NC - Configuration
Appending and parameterizing an NC task
After appending an NC task the cycle time of the block execution task (NC task x SAF) has to be parameterized. The cycle ticks define the cycle time in multiples of the set basic TwinCAT time (standard: 1 ms) for the task. The cycle time takes effect if/when auto start is selected. The task cycle time must be greater than the expected fieldbus cycle time (Estimated DP Cycle Time - see section I/O Configuration). Shorter times than 2 ms have not yet been tested with Sinamics S120.
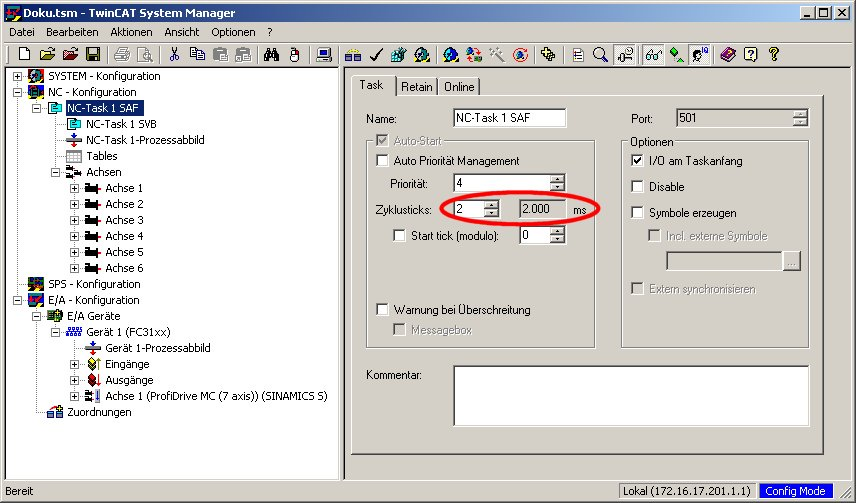
Appending and parameterizing axes
Enter the required number of axes in the context menu for the Axes symbol. The names Axis 1, Axis 2,… are only placeholders. To facilitate identification the names of the function are specified in the software, or the structures from a previous project are adopted. Set the axis type to Profidrive MC (DPV2) and the unit for actual position logging (e.g. mm for a linear axis) in the Settings tab for the respective individual axis. Use the button "Linked with…" to specify which of these logical axes (software structures) are linked to which individual PROFIdrive MC axis (axis system x, #A…#H).
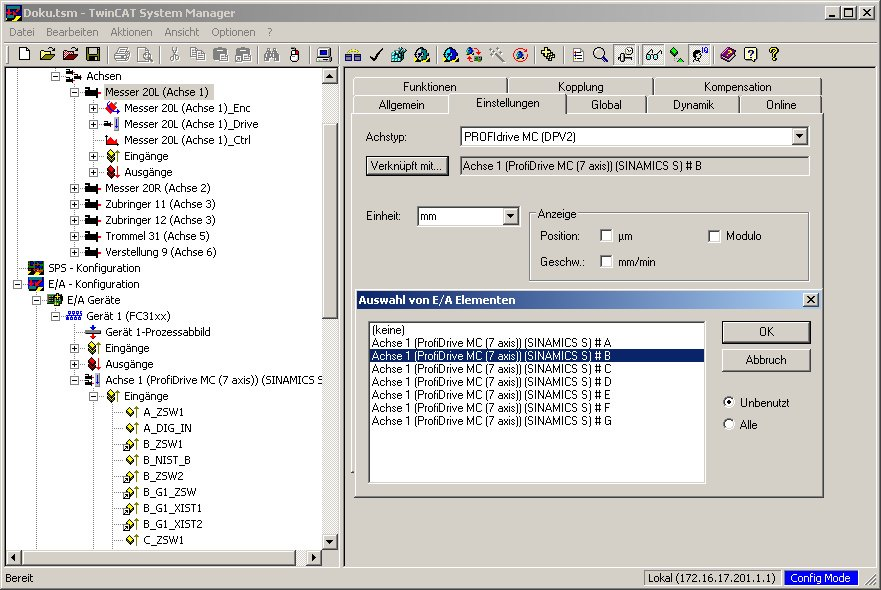
If required for control or diagnostics, CU and Active Line Module are linked with variables (structures) of a PLC project (which have to be created).
Verifying Profibus MC times
Once the NC and the fieldbus have been configured, in online mode press the button "Calculate MC Times" in the MC tab of the master card FC31xx (I/O configuration) and note any warnings. The "Estimated DP Cycle Time" for all axes must be smaller than the NC task time referred to above. A safety margin of approx. 10% should prevail.
Reading parameters from PROFIdrive MC
The following step takes place during commissioning and requires the existence of parameterized axes and a functional fieldbus for the PROFIdrive MC axis system.
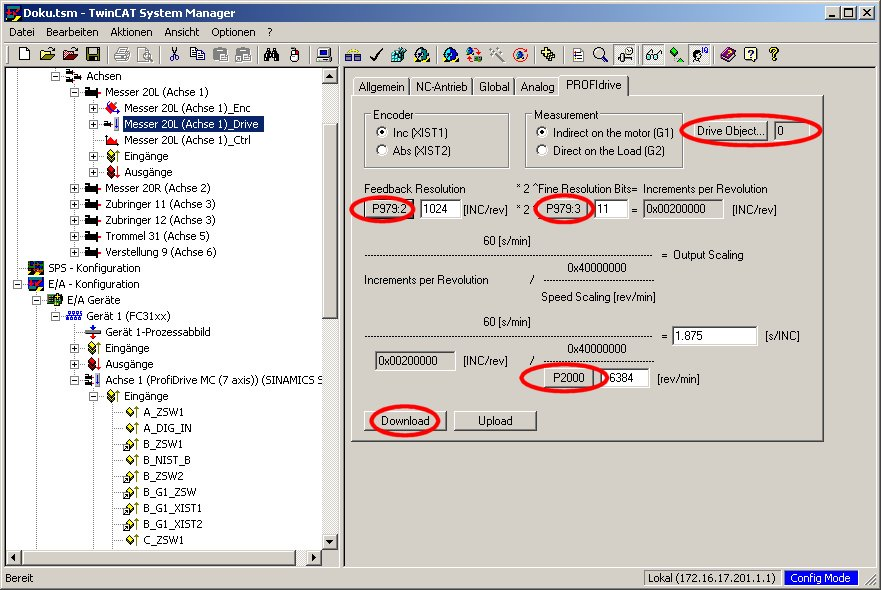
The "PROFIdrive" tab of the axis drive (in the current example Messer 20L(Axis 1)_Drive) features a dialog for reading motor parameters from the drive. To this end the drive object number from the STARTER software has to be specified. The respective buttons can then be used to read the encoder resolution via parameters P979.2, P979.3 and P2000. Alternatively, these parameters can be read with the STARTER software and manual written into the input fields. In both cases the values are transferred to TwinCAT via the Download button.
Together with the mechanical data (e.g. transmission ratio) of the axis, the value INC/rev (increments per revolution) can be used to calculate the scaling factor (in the linear axis example in mm/INC).
Formula
Scaling factor = path per revolution of the drive shaft / (gear ratio x increments per revolution) Gear ratio = motor shaft revolutions / drive shaft revolutions
Example conveyor belt:
300 mm feed per shaft revolution, gear ratio 10, encoder resolution 20000H = 2097152DEC INC/rev scaling factor = 300 mm/rev / (10 x 2097152 INC/rev ) = 0.000014305 mm/INC
Example drum rotation:
Angle= 360° per shaft revolution, gear ratio 17.08, transmission via toothed belt 64/50, encoder resolution 20000H = 2097152DEC INC/rev scaling factor = 360°/rev / (17.08 x 64/50 x 2097152 INC/rev ) = 0.0000078519 mm/INC
Setting the encoder parameter scaling factor
Enter the determined value as the scaling factor for the encoder in the Global tab and accept the values through Download
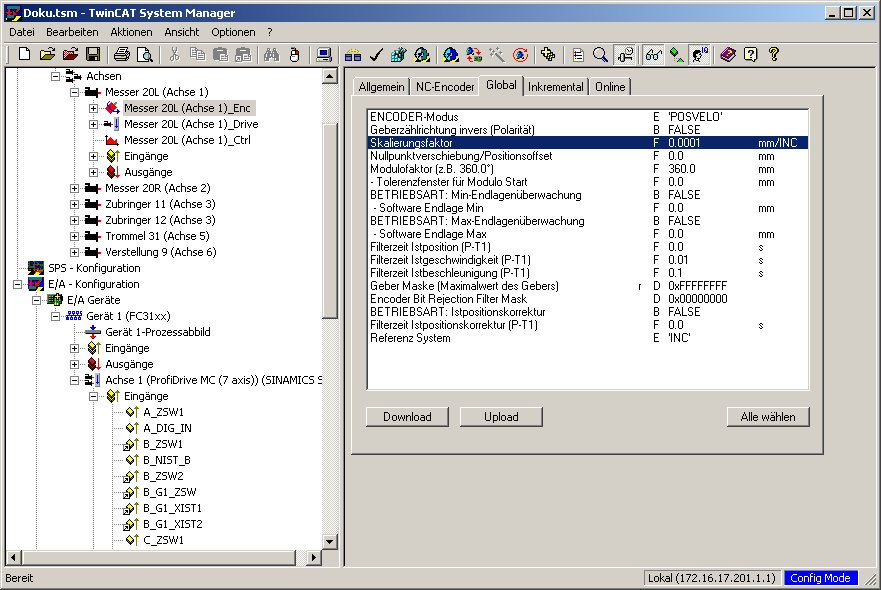
All other axis settings and commissioning steps correspond to the usual procedure.