EL3072 - Connection, display and diagnostics
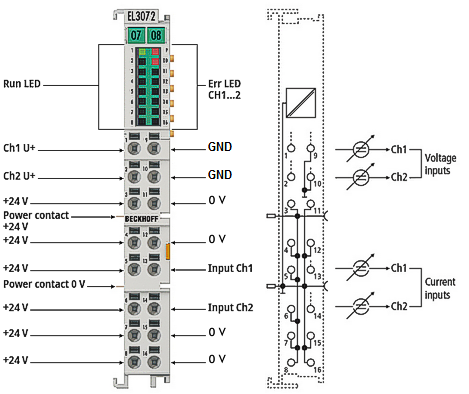
LEDs
LED | Color | Meaning | |
---|---|---|---|
RUN *) | green | These LEDs indicate the terminal's operating state: | |
off | State of the EtherCAT State Machine: INIT = initialization of the terminal or BOOTSTRAP = function for terminal firmware updates | ||
flashing | State of the EtherCAT State Machine: PREOP = function for mailbox communication and different default settings set | ||
Single flash | State of the EtherCAT State Machine: SAFEOP = verification of the Sync Manager channels and the distributed clocks. | ||
on | State of the EtherCAT State Machine: OP = normal operating state; mailbox and process data communication is possible | ||
Error**) | red | off | No error |
on | Error is present, corresponds to PDO Error |
*) If several RUN LEDs are present, all of them have the same function.
**) For channel 1 and 2.
![]() | Overcurrent protection of the 20 mA inputs The current inputs are protected against damage due to overcurrent by an internal electronic overcurrent detection with self-resetting current path separation. The overcurrent is caused by an occasionally excessive sensor voltage. Depending on the duration and level of the applied voltage, currents > 200 mA can also occur for a short time (tripping time: µs range) until the current path disconnection becomes effective. Approx. 1 second after overcurrent detection and the resulting current path separation, the current path is closed again. If the excessive sensor voltage is still present, an overcurrent is detected again and the current path is opened. This process is repeated as long as the excessive voltage is present (auto-retry). To ensure that the current path separation is not overloaded, the dielectric strength in the current measuring range must be observed (see Technical data). Overcurrent is indicated in the process image as "Overrange". After it occurs, the error condition must be eliminated immediately. |
EL3072 - Connection
Terminal point | Description | Internally connected | Max. current carrying capacity *) | |
---|---|---|---|---|
Name | No. | |||
Ch 1 U+ | 1 | Channel 1, voltage measurement, positive input | - | not applicable (voltage input) |
Ch 2 U+ | 2 | Channel 2, voltage measurement, positive input | - | not applicable (voltage input) |
+24 V | 3 | +24 V | 4, 5, 6, 7, 8; positive power contact | 1 A |
+24 V | 4 | +24 V | 3, 5, 6, 7, 8; positive power contact | 1 A |
+24 V | 5 | +24 V | 3, 4, 6, 7, 8; positive power contact | 1 A |
+24 V | 6 | +24 V | 3, 4, 5, 7, 8; positive power contact | 1 A |
+24 V | 7 | +24 V | 3, 4, 5, 6, 8; positive power contact | 1 A |
+24 V | 8 | +24 V | 3, 4, 5, 6, 7; positive power contact | 1 A |
GND | 9 | Signal ground, channel 1 | negative power contact ( please note current carrying capacity) | 100 mA |
GND | 10 | Signal ground, channel 2 | negative power contact ( please note current carrying capacity) | 100 mA |
0 V | 11 | 0 V | 12, 15, 16; positive power contact | 1 A |
0 V | 12 | 0 V | 11, 15, 16; negative power contact | 1 A |
Input Ch1 | 13 | Channel 1, current measurement, input | - | 50 mA (see note "Overcurrent protection of the 20 mA inputs") |
Input Ch2 | 14 | Channel 2, current measurement, input | - | 50 mA (see note "Overcurrent protection of the 20 mA inputs") |
0 V | 15 | 0 V | 11, 12, 16; positive power contact | 1 A |
0 V | 16 | 0 V | 11, 12, 15; positive power contact | 1 A |
*) Constant current; short-time higher currents are to be avoided and can cause thermal overload (damage)