PDO assignment, also select Cyclic synchronous position mode (CSP), Fig. Selecting a predefined PDO assignment.
- Activate the configuration (Ctrl+Shift+F4).
- Run through the State Machine of the terminal. There are two ways to do this:
- If you use the TwinCAT NC.
The State Machine is run through automatically by the NC. You can enable the axis in the “Online” tab of the axis.
Set all tick marks and set Override to 100% (see Fig. Set enables). The axis can then be moved. - If you don’t use the TwinCAT NC.
In this case you must run through the State Machine manually. To do this, follow the instructions in the chapter Commissioning without the NC. - You can specify a defined position via the cyclic variable Target position (fig. Position specification). The value must be multiplied by the calculated scaling factor in order to obtain the correct position.
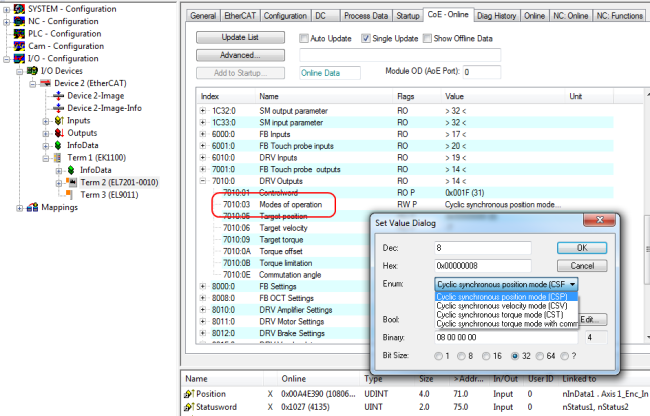
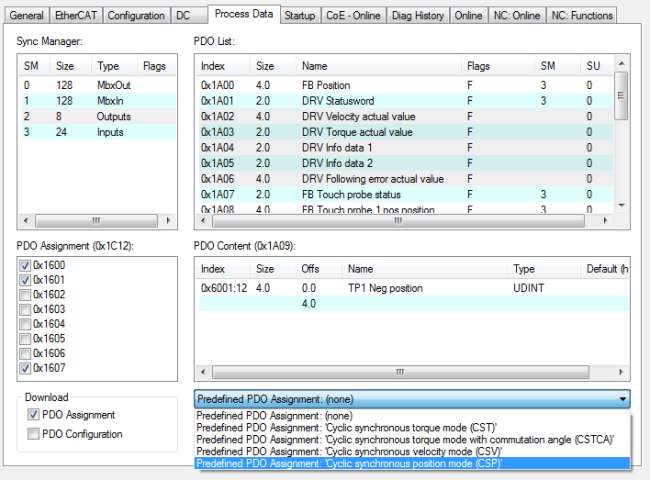
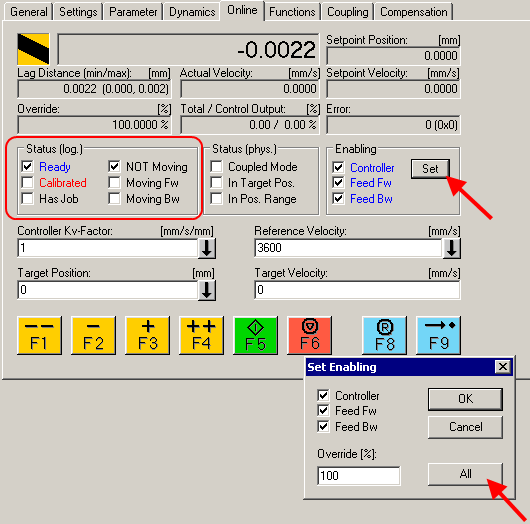
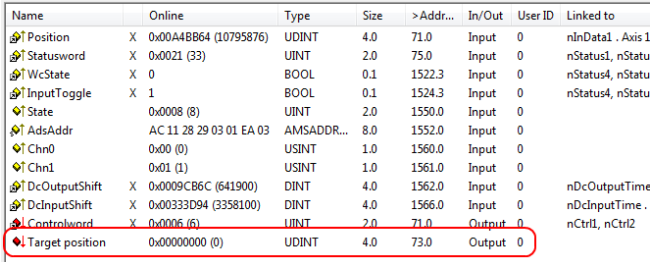
Following error monitor
Furthermore, there is an option in CSP mode to activate a following error monitor. The following error monitor is switched off on delivery. In all other modes this is not used and is ignored.
- The window of the following error monitor can be adjusted with the Following error window (Index 0x8010:50 MDP742 / Index 0x6065 DS402). The value set here – multiplied by the scaling factor – specifies by what position the actual position may differ from the set position, positively and negatively. The total accepted tolerance is thus twice as large as the position entered in the Following error window (see fig. Following error window).
- The time (in ms) allowed for a following error exceedance can be set with the Following error time out (Index 0x8010:51 MDP742 / Index 0x6066 DS402). As soon as the target position is exceeded by more than the position entered in the Following error window for the time entered in the Following error time out, the terminal outputs an error and stops immediately.
- The current following error can be read in the Following error actual value (Index 0x6010:09 MDP742 / Index 0x60F4 DS402).
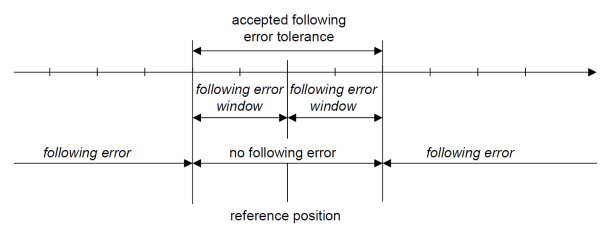
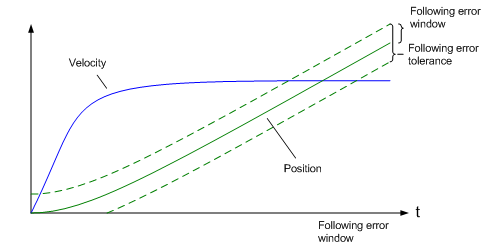
The value 0xFFFFFF (- 1) in the Following error window means that the following error monitor is switched off and corresponds to the delivery status.
The Following error time out is 0x0000 (0) on delivery.