MC_SYNC_STRATEGY
The data type MC_SYNC_STRATEGY defines the synchronization profile of the slave for e.g. a MC_GearInPosCA command.
TYPE MC_SYNC_STRATEGY :
(
mcSyncStrategyLate := 16#1,
mcSyncStrategySlow := 16#2,
mcSyncStrategyEarly := 16#3
)
END_TYPE
TF5410 | TF5420 | |
---|---|---|
MC Group with Pick-and-Place | MC Group Coordinated Motion | |
Examples:
The boundary conditions in the following examples are equal:
- The master motion is equal.
- The MasterStartDistance is equal.
- The distances (MasterSyncPosition – current master position) and (SlaveSyncPosition – current slave position) are in all three examples equal.
- The slave dynamics are equal.
- Configuration with one axis in the CA Group, one PTP axis as master.
- A motion command is issued to the master.
Example 1: mcSyncStrategyLate
The slave starts the synchronization as late as possible and with full dynamics (according to the input values velocity, acceleration, deceleration, jerk). It reaches the SlaveSyncPosition just in time with the correct gear ratio. The user has to take care that the master does not accelerate once the slave signals StartSync, since the synchronization profile is already planned with the maximal slave dynamics. The slave cannot violate its dynamic restrictions and therefore cannot compensate any master acceleration. This situation will result in an error at the function block.
- 1. Issue the command MC_GearInPosCA to the axis. The command becomes active while the master is still accelerating.
- The slave starts synchronizing as late as possible and with full dynamics, and reached the SlaveSyncPosition when the master reached the MasterSyncPosition (black x-Cursor).
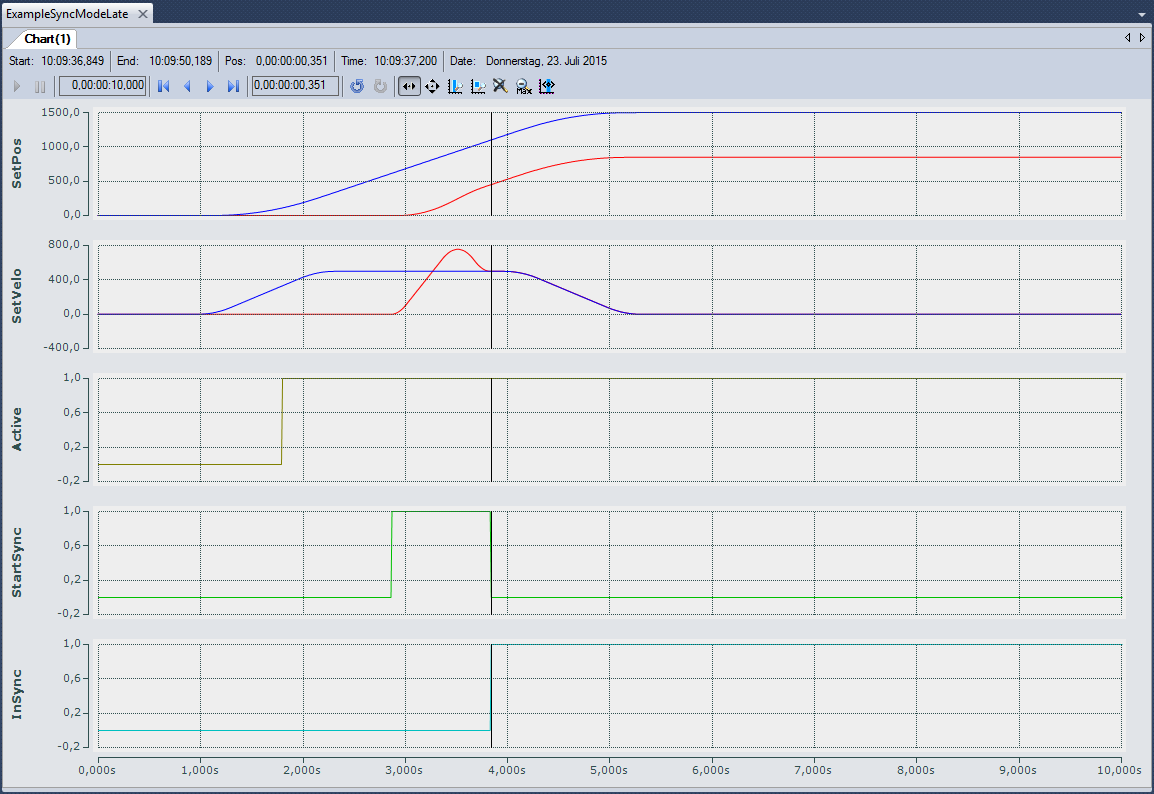
Example 2: mcSyncStrateySlow
The slave starts its synchronization in motion as soon as the master passes (MasterSyncPosition - MasterStartDistance) in the right direction if a MasterStartDist was set, otherwise as soon as the function block is Active. The dynamics of the slave are reduced so that the slave reaches the SlaveSyncPos with the right gear factor just in time when the master reaches the MasterSyncPos. The slave can compensate for an acceleration of the master if StartSync is also set, but only until the slave reaches its maximum dynamics.
- 1. Issue the command MC_GearInPosCA to the axis. The command becomes active while the master is still accelerating.
- The slave starts synchronizing as soon as MC_GearInPosCA is Active. The dynamics is reduced such that the slave reaches the SlaveSyncPosition at the same time the master reaches the MasterSyncPosition (black x-Cursor).
![]() | A synchronization on a standing master can lead to a high load if mcSyncStrategySlow is used. It is best to use mcSyncStrategyEarly in this case. |
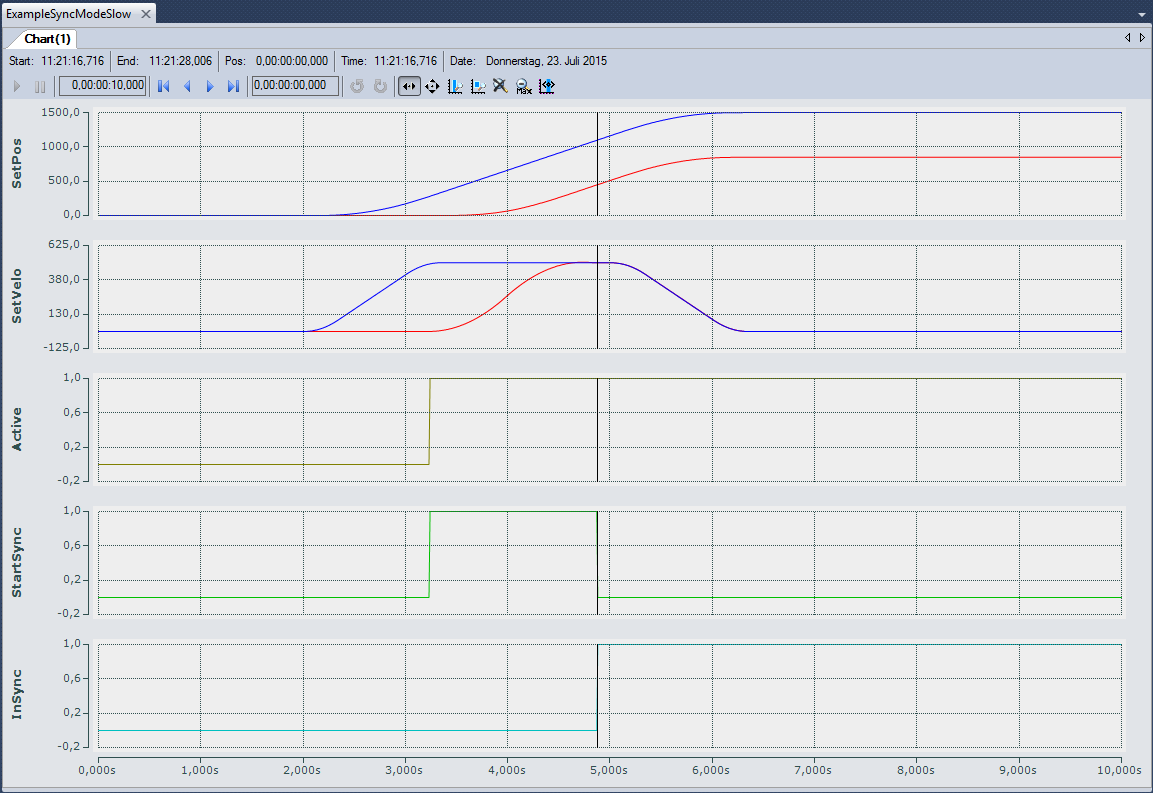
Example 3: mcSyncStrategyEarly
The slave starts synchronization immediately (if a MasterStartDistance is set: immediately after it was passed) and with full dynamics. The slave signals earlier InSync than demanded by the SlaveSyncPosition, but it is still guaranteed that demanded offset between master and slave (MasterSyncPosition – SlaveSyncPosition) is reached with the correct gear ratio. This strategy can synchronize on a standing master and is best suited if the master velocity is not constant. The slave will constantly try to synchronize. If the boundary conditions do not allow the slave to be InSync at the SlaveSyncPosition, this will not result in an error but the slave constantly tries to synchronize to the master.
- 1. Issue the command MC_GearInPosCA to the axis. The command becomes active while the master is still accelerating.
- The slave starts the synchronization as soon as MC_GearInPosCA is Active and with full dynamics. The slave is InSync as soon as possible, but still reaches the SlaveSyncPosition at the same time the master reaches the MasterSyncPosition (black x-Cursor).
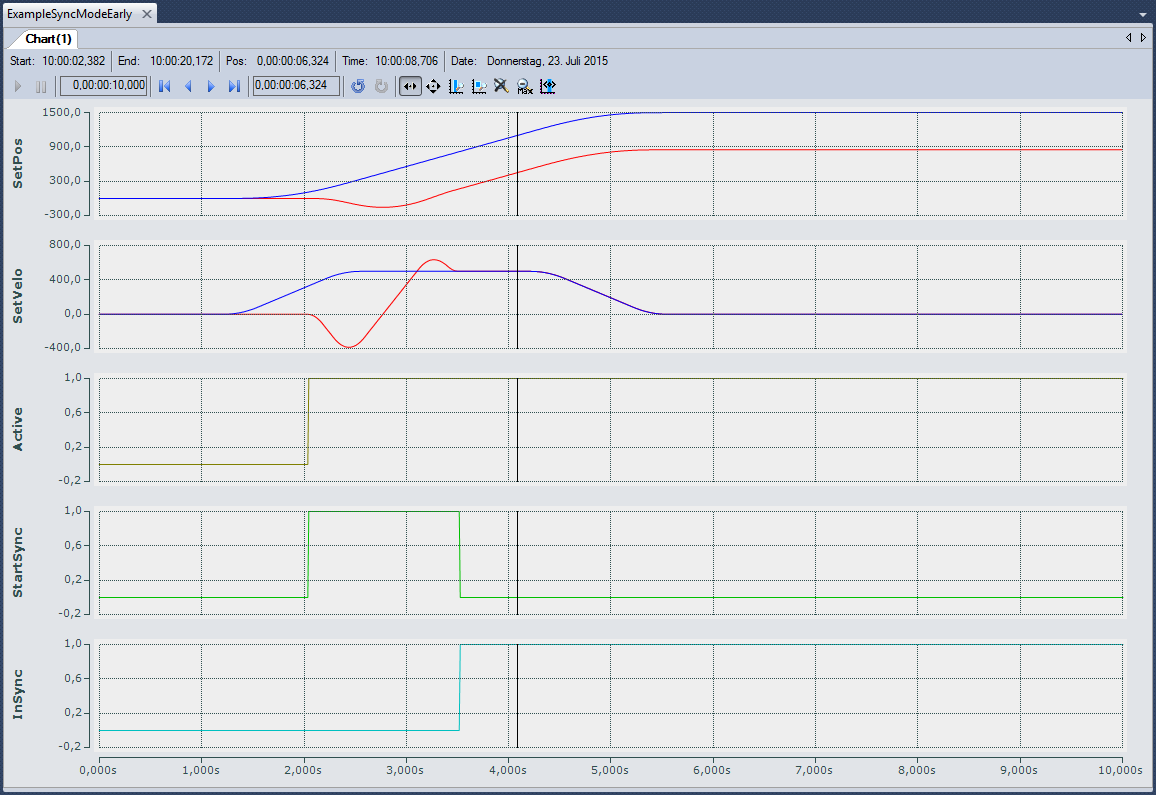
Requirements
Development environment | Target platform | PLC libraries |
---|---|---|
TwinCAT V3.1.4018.26 TF5400 Advanced Motion Pack V3.1.1.17 | PC or CX (x64) | Tc3_McCoordinatedMotion, Tc2_MC2 |