Wälzlagerüberwachung
Motivation
Wälzlager zählen zu den häufigsten und am stärksten belasteten Maschinenelementen. In vielen Fällen können sie eine für den Betrieb einer Anlage kritische Bedeutung haben. Während bei großen Lagern schon die Ausfallzeiten für eine Ersatzbeschaffung hohe Kosten verursachen können, können auch Ausfälle von kleinen Lagern Kosten verursachen, welche weit über den Kosten des Ersatzteils liegen.
Schadensursachen
Die möglichen Ursachen für Ausfälle von Wälzlagern sind vielfältig:
- Die "natürliche" Ursache für Ausfälle von Wälzlagern ist Materialermüdung durch die hohen Spannungen, die beim Betrieb an den Kontaktflächen der Wälzkörper auftreten. Diese führen nach einer gewissen Zeit zu Rissen im Material und zu Ausbrüchen an der Lauffläche. Es entstehen kleine Defekte, die zunächst sehr langsam wachsen und sich gegen Ende der Lebensdauer mit zunehmender Geschwindigkeit vergrößern. Die Mechanismen der Materialermüdung sind theoretisch gut verstanden und lassen sich statistisch beschreiben; sie sind Bestandteil der normalen Abnutzung. Bei der Auslegung eines normalen Lagers werden die Dimensionen so gewählt, dass die Wahrscheinlichkeit eines gravierenden Schadens innerhalb der Lebensdauer der Maschine gering ist. Von korrekt dimensionierten und gewarteten Lagern kann also unter normalen Umständen eine sehr lange Lebensdauer erwartet werden. Die tatsächlich erreichte Lebensdauer ist oft wesentlich geringer, jedoch nicht genau vorhersagbar und kann beträchtlich schwanken, was an den folgenden Ursachen liegt.
- Die Beanspruchung von Wälzkörpern und Laufflächen wird erheblich vergrößert durch fehlerhafte Schmierung, da das Schmiermittel einen Teil der Spannung verteilt und auch ein Heißlaufen des Lagers verhindert.
- Eine weitere Ursache von Schäden sind Verschmutzungen, beispielsweise aufgrund fehlerhafter Dichtungen, oder durch Metallspäne. Auch das Eindringen von Wasser kann zu einem Versagen der Schmierung führen, da schon geringe Mengen Wasser Schmiermittel untauglich machen.
- Eine nicht unwichtige Fehlerquelle sind weiterhin Ungenauigkeiten bei der Ausrichtung oder schädigende Belastungen beim Einbau.
- Zu hohe Belastungen führen zu plastischen Verformungen der Lauffläche (Brinelling). Ähnliches kann auch durch Vibrationen bei Stillstand des Lagers entstehen, die nicht durch einen Schmierfilm gemildert werden (False Brinelling).
- In elektrischen Maschinen kann Stromfluss die Laufflächen zerstören.
- Korrosion kann die initiale Schädigung der Oberfläche bewirken.
Allen diesen Ursachen ist gemeinsam, dass Beschädigungen der Laufflächen des Wälzlagers schon früh im Schadensverlauf detektierbar sind. Aus der Tatsache, dass Ausfälle bei Lagern in der großen Mehrzahl der Fälle nicht durch Materialermüdung verursacht werden, folgt, dass eine frühe Erkennung von Schäden und die Analyse und Rückverfolgung auf die primären Ursachen (Root Cause Failure Analysis (RCFA)) es – neben der Reduktion von Ausfallkosten – mittelfristig möglich macht, viele Schäden vorbeugend zu vermeiden und die praktische Lebensdauer von Lagern erheblich zu erhöhen.
Schadensfolgen
Nach der ersten Beschädigung der Laufflächen kommt es infolge von anwachsenden Spannungen zu einer Ausbreitung von Defekten. Neben der Lauffläche können auch andere Komponenten, wie der Käfig der Wälzkörper betroffen sein. Vibrationen zeigen nicht unbedingt die ersten Stufen des Schadensprozesses an, da sie meist nicht die Ursache von Schäden darstellen, sondern ein Symptom. Jedoch führen alle Schadensverläufe früher oder später zu Defekten an den Kontaktstellen, die sich in zunehmenden Vibrationen äußern.
Überwachungsstrategien
Da eine direkte Erkennung der ersten Ursachen möglicherweise schwierig ist, liegt der Fokus auf einer Früherkennung der Folgeschäden in der Lauffläche des Lagers. Je früher diese bemerkt und untersucht werden, desto größer sind die Chancen, die Spuren der initialen Schäden zu finden und anhand dieser die Ursachen zu beheben – eine Strategie, die langfristig oft zu nachhaltigen Einsparungen führt. Weiterhin erleichtert eine Früherkennung eine Planung der Wartung, was vor allem für Anlagenbetreiber einen Vorteil darstellt. Eine zweite Strategie ist eine Identifikation der betroffenen Elemente durch Analyse der Schwingungssignale.
Zum Verständnis der folgenden Möglichkeiten zur Signalanalyse erfolgt zunächst ein kurzer phänomenologischer Einblick in die Entstehung von Vibrationen bei defekten Wälzlagern.
Schematischer Aufbau eines Wälzlagers im Querschnitt:
Die kritischen Teile eines Wälzlagers sind diejenigen Flächen, welche aufeinander laufen. Dies sind die Wälzkörperoberfläche, sowie die Lauffläche des Innenrings und die Lauffläche des Außenrings. Bei lokal beschädigter Lauffläche kommt es beim Überrollen der Beschädigung zu einem Stoßimpuls, welcher über einen Beschleunigungssensor aufgenommen werden kann. Je größer die Beschädigung, desto kräftiger fällt der Stoßimpuls aus.
Bewertung der Vibration im Zeitbereich
Eine einfache Methode zur Bewertung des Zustands eines Wälzlagers ist die Bewertung des Vibrationssignals hinsichtlich seiner Impulshaltigkeit. Gängige Verfahren dazu sind die Berechnung des Crestfaktors sowie des Kurtosiswerts.
Der Crestfaktor
Der Crestfaktor ist definiert als das Verhältnis vom Betrag der maximalen Amplitude zum Effektivwert des Signals. Er wird angegeben in Dezibel und ist eine Zahl größer gleich Null. Der Crestfaktor bestimmt somit das Verhältnis zwischen Maximalamplitude und der effektiven mittleren gemessenen Schwingungsamplitude. Stoßimpulse aus einem beginnenden Schaden führen zu einer Zunahme des Crestfaktors. Folgende Grafik zeigt die Erhöhung des Crestfaktors mit steigender Impulshaltigkeit der Signale.
Die unterste Kurve zeigt den typischen starken Anstieg des Crestfaktors beim Auftreten von spitzen Stoßimpulsen. Eine Zunahme des Crestfaktors zeigt normalerweise an, dass sehr wahrscheinlich eine Beschädigung vorliegt. Dies macht diese Größe zu einem geeigneten Werkzeug für die Früherkennung von Schäden und für Trendanalysen.
Signale aus einem Wälzlager können wie folgt interpretiert werden.
Die obige Abbildung zeigt zwei Schwingungssignale aus unterschiedlich abgenutzten Lagern, jeweils mit dem zugehörigem Crestfaktor. Die aus dem Schaden resultierenden Spitzen sind im unteren Signalverlauf deutlich zu erkennen. Während das unbeschädigte Lager einen Crestfaktor von 4,8 dB aufweist, beträgt dieser beim beschädigten Teil 11,4 dB, und zeigt so das Vorliegen einer Beschädigung klar an.
Der Crestfaktor hat den Vorteil, dass er sehr effizient zu berechnen und leicht interpretierbar ist. Zudem lässt er sich sehr einfach in einem Diagramm über der Zeit darstellen. Für eine korrekte Anwendung ist es wichtig, auch die prinzipiellen Grenzen dieser Auswertung zu verstehen:
- Der Crestfaktor ist stark durch das Signalmaximum bestimmt und daher im statistischen Sinne keine robuste Größe.
- Der Crestfaktor steigt bei zunehmenden lokalen Schädigungen an. Die Spitzenwerte der Stoßimpulse werden aber ab einem bestimmten Schadensfortschritt nicht mehr signifikant ansteigen, jedoch nimmt die Anzahl der lokalen Schädigungen zu. Das führt dazu, dass die Signalmaxima nicht zunehmen, der Effektivwert des Signals jedoch ansteigt. Dadurch verringert sich der Crestfaktor bei stark beschädigten Lagern wieder.
Aus diesem Grund ist es ratsam bei Verwendung des Crestfaktors möglichst kontinuierlich zu messen und die Ergebnisse hinsichtlich des Trends auszuwerten.
Der Kurtosiswert
In manchen Fällen ist die begrenzte statistische Robustheit des Crestfaktors problematisch. Robuster, aber etwas rechenaufwändiger, ist der Kurtosiswert (auch Kurtosis, Wölbung, viertes zentrales Moment). Die Kurtosis gehört, wie Mittelwert und Varianz, zu den sogenannten Momentenkoeffizienten, mit denen sich Größen statistisch beschreiben lassen. Die Kurtosis beschreibt das Verhältnis zwischen den extremen (weitab vom Mittelwert liegenden) Werten einer Verteilung und der mittleren Schwankungsbreite. Da vereinzelte Ausreißer in einer Messreihe aber nicht bestimmend für das Ergebnis sind, ist die Kurtosis statistisch wesentlich robuster als der Crestfaktor.
Die praktische Benutzung der Kurtosis erfolgt weitgehend analog zum Crestfactor. Die Berechnung der Kurtosis (bzw. des Exzess) und weiterer gängiger statistischer Momentenkoeffizienten erfolgt in der TwinCAT 3 Condition Monitoring Library mit dem Baustein MomentCoefficients.
Verarbeitungskonzepte
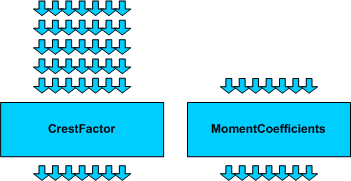
Die obige Abbildung benennt die verfügbaren Bausteine zur Berechnung von Crestfaktor und Kurtosis. Der Baustein CrestFactor kann Daten von mehreren Sensoren gleichzeitig auswerten, vorausgesetzt die Zahl der Einzelwerte ist für jeden Kanal gleich. Der Rückgabewert besteht aus einem Einzelwert für jeden Kanal. Die Einzelwerte werden in einem Vektor zurückgegeben. Dies soll in obiger Grafik durch die Verwendung der Pfeile in horizontale und vertikale Richtung angedeutet werden. Der Crestfaktor-Baustein erhält hier jeweils 5 Einzelwerte (vertikal) für 7 Kanäle (horizontal) und gibt entsprechend für jeden der 7 Kanäle den Crestfaktor aus.
Die Kurtosis kann durch den Baustein MomentCoefficients ausgewertet werden. Hierbei werden die Werte wahlweise für alle Kanäle und einzelne Zeitschritte übergeben, oder blockweise für mehrere Zeitschritte, was für einkanalige Signale aufgrund des geringeren Overheads effizienter ist.
Einhüllendenspektrum
Theorie
Die Bestimmung von Crestfaktor oder Kurtosis erzielt mit sehr geringem Aufwand frühe Hinweise auf das Vorliegen eines Schadens. Da die Zerlegung und Inspektion von Anlagenteilen immer einen – unter Umständen erheblichen – Aufwand bedeutet und gegebenenfalls eine Vielzahl von Lagern vorhanden sind, sind zusätzliche Diagnosemöglichkeiten von Interesse, mit denen sich beschädigte Lager oder sogar Einzelelemente genauer identifizieren lassen. Die Defekterkennung beruht auf der Auswertung von Stößen, die auf Beschädigungen der Kontaktflächen zurückgehen. Bei einem Schaden an einem rotierenden Teil entstehen die Stoßimpulse periodisch, wobei die Länge der Periode von der Frequenz abhängt, mit der ein Defekt eine Kontaktfläche berührt. Diese Stoßimpulsperiode hängt einerseits von der Rotationsgeschwindigkeit des Lagers, darüber hinaus jedoch auch von der Geometrie der Elemente ab. Somit kann die Periode der Stoßimpulse das defekte Bauteil identifizieren.
Die Stoßimpulse beinhalten sowohl einen hochfrequenten Signalanteil, welcher auf die Schwingungen des angestoßenen Maschinenteils zurückzuführen ist, als auch einen damit überlagerten (gefalteten) und eventuell auch modulierten niederfrequenten Anteilen, welcher Information über die periodische Wiederholungen der Stößen enthält. Diese niederfrequenten Signalanteile kann man durch die Berechnung der Einhüllenden (Envelope) ermitteln. Die Einhüllende kann durch Anwendung der Hilbert-Transformation im Frequenzbereich effizient berechnet werden. Eine vorherige Filterung durch einen Hochpassfilter, wie z.B. von der TwinCAT 3 Controller Toolbox bereitstellt, kann sinnvoll sein, ist jedoch nicht zwingend notwendig. Anschließend an die Berechnung der Einhüllenden wird das Leistungsspektrum des Einhüllendensignals ermittelt. Die markanten Frequenzen dieses Einhüllendenspektrums identifizieren die Stoßperioden.
Anwendung
Das Einhüllendenspektrum ist insbesondere ein Hilfsmittel für eine Diagnose, welche Aggregate oder welche Elemente eines Lagers möglicherweise defekt sind. Daneben ist für die Früherkennung von Schäden die Möglichkeit interessant, gezielt wichtige Signalanteile auszuwerten und Störanteile auszuklammern. Soll es für eine Früherkennung genutzt werden, so müssen die in Frage kommenden Schadfrequenzen aus der Lagergeometrie ermittelt und überwacht werden.
Das obige Diagramm zeigt die Einhüllende des schon zuvor verwendeten Signals eines beschädigten Wälzlagers. Das Zeitsignal wird durch die blauen Punkte markiert, die Einhüllende durch die rote Linie. Zum besseren Verständnis ist außerdem grün gestrichelt der gleitende Mittelwert des Zeitsignals geplottet, der nicht exakt Null ist, sowie hellblau die Beträge der negativen Werte im Zeitsignal. Man sieht, dass die Einhüllende immer sehr nahe an den maximalen Werten des Zeitsignals bzw. des Betrages der Zeitwerte liegt. Spitzen oder negative Ausschläge im Zeitsignal führen zu Spitzen in der Einhüllenden, während ein "Grundrauschen" im Zeitsignal durch die Einhüllendenbildung nur wenig verändert wird.
Analyse des Hüllkurvenspektrums
Da eine Sequenz von periodischen Stößen (Pulse Train) einem Signal mit vielen Oberschwingungen entspricht, treten im Hüllkurvenspektrum einerseits die Grundfrequenz und andererseits die ganzzahligen Vielfachen der Grundfrequenz auf. Dabei bestimmen sich – genauso wie bei einem Leistungs- oder Magnitudenspektrum – die den Spektralwerten zugeordneten Frequenz aus dem Index des Ergebnis-Array multipliziert mit der Frequenzauflösung der FFT, siehe Frequenzauflösung. Mit der Länge der FFT N und der Abtastrate fs folgte: Δf = fs ⁄ N und damit für die Frequenz des Frequenz-bin mit Index m : fm = (m-1) Δf (unter der Annahme, dass der Array-Index m mit 1 beginnt).
Zur Diagnose muss die Grundfrequenz der Stoßfolge identifiziert werden. Die Harmonischen sind zu erkennen an einer kammartigen Abfolge von spitzen Maxima, die einen gleichmäßigen Abstand haben. Die Grundfrequenz ist der Abstand zwischen diesen Maxima, in der Regel also die Frequenz des ersten Maximums dieser Reihe. Ihr Kehrwert ergibt die Periode der Stöße, die Einheit des Kehrwerts ist also eine Zeitdifferenz. Zusammen mit der Rotationsgeschwindigkeit der Achse, die zu messen ist, und den aus der Lagergeometrie ermittelbaren Drehzahlverhältnissen der Schadfrequenzen lassen sich dann die für die Ursache eines Defekts in Frage kommenden Bauteile ermitteln.
Charakteristische Schadfrequenzen in Wälzlagern
Die untenstehende Abbildung zeigt exemplarisch, welche Drehzahlverhältnisse in einem einfachen Wälzlager auftreten können. Grundsätzlich entstehen Stoßimpulse mit der Frequenz, mit der die Kontaktstelle zwischen zwei Lagerelementen eine Stelle mit beschädigter Oberfläche (im Bild an der Oberseite des Wälzkörpers ganz unten) passieren. Diese Kontaktstelle bewegt sich ebenfalls aufgrund der relativen Bewegung der Elemente zueinander. Die Drehzahl- bzw. Winkelgeschwindigkeit der Kontaktstelle kann basierend auf der Regel ermittelt werden, dass in einem korrekt funktionierenden Lager kaum Schlupf vorhanden ist, die Elemente also fast vollständig aufeinander abrollen.
Wälzlager-Geometrieparameter

Angenommen die Drehzahl frot einer Achse, die mit dem Innenring verbunden ist, wird gemessen, und die Durchmesser der Lagerteile verhalten sich wie folgt: Durchmesser des Innenrings DI, Durchmesser der Kugeln DB, Durchmesser Außenring DA. Die Zahl der Kugeln sei Z. Aus DI und DA ergibt sich der Pitch Diameter oder Rollkreisdurchmesser: DP = (DI + DA)/2. Dreht sich nun der Innenring mit einer Drehzahl von frot, so können hieraus die Impulsfrequenzen ermittelt werden. Zur Bezeichnung der Frequenzen sind die folgenden Akronyme gebräuchlich:
- BPFO (Rolling element pass frequency outer race): Frequenz, mit der die Wälzelemente den Außenring passieren.
- BPFI (Rolling element pass frequency inner race): Frequenz, mit der die Wälzelemente den Innenring passieren.
- BSF (Bearing spin frequency rolling elements): Frequenz, mit der die Kugeln/Wälzelemente relativ zu einer Lauffläche rollen.
- BPF (Ball pass frequency): Wälzelementfrequenz, die Frequenz, mit der ein Defekt auf einer Kugel eine Lauffläche passiert.
- FTF (Fundamental Train frequency): Rotationsgeschwindigkeit des Käfigs bzw. die Lagerelement-Modulationsfrequenz
Kontaktwinkel:
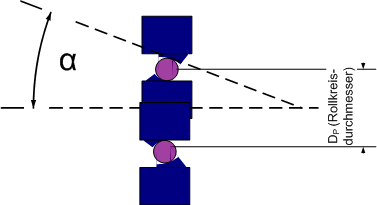
Für eine genaue Rechnung bei Lagern, die axiale Lasten aufnehmen, ist der Durchmesser der Kugeln mit dem Kontaktwinkel α zu korrigieren, mit dem die Kugeln die Lauffläche berühren: Db = cos(α) DB. Bei Radiallagern ist dieser Winkel 0°.Dann ergeben sich die folgenden praktisch genutzten Formeln:
BPFO = Z * frot /2 * (1 - Db / DP)
BPFI = Z * frot /2 * (1 + Db / DP)
BSF = frot /2 * DP/DB * (1 - (Db/DP)2)
BPF = 2 * BSF
Rotierender Innenring:
FTF = frot /2 * (1 - Db/DP)
Rotierender Außenring:
FTF = frot /2 * (1 + Db/DP) Dabei ist (BPFI + BPFO) / frot immer gleich der Anzahl der Wälzelemente Z. Von diesen Formeln ergeben sich in der Praxis leichte Abweichungen, da beispielsweise unter Belastung der Kontaktwinkel α variieren kann. Als einfache Faustregel wird häufig der Wert
fBPFI = 0.6 * frot * Z
als Indikatorfrequenz für einen Defekt des Innenrings verwendet, sowie
fBPFO = 0.4 * frot * Z
für einen Defekt des Außenrings. Zur Ermittlung der Lagergeometrie ist es sinnvoll Daten des Lagerherstellers hinzuzuziehen. Ebenfalls kann es hilfreich sein, Berechnungsprogramme zu nutzen, welche die Hersteller teilweise im Internet anbieten.
![]() | Die Typnummer eines Wälzlagers erlaubt keinen eindeutigen Rückschluss auf die Lagergeometrie; Parameter wie die Anzahl der Wälzkörper können sich durchaus ändern. |
Verarbeitungskonzept
Verarbeitungsschritte der Frequenzanalyse:
Analyseschritte:
Das obige Diagramm zeigt die Verarbeitungsschritte für das Einhüllendenspektrum sowie die Bausteine, die hier verwendet werden können. Dabei wird zunächst mit dem Baustein Envelope die Einhüllende berechnet. Anschließend wird, genauso wie bei der Berechnung des Spektrums eines beliebigen Zeitsignals, das Leistungsspektrum berechnet (Baustein PowerSpectrum ). Da das erhaltene Hüllkurvenspektrum bei nicht stationären Signalen relativ stark fluktuiert, empfiehlt sich, dieses wie zuvor im Abschnitt Frequenzanalyse erläutert, mit der Methode der Quantilsberechnung (Quantiles ) statistisch auszuwerten. Die erhaltenen Werte können mit einer Grenzwertüberwachung durch den Baustein WatchUpperThreshold automatisch auf die Einhaltung bestimmter Schwellwerte kontrolliert werden.