Introduction
The TF5110 - TF5113 TwinCAT Kinematic Transformation software package is installed together with the TF5400 software package.
TwinCAT Kinematic Transformation
The TF5110 - TF5113 TwinCAT Kinematic Transformation is a software solution that combines robot control and conventional PLC in one system (see also https://www.beckhoff.com/tf5113/). The implementation of the entire control in one system eliminates interface losses between different CPUs for PLC, motion control and robot control. In practice, this implementation leads to a reduction of engineering costs and to reduced cycle times in the production process. In addition to the elimination of interfaces and components, the merging of PLC, robotics and motion control into one application makes the system homogeneous. Therefore, for the user there is no apparent difference in the treatment of the individual functions. Conveniently, a part on a conveyor belt operated with standard motion control can be taken and set aside by the robot quickly and handily.
Since the working area of the robot is determined by the configuration and the number of axes, it depends on a number of parameters: arm lengths, angular range, center of mass, maximum load, etc. The configuration of the arms and joints determines the kinematic structure, which is divided in two main classes: serial kinematics and parallel kinematics.
Serial kinematics
The current position of any axis always depends on the position of the preceding axis, i.e. all axes are arranged sequentially.
Examples: SCARA and crane kinematics
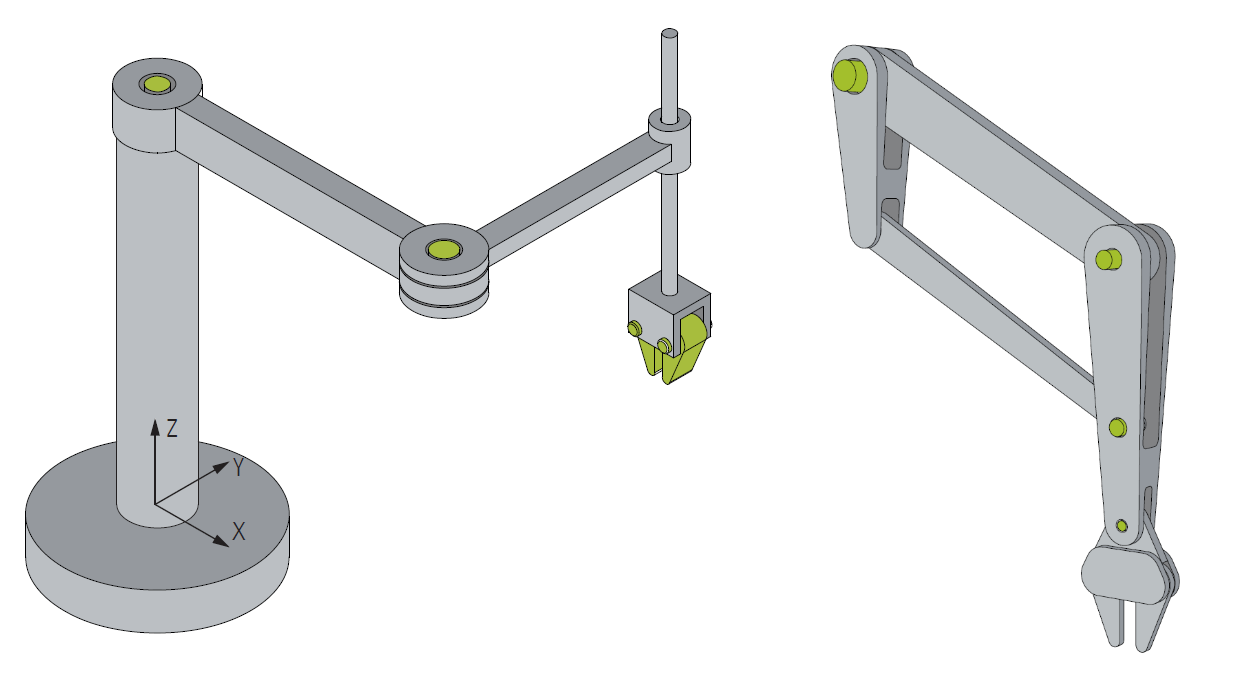
Parallel kinematics
All axes directly engage with the working platform via the kinematics.
Examples: delta kinematics, shear kinematics
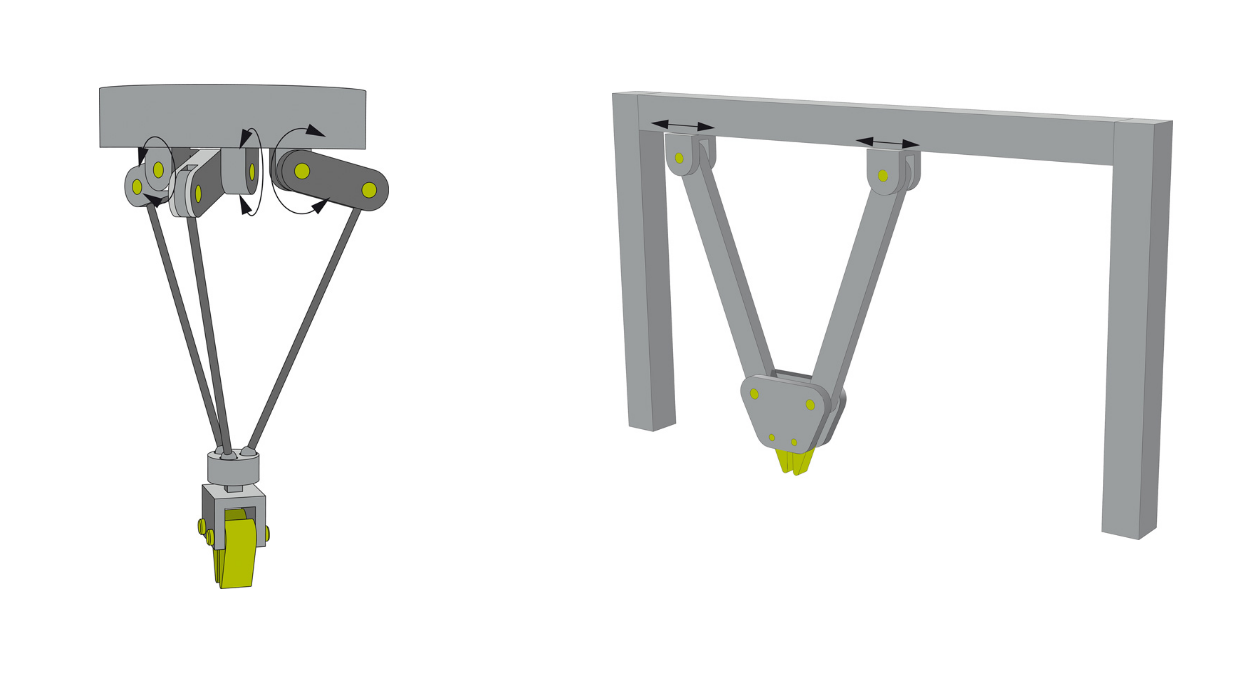
Coordinate systems
Coordinate systems are required in order to describe the positional behavior of a system. Different coordinate systems can be used as a basis for programming:
- The machine coordinate system (MCS ) is a robot-based cartesian coordinate system, which usually has its origin in the robot base.
- The world coordinate system (WCS ) is a cartesian coordinate system, which describes the whole modelled 'world'. It therefore does not refer to a specific robot, but to the whole system. The origin of a robot-based machine coordinate system (MCS) is at a particular point of the WCS. In other words, the user can specify, at which point of his “world” an industrial robot is located and how it is oriented. A WCS can contain several robots. When using a robot, world coordinates can coincide with the machine coordinates to improve transparency.
- The user can position the user coordinate system (UCS) at any position and with any orientation within the world coordinate system.
- The axis coordinate system (ACS) describes the position of the physical axes. It is generally not a cartesian coordinate system. Many robot joint axes perform rotary movements. Using the ACS makes it easier to take into account the limit values for angle, velocity and acceleration. If a robot axis performs rotary movements, it is often difficult for the user to predict and control the path. The axis coordinate system is usually used for referencing/homing.
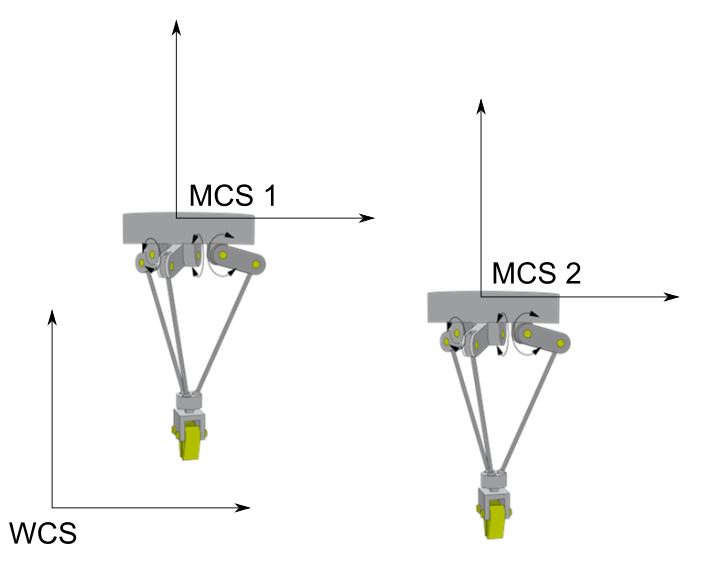
Kinematic transformation
In many cases, robots are programmed in the MCS. Due to the way humans think, movements are usually programmed in Cartesian coordinate systems. To execute such movements, it is therefore necessary to convert between the axis coordinate system and the Cartesian space.
Transformation describes, in the context of the kinematics, the calculation necessary in order to change from one coordinate system to another. There are basically two problems in considering the kinematics of robots:
- The conversion from the axis coordinate system (ACS) to a Cartesian coordinate system is referred to as forward transformation. The Cartesian position of the tool center point (TCP) is calculated from the axis-specific joint coordinates of the robot.
- The conversion from Cartesian coordinates of the TCP to axis coordinates, which is required in order to move the actual robot axes, is referred to as backward transformation.
Realization in TwinCAT
TwinCAT Kinematic Transformation can be used to realize robotics applications. All PLC and NC features can be combined on a common hardware and software platform. TwinCAT Kinematic Transformation realizes several robot kinematics (e.g. H-Bot, delta robot, 6-axis robot) on the PC. The axes are controlled directly from the TwinCAT Motion Control system.
The user can program robot movements directly in the Cartesian coordinate system. The software calculates the transformation to the axis coordinate system of the robot in each cycle. To minimize vibrations and to increase the positioning accuracy, for many kinematics a current pre-control can be activated, if the drive amplifier and the fieldbus are fast enough and interfaces for an additional current pre-control are available. EtherCAT and the Beckhoff servo axles meet these requirements.
The TwinCAT function seamlessly integrates into the motion control world of Beckhoff. TF5420 TwinCAT 3 Motion Pick-and-Place is available especially for the simple realization of handling tasks. TF5100 TwinCAT 3 NC I enables programming both via G-Code (DIN 66025) and directly from the PLC (PlcInterpolation library). The functions TF5055 TwinCAT 3 NC Flying Saw and TF5050 TwinCAT 3 NC Camming enable synchronization with conveyor belts for picking and placing of workpieces, for example. In addition, standard PTP functions from the familiar Beckhoff PTP motion libraries can be used.
The configuration of the robot takes place entirely in the TwinCAT 3 Engineering environment (XAE).