Introduction
Temperature control of the Plastics Processing Framework
The temperature controller of the Plastics Processing Framework has been optimized for
- a quick start-up,
- overshot-free response to setpoint changes,
- fast correction of faults,
- optimal heating and cooling ratio,
- independent parameter determination and
- exact response to setpoint changes during production
. These requirements cannot be realized with a normal PID controller, which is why further algorithms were implemented in addition to the PID controller.
The following figure shows schematically the structure of the controller.
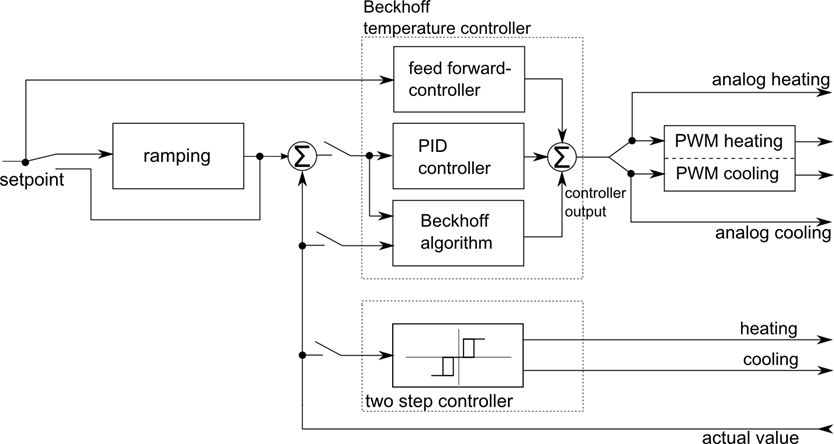
Determination of the path parameters:
- Takes place via the inflectional tangent method.
- Separate control parameter determination for heating and cooling.
- Determination of the idle load:
- Reduces overshoot on setpoint change.
- Parameter determination must be carried out in the controlled state.
- Takes only a few seconds and does not affect the actual temperature.
The control behavior:
- Large setpoint step-changes: Controlled by the Beckhoff algorithm. After reaching the set temperature, the PID controller is added. The optimally matched controller combinations enable fast and overshot-free control.
- Small setpoint step-changes: Are controlled by a modified PID controller, which has been optimized to handle large dead times.
- Exact response to setpoint changes: To guarantee exact response to setpoint changes during production, other stabilization measures have been taken in addition to the PID controller, such as taking transport and friction energy into account.
Other special features of the controller:
- Support of common thermocouples and Pt sensors.
- Error heating: Enables production even if the temperature sensor is defective.
- Extruder compensation: Calculates the shear rate and material transport into the process value.
- Zoning: Distribution of switch-on times within a PWM cycle avoids unnecessary power peaks.
- Power control heating tapes: Measures and checks the heating power of the heating tapes.
- I/O swap: If an input or output channel is defective, the operator can swap it from one channel to the other during operation.
- The temperature controller handles all terminal communication, so the controller only needs to be parameterized.
- Load and save routines are available for separate storage of product and machine data.
- Various filter functions (e.g. HMI filter) are available.
- Alarm handling functions are available.
- The library monitors:
- the operating state of the terminals,
- the autotuning,
- whether the current temperature exceeds certain limits,
- whether there is an appropriate temperature change for the heating power output.
Useful hints:
- Sample program: see Knowledge Base at Commissioning.
- Commissioning instructions: see Knowledge Base.
- How do I include other functions (power measurement, scope functions, etc.): see Knowledge Base in the FAQs.