Overview
The TwinCAT System Manager is the central configuration tool of the TwinCAT System. It is where the inputs and outputs of the software tasks and the physical inputs and outputs of the connected fieldbusses are managed. The individual software tasks (e.g. PLC tasks) each operate on their own private process image so that the addresses of the symbols mapped in the process image (variables) are relevant and valid only within that particular task.
The I/O information of the individual Software Tasks is read from and entered in the TwinCAT System Manager. From there, the installed fieldbusses and their connected modules/boxes are also described. The logical and physical inputs and outputs are assigned to one another by linking software task variables and fieldbus variables.
Task-task communication:
With the aid of the TwinCAT System Manager, the ”in and outputs” of a task can be cyclically exchanged with the ”out and inputs” of another task. The data consistency remains thereby intact.
Variable orientated:
The smallest addressable and linkable unit is a variable. Variables can be individual bits, bytes, 16 bit data words, 32 bit data words etc. Variables can also be structures or arrays (fields) consisting of other data types.
Process Images:
Variables are always precisely assigned to a process image, i.e. the address of the variable is indicated unambiguously in its process image - but only within that process image. Each software task and each fieldbus possesses precisely one process image (exception: PLC run time system tasks share a combined process image).
Assignments:
The TwinCAT System Manager produces individual assignments which contain the links created. Assignments are produced between software tasks and fieldbus devices and between software tasks if these have mutually linked variables. I.e. if a PLC task variable is linked to the variables of a fieldbus an assignment will be produced between these two. If the same PLC task has other variables linked with another fieldbus, a second assignment will be generated. The assignments contain the corresponding copying directives to enable the exchange of the corresponding variables at the run time.
Fieldbus independence :
When defining and programming the software tasks participating in the TwinCAT system it is not necessary to know the type and structure of these or the fieldbus used. Programming is carried out with the aid of logical variables which are defined locally within the software itself. The TwinCAT System Manager links these logical variables with other variables, which correspond either to physical inputs and outputs on the fieldbus or to logical variables of other tasks. The type and the special properties of each fieldbus do not need to be known or considered.
TwinCAT System Manager supports all standard commercial fieldbuses and some other PC standard interfaces:
- Beckhoff Lightbus
- Profibus DP, MC (DP-V2)
- Interbus
- CANopen
- SERCOS
- DeviceNet
- Ethernet
- EtherCAT
- Beckhoff Real-Time Ethernet
- PC printer port (8 inputs and 8 outputs on TTL basis)
- Serial Bus Coupler BK8100 to COM
- USB Bus Coupler BK9500 and USB Control Panel interface (CPx8xx)
- Dual-ported memory interface (DPRAM) for PC cards
- NOVRAM (Non-Volatile RAM)
- System Management Bus (SMB) for monitoring of PC hardware like fans, temperatures, etc...
Detailed information on the various fieldbus cards and other supported I/O devices can be found in our Reference Documentation.
Starting TwinCAT System Manager:
To open the TwinCAT System Manager, move the mouse to the Windows 'start' menu and select 'start' -> 'Programs' -> TwinCAT System' -> ' TwinCAT System Manager' or start it from the Windows SysTray by clicking the TwinCAT icon and selecting 'System Manager' from the appearing Pop-up menu as shown below:
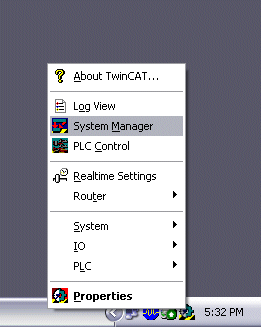
System Manager components :
The System Manager window is structured as shown in the image below (up to TwinCAT version 2.8):
The project name is written in the title bar (upper blue bar), in this case Machine.wsm. The menu bar and the toolbar (symbol bar) are below the title bar. There functions are described in the following chapter Operation.
In the large left-hand window a tree structure is displayed which contains all system configuration components.
At the bottom you can see the status line which provides information on the current system status. In the below case the system is running, this is indicated by the word ”RTime”.
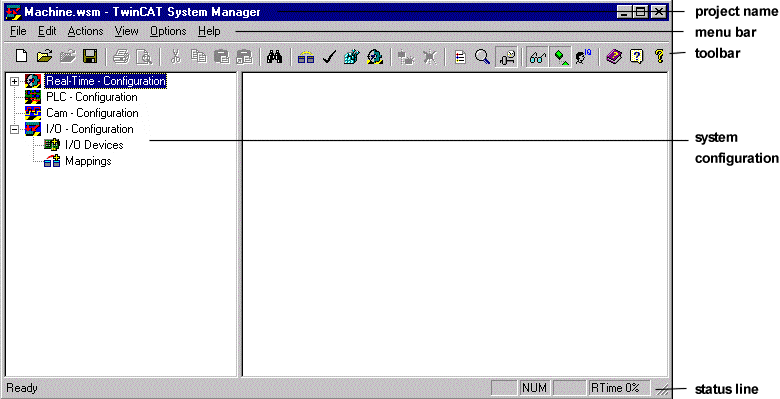
For a description of the System Manager main window from TwinCAT version 2.9, please refer to: TwinCAT System Manager -> Introduction.
System configuration model of the TwinCAT System Manager
The list below gives the various main components of the TwinCAT System Manager. The existence of the configuration components depends upon the Level of the Installed TwinCAT System.
Configuration module | Description |
---|---|
Basic system settings are carried out. The basis time for the system is specified. User-defined tasks can also be integrated. | |
Up to four PLC programs can be integrated into the maximum four run-time systems. Up to four tasks per run-time system can be carried out and the links between the individual task and the variables is configured. | |
The optional electronic camshaft controller is configured. | |
All devices and fieldbus components are listed and configured. These include:
|
Further information on the use of the TwinCAT System Manager can be found in the TwinCAT Quick Start documentation.