Specification notes
The following tables with the TC specification apply only when using the internal cold junction. In the ELM334x/ ELM370x, each channel has its own cold junction sensor.
The terminal can also be used with an external cold junction if required. The uncertainties must then be determined for the external cold junction on the application side. The temperature value of the external cold junction must then be communicated to the terminal via the process data for its own calculation. The effect on the TC measurement must then be calculated on the system side.
Thermal stabilization
The specification values for the measurement of the cold junction given here apply only if the following times are adhered to for thermal stabilization at constant ambient temperature
- after switching on: 60 min
- after changing wiring/connectors: 15 min
Ambient air in motion
For a constant TC measurement, thermally stable environmental conditions around the ELM terminal are important. Air movements around the terminal with a possibly varying air temperature must be avoided. If these are unavoidable, the separately available ZS9100‑0003 shielding hood should be used for thermal shielding. The following specification was created without a shielding hood in a quiet environment.
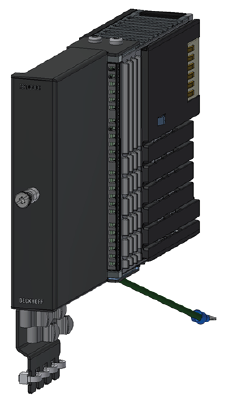
Note: Additional measurement deviations related to the TC wire cross-section/diameter are negligibly small for Lemo and Mini-TC connector types.
Specification of the internal cold junction measurement
Mode TC CJC | Cold junction | |
---|---|---|
Basic accuracy: Measurement deviation at 23 °C, with averaging | < ±4 °C | |
Repeatability | ERep | < 50 mK |
Temperature coefficient | Tc | < 75 mK/K |
Mode TC CJC RTD | Cold junction |
---|---|
Basic accuracy: Measurement deviation at 23 °C, with averaging *) | < ±1 °C |
*) The achievable accuracy in TC CJC RTD mode is highly dependent on the implementation, especially the quality and positioning of the external RTD. The above figure should be considered as an example of a guide value for correct installation, see Assembly of the LEMO connector ELM3702-0101. A measurement uncertainty analysis of the entire system is recommended.
In the following, the achievable temperature measurement uncertainty is now specified for the individual TC types, listed by type in ascending order.