Description
Task of homing
The actual position value system of a machine axis is synchronised with the machine geometry by homing.
Homing means: Synchronising axis initialisation with the required axis coordinate system.
Homing refers to the entire process including referencing up to axis standstill.
Notice | |
Only when homing is completed are the software limit switch position of the axes monitored. |
![]() | Homing is always executed at line slope speed profile. |
![]() | Axis position after homing After homing is complete, the axis is not located at its reference point. The reason for this is that, when the cam/zero pulse signal occurs, the reference position is adopted and the axis is then decelerated. At the end of homing, the axis is then located at the deceleration distance away from the reference position. |
Absolute measuring system or incremental measuring system
Machine axes need not be homed if they are equipped with an absolute measuring system which supplies a unique axis or slide position in the entire motion range of the drive. This can be set by the axis parameter P-AXIS-00014 (abs_pos-_gueltig).
Notice | |
Homing is required for incremental measuring systems. This is obtained by setting the axis parameter P-AXIS-00014 (abs_pos_gueltig) to 0. The homing that is then required is described in detail below. |
Homing strategies
The following strategies can be executed with the controller to home an axis.
- Homing with reference cam, reference with zero pulse
- Homing with reference cam, reference with cam (without zero pulse)
- Referencing (without reference cam) with zero pulse
- Homing with fast and slow reversal
- Referencing by homing to fixed stop
Reference cam
The reference cam executes a pre-positioning and precise homing is then executed with the zero pulse from the encoder. A cam switch determines whether the axis is located on or next to the cam.
It is also possible to reference with cam without zero impulse. For example, this is a standard method with stepper motors in addition to referencing with “Move to fixed stop”.
Repeatability with referencing
Depending on the homing strategy and the hardware used, latching the axis position is executed either by the cam signal or the zero pulse. This permits exact speed-independent referencing.
If the hardware used does not support this, the homing accuracy is dependent on the speed at which motion takes place on the cam.
If the homing speed is selected, the maximum tolerance results from the sampling time of the function which executes position and cam detection.
For example, a maximum deviation of 200 µm results from a homing speed of 6 m/min and a sampling rate of 2ms.
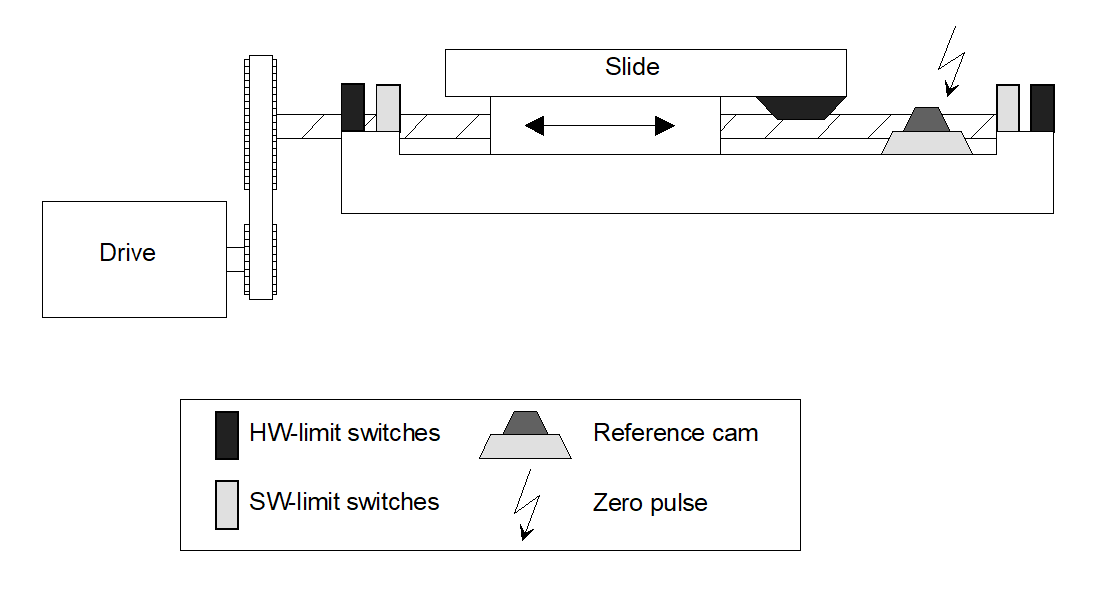
Zero pulse encoder
After pre-positioning with a reference cam, referencing can be executed very precisely with a zero pulse encoder if the hardware supports latching the counter state when the zero pulse is received. In this case, the repeatability of referencing depends on the homing speed. It is also possible to reference with only one pulse which may occur once in the motion range and is therefore unique. This is often used with rotary axes.
![]() | Fitting the zero pulse encoder The search for a zero pulse is only activated by the NC kernel if the reference cam is operated. The encoder should therefore be fitted so that the zero pulse occurs about half an encoder rotation after the cam is operated. This produces reproducible referencing. If the zero pulse occurs simultaneously with the cam, the zero pulse is either detected or not depending on whether the reference cam is operated before or after the zero pulse occurs. Axis referencing can then by shifted by one encoder rotation. |