Scan Motor Cogging
When moving the motor, position-dependent torque fluctuations occur due to the cogging torques between the magnets. This can be compensated by determining appropriate cogging coefficients in the control. These coefficients are determined and stored (0x8010:61) by the "Scan Motor Cogging" function. It is a good idea to add the measured cogging coefficients to the start-up list after a successful scan.
Executing the scan
| |
The motor shaft moves during the scan procedure Injuries and damage to property are possible.
|
Requirements:
- Stable operation in the CSP operation mode. See chapter Selecting the operation mode.
- An encoder is connected and configured.
- The encoder has at least 256 increments per revolution.
- 1. Remove any load from the motor shaft.
- 2. Write the command 0x8009 into the register 0xFB00:01 "Request".
- The scan runs.
- The value of register 0xFB00:02 indicates the progress of the scan.
The values 100dec ... 199dec correspond to 0 ... 99 %. - 3. Wait until register 0xFB00:02 "Status" has one of the following values: 0, 1, 2, 3.
- Value 0: the scan has been successfully completed.
- Value 3: error. See chapter Error diagnosis.
- 4. Check Diag History: the error 0x8420 means that the controller is insufficiently optimized.
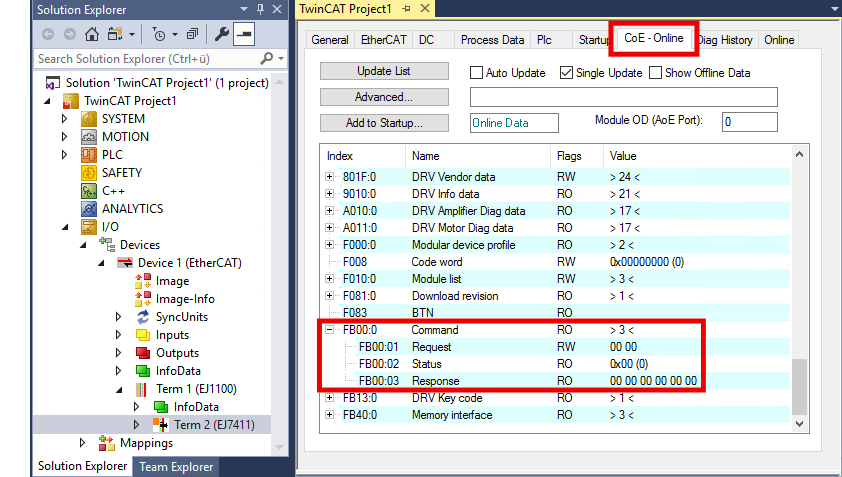
You can enable cogging compensation in CoE parameter 0x8010:05 "Enable cogging torque compensation".