Filtering the actual values of the conveyor axis
Synchronising and tracking the co-moving workpiece coordinate system PCS1 are based on the actual values of the conveyor axis. The actual values are more or less extremely noisy depending on the design of the linear conveyor.
Due to the coupling, this noise has a negative effect on the contour error when synchronisation is active. This is why the actual values are smoothed by a filter. Two different filter configurations are available for this purpose and can be switched over depending on the operating state of the conveyor. Filtering also reduces the risk of exceeding the dynamics due to velocity jumps in the probing signal.
In normal mode at constant conveyor velocity, the strongly smoothed conveyor velocity is used for synchronisation. The longer filter length defined in P-AXIS-00623 results is a greater time delay and is less dynamic. When the coupled system is in normal mode, this filter results in only very slight undesirable excitations in the manipulated variable in the coupled system caused by noise in the actual position signal of the conveyor axis.
The MCV_SetReducedFilter function block in the PLC can be used to switch from strong to weak filtering to minimise the contour error in dynamic phases and especially in the event of a motion stop. This weak filter set-up consists of a sinc (ideal low-pass) filter (P-AXIS-00625) followed by an average value filter (P-AXIS-00624).
Both filters generate a longer or shorter delay time due to the set filter order. The weak filter reacts more dynamically due to the smaller filter width and also generates a shorter delay time. The filtered velocity is used for feedforward control of the delay time.
The individual filters can be configured in the axis parameters and, while the conveyor axis is in operation, the filter parameters can be adapted using the #MACHINE DATA command.
The figure below shows an example signal curve with a noisy probe signal and the filtered signal with a filter order of 10 (parameter conv_sync.order_v_filter = 10).
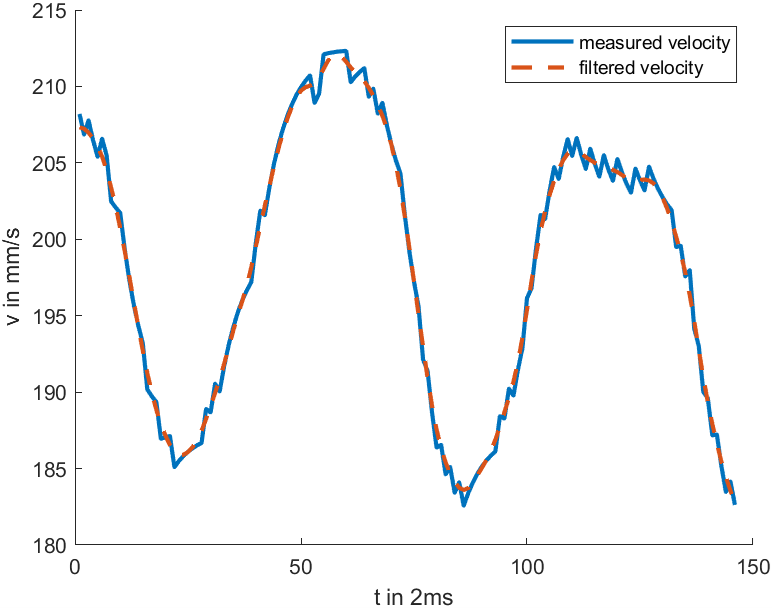