Encoder - dialog: NC encoder
Below the axes, in the tree view, there are some setting dialogs at Axis_Enc on the right side of the System Manager. One of them is the dialog "NC-Encoder", which is described below:
Type
Here you have to select the used interface type to which the encoder of the axis is connected. The following types are supported:
Supported types | Description |
---|---|
Simulation Encoder | For simulation purposes or as a virtual encoder, an internal, direct setpoint/actual value feedback can be switched on with this encoder type. This encoder type is set by default. |
Encoder connected to M3000 | The Beckhoff Lightbus M3000 absolute encoder is used as the encoder interface. |
Encoder connected to M31x0 / M3200 | The Beckhoff Lightbus M31x0 or M3200 incremental encoder is used as the encoder interface. |
Encoder connected to M2510 | The Beckhoff Lightbus M2510 analog input/output module is used for position feedback with this encoder type. |
Encoder connected to KL51x1 | A KL5101 Incremental Encoder Interface is used for position feedback. |
Encoder connected to KL5001 | A KL5001 SSI encoder (absolute encoder) interface is used for position feedback. |
Encoder connected to KL5051 / KL2502 | The bidirectional KL5051 BI-SSI interface terminal is used here for position feedback. This should usually be the case with Digifas 7x00 drives from Seidel. |
Encoder connected to KL30xx | One channel of the KL30xx analog input terminal is used here for position feedback. |
Encoder connected to FOX-50 | A FOX-50 module is used here as the interface for position feedback. |
Encoder connected to SERCOS (position) | Position feedback according to SERCOS specification. |
Encoder to SERCOS (position+velocity) | Position and velocity feedback according to SERCOS specification. |
Encoder connected to dig. input (binary) |
|
Hydraulic encoder | The force from Pa, Pb, Aa and Ab is fed in as feedback with this setting. |
Encoder connected to AX2000 | The resolver of the motor, or connected external encoders of the AX2000-B200 drive, provides the position feedback. |
Encoder connected to ProfiDrive | Position feedback according to ProfiDrive specification. |
Encoder connected to NC Backplane | The Beckhoff NC Backplane transmits the positioning data here. |
Encoder (universally applicable) | Universal applicable encoder |
Encoder connected to CANopen | The position feedback is synchronous via the CANopen fieldbus interface (possible e.g. with the FC510x |
Linked to
Here you have to select the terminal/module of the I/O configuration which is electrically connected to the encoder of the axis. Only terminals or modules that match the set type are offered for linking.
Linking a universal encoder
The type Encoder (universally applicable) can be used for encoder systems that are not listed in the type list. In this case, the counter value of the encoder must be linked manually and the value range must be set. The link is made directly via the input variables of the axis encoder
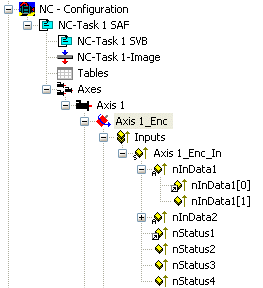
The input/output variables of the encoder have the following meaning:
nInData1 - (16 or 32 bit) position value of the axis in increments
nInData2 - (16 or 32 bit) optional latch value for measuring probe function or referencing with zero pulse (reference mode: HARDWARE SYNC)
nStatus1 - status byte of the encoder
nStatus2..4 - further optional status bytes of the encoder
nCtrl1 - control byte of the encoder
nCtrl2...4 - further optional control bytes of the encoder
After linking the position count value with nInData1 the maximum count value until overflow is still defined in the global encoder settings (Encoder mask).
In some cases, the word or double word of the counter still contains status information that can be hidden. For this purpose, the corresponding bits in the Encoder Bit Rejection Filter Mask are activated. In most cases, this mask remains zero.
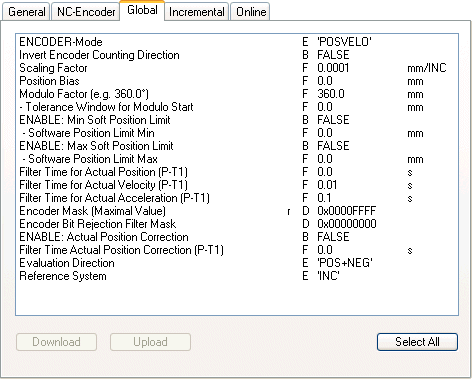