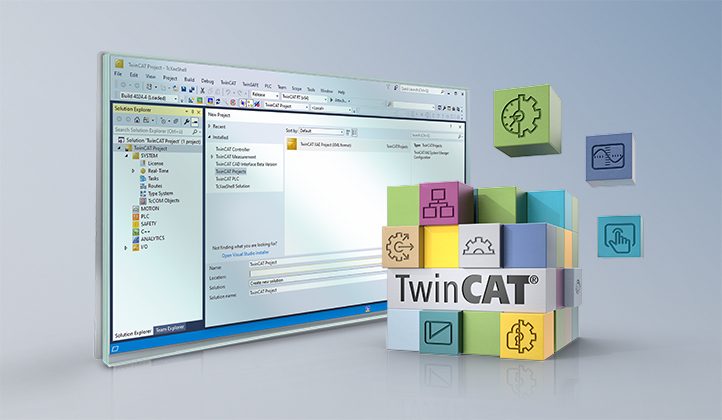
TExxxx | TwinCAT 3 Engineering
TwinCAT 3 is divided into components. The TwinCAT 3 engineering components enable the configuration, programming and debugging of applications.
Name | Description |
---|---|
TE1010 | | The TwinCAT 3 Realtime Monitor enables precise diagnostics and optimization of the runtime behavior of tasks in the TwinCAT 3 Runtime environment. |
TE1030 | | TwinCAT Documentation Generation enables the creation of documentation within a machine application or PLC library. |
TE1111 | | With this engineering component, the generated control code can be tested and optimized at an early stage in the engineering process without actual hardware, meaning that real commissioning can take place much faster. |
TE1120 | | TwinCAT 3 XCAD Interface is the latest version of the interface between ECAD tools and TwinCAT 3. |
TE1130 | | The TwinCAT 3 Interface for Inventor® is a tool for easy configuration of a coupling between TwinCAT 3 and the 3D CAD system Autodesk® Inventor®. |
TE1200 | | Static code analysis should be regarded as a supplement to the compiler. It facilitates clearer code writing and can help uncover potential sources of error during programming. |
TE1210 | | The TwinCAT 3 PLC Profiler is an analysis tool that is used for performance evaluation and optimization of PLC programs within the TwinCAT 3 software environment. |
TE13xx | | TwinCAT 3 Scope is a charting and analysis tool for TwinCAT. Variables in TwinCAT can be recorded and displayed graphically. |
TE131x | | The TwinCAT Filter Designer belongs to the TwinCAT Measurement product family. This tool allows digital filters to be designed with ease. |
TE132x | | The TwinCAT 3 Bode Plot is a tool for analyzing and optimizing mechanical resonances within a mechatronic system. The TwinCAT Bode Plot can be used in conjunction with the AX5xxx drives from Beckhoff. |
TE1400 | | With the TwinCAT 3 Target for Simulink®, models developed in Simulink® can be used in TwinCAT 3. Various toolboxes can be integrated into Simulink®. Embedded MATLAB® function blocks are also supported. |
TE1401 | | With TwinCAT 3 Target for MATLAB®, the functions developed in the MATLAB® script language can be used in TwinCAT 3. The functions are automatically compiled in C/C++ code with the aid of the MATLAB® Coder™ and transformed into TwinCAT objects with the TwinCAT 3 Target for MATLAB®. These objects can be used seamlessly in the TwinCAT 3 Engineering, e.g. extended with PLC source code to make an overall project, debugged and linked with fieldbus devices. |
TE1402 |
| This documentation explains the limitations and extensions of the “TwinCAT 3 Target for Simulink®” reference documentation. |
TE1410 | | The TwinCAT 3 Interface for MATLAB®/Simulink® enables data exchange between MATLAB® and the TwinCAT Runtime and between Simulink® and the TwinCAT Runtime. |
TE1420 | | The Functional Mock-up Interface (FMI) is a free standard for exchanging or coupling simulation models created with different simulation tools. This is often the case when the models are provided by different suppliers or domain-specific simulation tools are used to simulate the different aspects of a machine or plant (e.g. thermal simulation, control engineering simulation). |
TE1421 | | The Functional Mock-up Interface (FMI) is a free standard for exchanging or coupling simulation models created with different simulation tools. This is often the case when the models are provided by different suppliers or domain-specific simulation tools are used to simulate the different aspects of a machine or plant. |
TE1500 | | The graphically-oriented Valve Diagram Editor, which is similar to the cam plate editor, is used to design the characteristic curve of a hydraulic valve. |
TE1510 | | A cam plate editor is used to design the motions for a cam plate. |
TE1610 | | The TwinCAT EAP Configurator is a tool for visualizing and configuring communication networks where data exchange based on the EtherCAT Automation Protocol (EAP) takes place or is to be established. EAP is used for master/master communication. |
TE2000 | | The TwinCAT 3 HMI (human-machine interface) integrates into the familiar Visual Studio® development environment. It enables platform-independent user interfaces to be developed based on current web technology (HTML5, JavaScript). |
TE3500 | | The TwinCAT 3 Analytics Workbench is a TwinCAT 3 engineering product for creating continuous data analyses from various decentralized machine controllers. The configuration of the workbench is integrated into Microsoft Visual Studio® and is designed as a graphical user interface. |
TE3520 | | The TwinCAT 3 Analytics Service Tool is used for commissioning machinery and for service engineers. Live and historical data can be retrieved for an analysis via the IoT connection or offline via file copy. Analysis configuration takes place in Microsoft Visual Studio, where a toolbox of algorithms is available to the user. |
TE5910 | | The design of the drive, particularly the dimensioning of drive axes, in conjunction with the optimum selection of motor, gear unit, drive controllers, and accessories, is the foundation for efficient machine design. The TwinCAT 3 Motion Designer tool can be integrated in the TwinCAT |
TE6100 | | The TwinCAT OPC UA Nodeset Editor is an engineering tool for creating and editing OPC UA nodeset files, which are used for companion specifications and other elements. With the help of the editor, existing companion specifications or your own information models can be mapped onto a Beckhoff controller and linked with data points from the PLC. |