Lebensdaueranalyse und Schädigungsrechnung
Motivation
Wie lange hält eine strukturelle Komponente, wie z. B. ein Turm einer Windkraftanlage, Brückenträger, Lastenkräne oder auch Maschinenkomponenten, die zyklischen Lasten ausgesetzt sind?
Die Antwort auf diese Fragen liefern rechnerische Lebensdaueranalysen. Sie verwenden Betriebslasten, Geometrie- und Materialdaten, um die Ermüdungsfestigkeit einer Konstruktion zu ermitteln. Ist das Bauteil oder die Konstruktion in Betrieb, kann mit einem kontinuierlichen Monitoring der realen Betriebslasten eine Abschätzung der Restlebensdauer realisiert werden.
Vor allem der Leichtbau hat den ressourcensparenden Einsatz von Rohstoffen und Energie bei Produktion und Betrieb zum Ziel. Durch leichtere Konstruktionen lassen sich nicht nur Kosten reduzieren, sondern auch neuartige Produkte mit komplexeren Geometrien realisieren. Diese Zielstellungen sind natürlich nicht nur auf den Bereich Leichtbau beschränkt, sondern erstrecken sich mehr und mehr über alle Bereiche mechanischer Konstruktionen. Vormals überdimensionierte Bauteile werden den voraussichtlich im Betrieb auftretenden Lasten angepasst. Entsprechend reduzieren sich auch die Sicherheitsmargen gegenüber Belastungen – die Bauteile sind also nicht mehr als dauerfest konstruiert. Eine betriebsfeste Konstruktion hingegen versucht, ein Bauteil so auszulegen, dass es für den definierten Einsatzzweck und bei definiertem Belastungsprofil eine gewünschte Lebensdauer ohne Versagen übersteht.
Wie im Bereich Schädigungsüberwachung im Abschnitt Beispiele aufgezeigt, ist die Software zur Lebensdaueranalyse mit TwinCAT 3 Condition Monitoring einfach realisierbar. Darüber hinaus bietet das Beckhoff-System eine hervorragende Plattform, die notwendigen Messgrößen aufzunehmen (bspw. ELM35xx), sie per EtherCAT auch über weite Strecken zu kommunizieren, sie auf einem verlässlichen IPC zu verarbeiten und schlussendlich an überlagerte Systeme weiterzureichen, zu speichern oder anzuzeigen.
Der folgende Abschnitt vermittelt Hintergrundwissen und dient der Einordnung des Themengebiets. Die Beschreibung der relevanten Funktionsbausteine sowie das aufbereitete Beispiel dienen exemplarisch der praktischen Umsetzung.
Hintergrund zur Lebensdaueranalyse
In diesem Abschnitt lernen Sie:
- Wie berechnet man die Ermüdungslebensdauer eines Bauteils und was ist eine Schadensakkumulation?
- Was sind Rainflow-Zyklenzählungen?
- Was ist eine Wöhler-Kurve?
- Wie werden Wöhler-Kurven ermittelt?
Grundlegende Konzepte
In den Anfängen der Ermüdungsrechnung vor ca. 200 Jahren, weit vor dem heutigen standardmäßigen Einsatz von Simulationstools und Messtechnik, wurden die ersten Fälle von Bauteilversagen näher untersucht: Bereits im Jahre 1837 hat Wilhelm Albert, Ingenieur aus Clausthal, erste Untersuchungen zur Ermüdung von Stahlketten durchgeführt. Seine Beobachtung, dass die Ketten nicht durch Überlastung, sondern auch bei häufigen, zyklischen Belastungen mit kleinerer Amplitude versagen, hat den Grundstein für die systematische Untersuchung der Ermüdungsfestigkeit gelegt. Um 1860 hat Albrecht Wöhler, ein deutscher Eisenbahn-Ingenieur, eine mathematische Formulierung der Dauerschwingfestigkeit von Metallen, der sog. Wöhler-Kurve, formuliert. Hierzu hat er Materialproben zyklischen Belastungen ausgesetzt und die Tests bis zur Zerstörung gefahren. Aus diesen Messungen konnte August Wöhler in einem Diagramm die mechanische Spannung über der erreichten Schwingspielzahl auftragen und eine Kennlinie des getesteten Materials ableiten.
Ergänzend zu diesen grundlegenden Beobachtungen wurde der Einfluss der Mittelspannung, d. h. einer konstanten mechanischen Vorspannung, auf die Ermüdungslebensdauer von Gerber und Goodman näher untersucht. Sie haben Berechnungsmethoden entwickelt, um den Mittelspannungseinfluss in den Berechnungen zu berücksichtigen.
Die Hypothese der linearen Schadenakkumulation wurde 1924 von A. Palmgren aufgestellt und von M.A. Miner im Jahr 1945 veröffentlicht. Sie besagt, dass bei einer Gesamtschädigung von D = 1 das betrachtete Bauteil versagt.
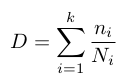
Hier beschreiben Ni die maximal Anzahl an Schwingzyklen bis zum Bauteilversagen und ni die bereits vom Bauteil erfahrene Anzahl von Schwingzyklen. Das Verhältnis ni/Ni wird als Teilschädigung bezeichnet und betrachtet nur die Schädigung, die durch eine feste Schwingbreite verursacht wird. Die Summe aller Teilschädigungen über alle auftretenden Schwingbreiten ist dann die Gesamtschädigung D. Der Index i läuft entsprechend über k Klassen, welche jeweils eine Schwingbreite definiert.
Zur Definition von Mittelspannung und Schwingbreite: Angenommen ein Material wird mit einer konstanten Kraft vorgespannt und dann zusätzlich mit einer harmonischen Schwingung mit Amplitude yp beaufschlagt. Die mechanische Spannung im Material setzt sich dann zusammen aus der Mittelspannung ym und einer harmonischen Schwingung mit Schwingbreite von 2*yp.
Im folgenden Beispiel wird ein Bauteil mit einer Schwingbreite von 200 MPa beansprucht. Die Wöhler-Kurve definiert zu dieser Beanspruchung eine Schwingspielzahl von 100.000 (1E5) Zyklen. Ein Zyklus „verbraucht“ somit 1/100.000 der Ermüdungslebensdauer. Die Wähler-Kurve ist doppelt-logarithmisch aufgetragen.
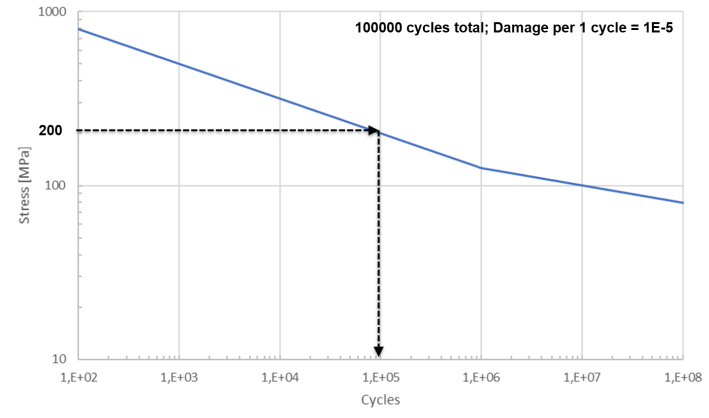
Belastungen an realen Bauteilen haben, im Gegensatz zu Werkstoffprüfungen, fast beliebige Signalverläufe. Es ist demnach notwendig, das zeitliche Beanspruchungssignal mit einem geeigneten Verfahren in Klassen zusammenzufassen, welche dann nach obigem Verfahren nach Miner gezählt werden können.
M. Matsuishi und Tatsuo Endo haben 1968 mit der Rainflow Zyklenzählung ein Verfahren vorgestellt, welches die Zeitsignale auf einer um 90° gedrehten Zeitachse darstellt. Die Ähnlichkeit mit einem Pagodendach, über das Regen an den Umkehrpunkten abläuft, gab dem Verfahren den Namen. Es werden zunächst Halbzyklen, z. B. in Zugrichtung, gezählt und mit passenden Halbzyklen in gegengesetzter Beanspruchungsrichtung, z. B. Druckrichtung, zu geschlossenen Zyklen kombiniert. Dieses Verfahren ist in der ASTM E 1049-85 (Standard Practices for Cycle Counting in Fatigue Analysis) genormt und weit verbreitet.
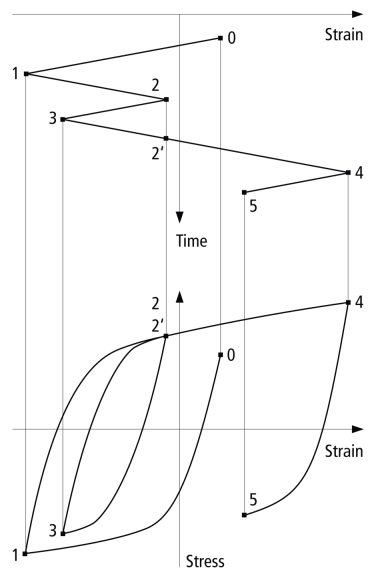
Ermittlung und Bedeutung von Wöhler-Kurven
Zur Ermittlung der Wöhler-Kurve werden Materialproben mit einer definierten Probengeometrie (häufig eine Rundprobe mit 10 mm Durchmesser) in eine Prüfmaschine eingespannt. Diese leitet zyklisch Kräfte in die Probe ein, meist symmetrisch um den Nullwert (Mittelspannungsfrei) mit einer konstanten Maximalkraft schwingend. Es sind aber auch Abwandlungen im Druck- oder Zugschwellbereich möglich, um Materialparameter bei anderen Mittelspannungswerten zu ermitteln. Der Versuch wird bei einer konstanten Maximalamplitude bis zur Zerstörung (= Ermüdungsbruch) oder bis zum technischen Anriss gefahren und die erreichte Zyklenzahl für diese Laststufe im Diagramm eingetragen.
Ein Material reagiert bei einer äußeren Belastung, also der eingeleiteten Kraft F, aufgrund seiner Geometrie mit Querschnitt A mit einer Beanspruchung, die als mechanische Spannung definiert ist. Bei bekanntem (initialem) Probendurchmesser und bekannter einwirkender Kraft kann somit die resultierende Bauteilbeanspruchung als Quotient aus F und A ermittelt werden. Sie wird üblicherweise in der Einheit Megapascal (MPa) angegeben.
Entsprechend wird also ein mechanischer Spannungswert in der Wöhler-Kurve über die erreichbare Zyklenzahl aufgetragen. Um die natürliche Streuung der Tests zu ermitteln, werden pro Laststufe stets mehrere Wiederholungen mit gleichwertigem Material und gleicher Probengeometrie durchgeführt.
Die Durchführung von Schwingfestigkeitsversuchen ist u. a. in der DIN 50100 normiert. Auch die ASTM hat mit der ASTM E466-15 ein Standardverfahren für die Ermüdungsversuche mit konstanter Amplitude veröffentlicht.
Exemplarisch ist im Folgenden eine Wöhler-Kurve für Aluminium in einfach logarithmischer Darstellung abgebildet.
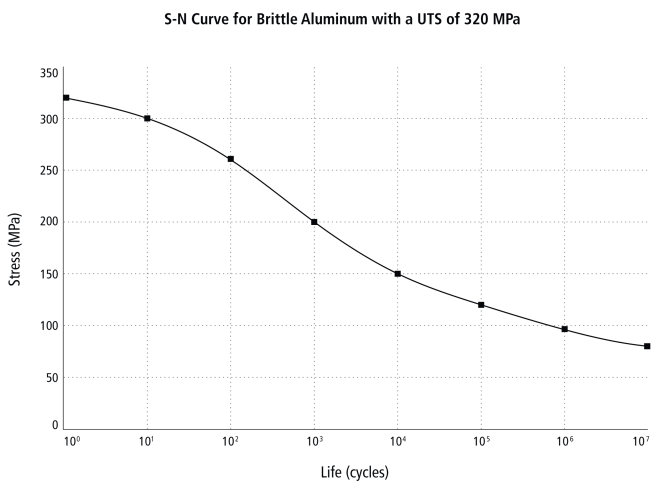
Die Wöhler-Kurve lässt sich in drei Bereiche einteilen:
Kurzzeitfestigkeit (Low Cycle Fatigue, LCF): Bereich hoher Beanspruchungsamplituden
(N = 1 … ca. 10^4 Zyklen). In untenstehender Grafik Gelb dargestellt.
- In diesem Bereich findet eine starke Beanspruchung statt, bei der sich das Material plastisch stark verformt. Für diesen Bereich bilden dehnungsgesteuerte Materialversuche das Verhalten deutlich besser ab; es werden sog. Dehnungs-Wöhlerlinien verwendet.
- Nur wenige Bauteile werden in der Praxis im Bereich der Kurzzeitfestigkeit ausgelegt.
Zeitfestigkeit/Betriebsfestigkeit (High Cycle Fatigue, HCF): Bereich konstanter Steigung wenn die Wöhler-Kurve in x- und y-Achse logarithmisch aufgetragen wird ([N = ca. 10^4 … 10^6). In untenstehender Grafik Grün dargestellt.
- Klassischer Bereich der betriebsfesten Bauteilauslegung.
- In Industrie und Forschung weit verbreitet und in vielen Anwendungen eingesetzt.
- Viele Materialparameter in der Literatur verfügbar.
Dauerfestigkeit (Very High Cycle Fatigue, VHCF): Bereich ohne signifikanten Abfall der Wöhler-Kurve ab einer bestimmten Amplitude [N > ca. 10^6]. In untenstehender Grafik Blau dargestellt.
- Theoretische Beanspruchungsgrenze, unterhalb der keine Ermüdung beobachtet wird (durch Korrosion und erhöhte Temperaturen treten dennoch Ermüdungserscheinungen auf).
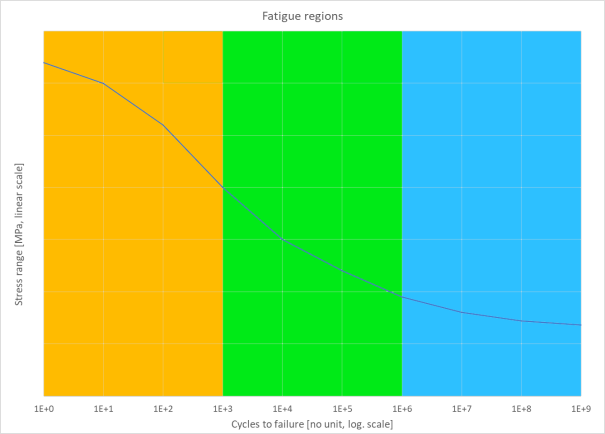
Eine gebräuchliche Approximation einer Wöhler-Kurve in Anlehnung an obige drei Bereiche ist im Folgenden dargestellt. Dazu wird die Wöhler-Kurve in doppelt-logarithmische Darstellung umgesetzt und diese dann in drei lineare Abschnitte unterteilt. Diese Darstellung wird häufig genutzt und kann aus wenigen Materialparametern erstellt werden.
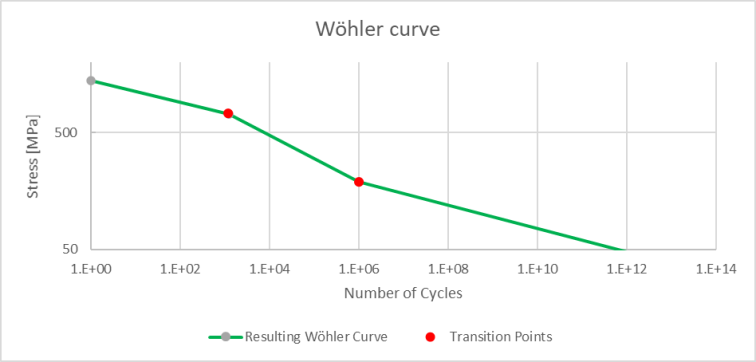
Übliche Werte für die Steigung k der Wöhler-Kurve sind:
- Geschweißte Bauteile: k = 3
- Elektronische Komponenten: k = 4
- Bauteile ohne Spannungskonzentrationen: k = ~10
Je flacher die Steigung einer Wöhler-Kurve ist (hohe k Werte), desto unempfindlicher ist das Material aus Sicht des Ermüdungsverhaltens. Kleinere Schwingbreiten schädigen das Material also weniger stark, d.h. die ertragbare Schwingspielzahl zu einer bestimmten Schwingbreite ist größer als bei einem Material mit einem steileren Verlauf der Wöhler-Kurve.
Ein steiler Verlauf eignet sich für Bauteile, die auch bei kleineren Schwingbreiten noch ermüdungsempfindlich sind: Geschweißte Konstruktionen, Bauteile mit Spannungskonzentrationen oder auch elektronische Bauteile. Im folgenden Beispiel sind bei gleichem Spannungsschnittpunkt zwei Wöhler-Kurven mit Steigungen k=8 und k=6 aufgetragen. Die ertragbaren Schwingspielzahlen unterscheiden sich deutlich (46.500 zu 1,68*10^6).
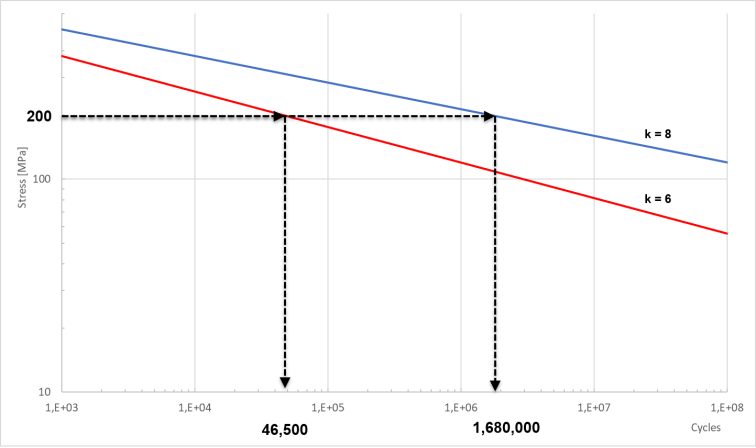
Praktische Hinweise zur Deutung der Wöhler-Kurve
Arbeitet man im Themenfeld der Materialermüdung, sollte man jederzeit bedenken, dass die Berechnungen stets eine statistische Natur besitzen. Häufig werden Wöhler-Kurven über 50 % Überlebenswahrscheinlichkeit definiert. Dies bedeutet, dass beim angegebenen Punkt einer p50-Wöhler-Kurve bereits 50 % der getesteten Prüflinge zerstört wurden. Wenn eine höhere Überlebenswahrscheinlichkeit gefordert ist, sind aus den Materialversuchen Kurven mit entsprechender Überlebenswahrscheinlichkeit abzuleiten.
Nicht nur die Ermittlung der Materialparameter abstrahiert die streuenden Messergebnisse in einige wenige einfache Kurvenparameter, sondern es unterscheiden sich auch Materialproben deutlich von realen Bauteilen. Insbesondere die reduzierte Lebensdauer von Bauteilen durch Spannungskonzentrationen spielt eine wichtige Rolle.
Geometrie:
- Probenkörper weisen keine scharfen Kanten auf und sind geschliffen (keine Kerben, Lunker etc.)
- Scharfe Kanten und Ausstanzungen im Bauteil führen lokalen Spannungsüberhöhungen und Rissbildung
Materialqualität:
- Probenkörper besitzen eine hohe Materialqualität
- Reale Materialien in der Produktion weisen oft schwankende Qualität auf (Lunker, Variation der Herstellungsprozesse, Oxidation, Elektrokorrosion, Beschädigungen durch Verformung etc.)
Bearbeitungsprozesse:
- Schweißverbindungen in realen Bauteilen
- Durch Bearbeitungsprozesse entstehen scharfe Kanten, Ausfräsungen und Kerben. Eine Nachbearbeitung der Oberfläche oder eine Konstruktionsänderung kann diese Spannungskonzentrationen reduzieren.
Spannungskonzentrationen führen zu deutlich früherem Materialversagen. Im Folgenden ist exemplarisch der Einfluss einer Kerbwirkung (stress concentration factor) auf die Wöhler-Kurve dargestellt, der zu einer Absenkung der Kurve führt und die ertragbare Schwingspielzahl um Faktor 6 reduziert.
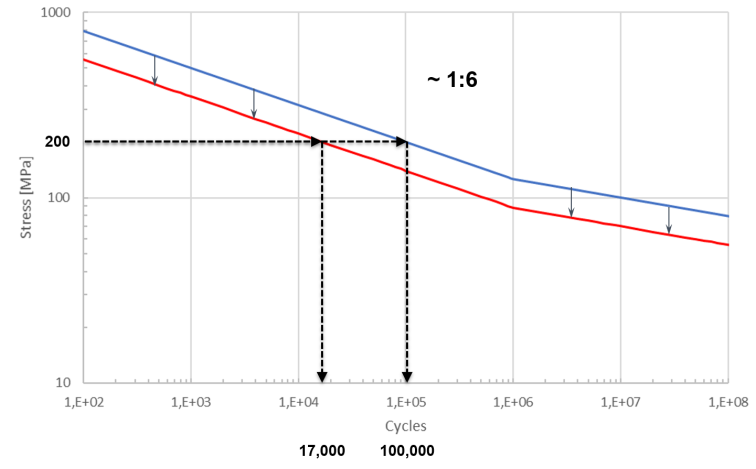
Wird für ein Bauteil/eine Komponente eine präzise Aussage zur Schwingfestigkeit gefordert, besteht die Möglichkeit – je nach Bauteilkosten, Größe und Verfügbarkeit von Bauteil und Prüfequipment – eine sog. „Bauteil-Wöhler-Kurve“ zu ermitteln. Nachteilig ist hierbei, dass neben den hohen Kosten für das Testen die Aussagekraft zwar für das aktuelle Bauteil hoch ist, dies aber eingeschränkt nutzbar sind, wenn sich die Bauteilkonstruktion ändert.
Überwachungsstrategie: Ermüdungs- bzw. Lebensdaueranalyse
Die Ermittlung der Lastdaten erfolgt direkt am Prüfling, z. B. durch Messung mit Dehnungs-, Kraft- oder Drucksensoren. Nach der Zyklenzählung mit dem Rainflow-Algorithmus stehen damit aus Sicht der Belastungen alle notwendigen Informationen zur Verfügung. Hinsichtlich der Ermüdungsbewertung nach Miner sind nun die Materialeigenschaften (Wöhler-Kurve) hinzuzuziehen. Die Festlegung der Ermüdungseigenschaften des verwendeten Materials sind häufig schwierig, oft stehen nur wenige oder keine Materialkennwerte zur Verfügung oder müssen abgeschätzt werden.
Praktisch helfen folgende Überlegungen:
- Beschränkung auf einen relativen Vergleich von baugleichen Komponenten
- Heranziehen von Literaturdaten und entsprechende Umrechnung in eine approximierte Wöhler-Kurve
Relativer Vergleich von Komponenten
Insbesondere für relative Vergleiche zwischen baugleichen Komponenten, z. B. Maschinenteilen im Serienmaschinenbau, eignen sich generische Wöhler-Kurven mit definierten Steigungen. Die absolute Schadenssumme ist hier nicht aussagekräftig, jedoch können Aussagen wie „Maschinenteil B ist um 40 % stärker geschädigt als Maschinenteil A“ abgeleitet werden und damit Wartungsentscheidungen unterstützt werden.
Nutzung von Literaturquellen
Für die Ermittlung von absoluten Schadenswerten werden üblicherweise Wöhler-Kurven aus realen Materialproben in Prüfmaschinen ermittelt. Es stehen aber mit dem Eurocode 3 und der FKM-Richtlinie ebenfalls Quellen für Materialparameter von Stahl zur Verfügung, aus denen sich Wöhler-Kurven berechnen lassen.
![]() | Im Folgenden werden immer Schwingbreiten angegeben und nicht wie in einigen Quellen auch üblich Peak-Amplituden. Die Schwingbreite ist doppelt so groß wie die Peak-Amplitude. |
Die FKM Richtlinie (Forschungskuratorium Maschinenbau, Verbund im VDMA) gibt konservative Materialkennwerte für verschiedene Werkstoffsorten und -zustände an. Ein Beispiel auf der FKM Richtlinie (weitere siehe Abschnitt Anlagen).
Sorte | UTS [Schwing-breite, MPa] | Schwingbreite bei Dauerfestigkeit [MPa] | k | NC | SRI [MPa] |
---|---|---|---|---|---|
S185 | 620 | 280 | 5 | 1E+06 | 4438 |
Übersetzt in die Materialparameter für die Funktion F_CM_CalculateWoehlerCurve ergeben sich:
fSRI : LREAL := 4438;
fUTS : LREAL := 620;
bUseUTSCorrection : BOOL := TRUE;
fK1 : LREAL := 5;
fK2 : LREAL := 0;
nNC1 : ULINT := 18790;
nNC2 : ULINT := 1E+06;
fSRI
und fUTS
können also direkt übernommen werden. Die Steigung beträgt wie angegeben 5 und bezieht sich auf den Bereich zwischen der Transition von der UTS Korrektur bis zur Dauerfestigkeitsgrenze. Die Dauerfestigkeitsgrenze ist bei NC definiert, welche als nNC2
eingetragen wird. Die Steigung im Dauerfestigkeitsbereich ist natürlich fK2 = 0
. Nur als Eingabe in die Funktion F_CM_CalculateWoehlerCurve muss zusätzlich der Transitionspunkt von der UTS Korrektur zum Bereich mit Steigung 5 über die Gleichung
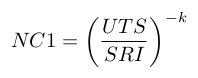
berechnet werden.
Der Eurocode 3 (BS EN1993-1-9: 2005) definiert für Stahl in unterschiedlichen Konstruktionsdetails, insbesondere gerollte/extrudierte Produkte, Schweiß- und Schraubverbindungen und unterschiedliche Geometrien, wie T-Träger, unterschiedliche Wöhler-Kurven. Alle Wöhler-Kurven haben diese drei Abschnittsdefinitionen gemeinsam:
- N ≤ 5*106 mit k = 3
- 5*106 ≤ N ≤ 108 mit k = 5
- N ≥ 108 mit k=0 (dauerfest)
Ein Beispiel aus dem Eurocode 3 (weitere siehe Abschnitt Anlagen).
Konstruktionsdetail | Δσc [Schwing-breite, MPa] | k1 | k2 | N bei Δσc | NC1 | ND (Dauer-festigkeits-grenze) | SRI bei | ΔσNC1 bei NC1 [MPa] | Δσl bei ND [MPa] |
---|---|---|---|---|---|---|---|---|---|
160 | 160 | 3 | 5 | 2E+06 | 5E+06 | 1E+08 | 20159 | 118 | 65 |
Als Konstruktionsdetail 160 ist im Eurocode ein gerolltes oder extrudiertes Produkt definiert, ausgeführt als Platte, Hohlzylinder oder ähnliche Formen.
Übersetzt in die Materialparameter aus dem bereitgestellten Beispielcode ergeben sich:
fSRI : LREAL := 2580;
fUTS : LREAL := 20159;
bUseUTSCorrection : BOOL := TRUE;
fK1 : LREAL := 5;
fK2 : LREAL := 0;
nNC1 : ULINT := 5E+06;
nNC2 : ULINT := 1E+08;
Die Parametrierung wurde hier so umgerechnet, dass sich die Forderung nach drei definierten Zonen mit Steigung 3, 5, und 0 bei Verwendung der Funktion F_CM_CalculateWoehlerCurve ergibt. Die UTS-Korrektur wird hier so genutzt, dass sich im ersten Abschnitt eine Steigung von 3 ergibt. Aus diesem Grund ist fUTS
auch größer als fSRI
. Der Wert für fSRI
ergibt sich mit k2 = 5 zu

fUTS
wird dann zu SRI aus dem Eurocode gesetzt. Damit ergibt sich im ersten Abschnitt eine Steigung von 3. Durch Setzen von fK1
= k2 und fK2
= 0 ergeben sich die weiteren zwei Sektionen.
Zusammenfassung
Die Eingangsgrößen einer Lebensdaueranalyse lassen sich in drei Gruppen einteilen:
- Materialeigenschaften beschreiben die Ermüdungsfestigkeit des Werkstoffes, meist als Wöhler-Kurve, ergänzt um Oberflächenbeschaffenheit und -bearbeitung.
- Geometriefaktoren dienen zur Anpassung der Materialparameter an lokale Geometrieeigenschaften, die die Ermüdungslebensdauer beeinflussen (z. B. Kerben oder scharfe Kanten).
- Lasten sind auf das Bauteil einwirkende Signale, die zu einer Beanspruchung führen. Sie werden häufig mit Dehnungsmessstreifen, Kraft- oder Drehmomentaufnehmern erfasst.
Im Analyseteil befinden sich je nach Komplexitätsgrad folgende Komponenten:
- Korrekturen der Materialparameter und Verwendung von Geometriefaktoren
- Zyklenzählung zur Überführung der Zeitsignale in Klassen (Mittelspannung, Schwingbreite) für die Verarbeitung in der Schadenakkumulation
- Mittelspannungskorrekturen, um die Reduzierung der Ermüdungslebensdauer durch Mittelspannungseffekte zu berücksichtigen
- Schadenakkumulation für die Summierung der einzelnen Schädigungsanteile aus der Zyklenmatrix, Materialparametern und Korrekturfaktoren
Als Ergebnis stehen u. a. die Schadenssumme für weitergehende Vergleiche, beispielsweise zu baugleichen Komponenten, oder als Grundlage für Warnungs-/Alarmmeldungen zur Verfügung. Der monoton steigende Verlauf der Schadenssumme eignet sich gut für eine Extrapolation zu definierten Grenzen, um kritisch beanspruchte Komponenten zu identifizieren und Wartungseinsätze besser planen zu können.
Dieses Verfahren eignet sich nicht nur für die klassische Ermüdungsanalyse zur Berechnung einer absoluten Schädigungszahl, sondern auch für relative Vergleiche der Schädigungsintensität: Kraft- oder Drucksignale, Temperaturzyklen oder andere schwingende Signalformen können verwendet werden, um statische Verfahren (Extremwerte, Crest-Faktor, Kurtosis usw.) um eine aussagekräftige Information zu erweitern.
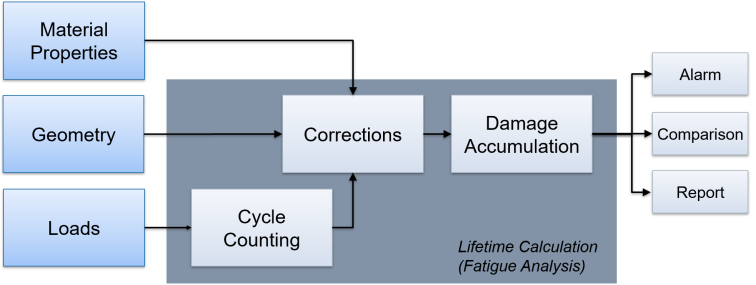
Die drei in obiger Grafik zentralen Elemente „Cycle Counting“, „Corrections“ und „Damage Accumulation“ werden in der Function TwinCAT 3 Condition Monitoring umgesetzt mit FB_CMA_RainflowCounting, FB_CMA_MeanStressCorrection und FB_CMA_MinersRule.
Anlage: Eurocode und FKM Richtline
Eurocode 3 (EN 1993-1-9:2005 - Design of steel structures)
Konstruktionsdetail | Δσc [Schwing-breite, MPa] | k1 | k2 | N bei Δσc | NC1 | ND (Dauer-festigkeits-grenze) | SRI bei | ΔσNC1 bei NC1 [MPa] | Δσl bei ND [MPa] |
---|---|---|---|---|---|---|---|---|---|
160 | 160 | 3 | 5 | 2E+06 | 5E+06 | 1E+08 | 20159 | 118 | 65 |
140 | 140 | 3 | 5 | 2E+06 | 5E+06 | 1E+08 | 17639 | 103 | 57 |
125 | 125 | 3 | 5 | 2E+06 | 5E+06 | 1E+08 | 15749 | 92 | 51 |
112 | 112 | 3 | 5 | 2E+06 | 5E+06 | 1E+08 | 14111 | 83 | 45 |
100 | 100 | 3 | 5 | 2E+06 | 5E+06 | 1E+08 | 12599 | 74 | 40 |
90 | 90 | 3 | 5 | 2E+06 | 5E+06 | 1E+08 | 11339 | 66 | 36 |
80 | 80 | 3 | 5 | 2E+06 | 5E+06 | 1E+08 | 10079 | 59 | 32 |
71 | 71 | 3 | 5 | 2E+06 | 5E+06 | 1E+08 | 8945 | 52 | 29 |
63 | 63 | 3 | 5 | 2E+06 | 5E+06 | 1E+08 | 7938 | 46 | 25 |
56 | 56 | 3 | 5 | 2E+06 | 5E+06 | 1E+08 | 7056 | 41 | 23 |
50 | 50 | 3 | 5 | 2E+06 | 5E+06 | 1E+08 | 6300 | 37 | 20 |
45 | 45 | 3 | 5 | 2E+06 | 5E+06 | 1E+08 | 5670 | 33 | 18 |
40 | 40 | 3 | 5 | 2E+06 | 5E+06 | 1E+08 | 5040 | 29 | 16 |
36 | 36 | 3 | 5 | 2E+06 | 5E+06 | 1E+08 | 4536 | 27 | 15 |
FKM Richtlinie
Die FKM Richtlinie gibt konservative Materialkennwerte für verschiedene Werkstoffsorten und -zustände an. Die folgenden Werte für unlegierten Baustahl, unlegierten Feinkornbaustahl, Vergütungsstahl und Gusseisen gelten für eine Überlebenswahrscheinlichkeit von 97,5 %.
Unlegierter Baustahl
Sorte | UTS [Schwing-breite, MPa] | Schwingbreite bei Dauerfestigkeit [MPa] | k | NC | SRI [MPa] |
---|---|---|---|---|---|
S185 | 620 | 280 | 5 | 1E+06 | 4438 |
S235 | 720 | 320 | 5 | 1E+06 | 5072 |
S275 | 860 | 390 | 5 | 1E+06 | 6181 |
S355 | 1020 | 460 | 5 | 1E+06 | 7291 |
S450 | 1100 | 500 | 5 | 1E+06 | 7924 |
E295 | 980 | 440 | 5 | 1E+06 | 6974 |
E335 | 1180 | 530 | 5 | 1E+06 | 8400 |
E360 | 1380 | 620 | 5 | 1E+06 | 9826 |
Vergütungsstahl, vergüteter Zustand
Sorte | UTS [Schwing-breite, MPa] | Schwingbreite bei Dauerfestigkeit [MPa] | k | NC | SRI [MPa] |
---|---|---|---|---|---|
C22 E/R | 1000 | 450 | 5 | 1E+06 | 7132 |
C35 E/R/- | 1260 | 570 | 5 | 1E+06 | 9034 |
C40 E/R/- | 1300 | 590 | 5 | 1E+06 | 9351 |
C45 E/R/- | 1400 | 630 | 5 | 1E+06 | 9985 |
C50 E/R/- | 1500 | 680 | 5 | 1E+06 | 10777 |
C55 E/R/- | 1600 | 720 | 5 | 1E+06 | 11411 |
C60 E/R/- | 1700 | 770 | 5 | 1E+06 | 12204 |
28Mn6 | 1600 | 720 | 5 | 1E+06 | 11411 |
38Cr2 | 1600 | 720 | 5 | 1E+06 | 11411 |
46Cr2 | 1800 | 810 | 5 | 1E+06 | 12838 |
34Cr4 | 1800 | 810 | 5 | 1E+06 | 12838 |
37Cr4 | 1900 | 860 | 5 | 1E+06 | 13630 |
41Cr4 | 2000 | 900 | 5 | 1E+06 | 14264 |
25CrMo4 | 1800 | 810 | 5 | 1E+06 | 12838 |
34CrMo4 | 200 | 450 | 5 | 1E+06 | 7132 |
42CrMo4 | 2200 | 990 | 5 | 1E+06 | 15690 |
50CrMo4 | 2200 | 990 | 5 | 1E+06 | 15690 |
34CrNiMo8 | 2400 | 1080 | 5 | 1E+06 | 17117 |
30CrNiMo8 | 2500 | 1130 | 5 | 1E+06 | 17909 |
35NiCr6 | 1760 | 790 | 5 | 1E+06 | 12521 |
36NiCrMo16 | 2500 | 1130 | 5 | 1E+06 | 17909 |
39NiCrMo3 | 1960 | 880 | 5 | 1E+06 | 13947 |
30NiCrMo16-6 | 2160 | 970 | 5 | 1E+06 | 15373 |
51CrV4 | 2200 | 990 | 5 | 1E+06 | 15690 |