Activating the modulo function
Valid parameterization of the modulo function necessitates the setting of IDNs in the AX5000 as well as corresponding parameterization of the NC or CNC. It is recommended to commission the modulo function with the help of the TcDriveManager, since this also sets the NC or CNC parameterization correctly. The procedure when using the TcDriveManager is described below.
The following IDNs are used for the parameterization of the modulo function:
S-0-0076 - "Position data scaling type"
The modulo function is activated with the bit "Processing format" in IDN S-0-0076 "Position data scaling type".

S-0-0103 - "Modulo Value"
The maximum calculated value for an application period is entered in IDN S-0-0103 “Modulo Value”. The unit is "inc", and 2x inc (where x = [20 to 30], see S-0-0079) correspond to one motor revolution. For the conversion please take into account the gear ratio of any gear unit installed after the motor. Accordingly, the maximum modulo position is S-0-0103 - 1 inc. Please note that S-0-0103 must be > S-0-0079.

In this example a multi-turn absolute value feedback system with 4096 turns and a gear unit with a gear ratio of 1:5 is used. 5 motor revolutions correspond to 1 application revolution. In this case the maximum modulo position is 5 x 220 - 1 inc, for S-0-0103 = 5 x 220.
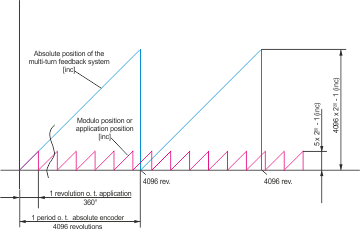
P-0-0276 – „Modulo calculation control“

This IDN can be used to select whether the offset required for the modulo calculation is to be stored cyclically in the drive, and in a fail-safe manner.
„0: Modulo data storage enabled“:
This setting requires a multi-turn encoder, otherwise the necessary memory operations cannot be performed fast enough. Thanks to the fail-safe storage of data, the modulo position can be reconstructed unambiguously after the drive was switched off and back on again, provided the encoder position was not changed by more than ¼ of the absolute range during the off state.
„1: Modulo data storage disabled“:
With this setting, no data are stored in the drive. It enables activation of the modulo calculation even for feedback systems that only provide a single-turn position. However, after the drive is switched off and on again, the modulo position cannot be reconstructed unambiguously, so that homing of the axis is necessary.
The further procedure is described in the section Configuration