Target Position Monitoring
Command | TPM |
Cancellation | End of block |
The command 'TPM' is used to trigger target position monitoring from the NC program. At the end of the geometry this always leads to an accurate stop on the set value side and subsequent checking of the target position window. Block relaying takes place when the monitoring conditions are met for all axes in the group.
Like for PTP, this function is enabled and parameterized individually for each axis. This means that different limits can be selected for auxiliary axes than for the path axes, for example.
Sample 1:
N10 G01 X100 Y100 F6000
N20 G01 X300 Y100 TPM
...
At the end of the motion of N20, target position monitoring is performed both for the X axis and for Y axis (provided target position monitoring is enabled for both axes).
Sample 2:
N10 G01 X100 Y100 F6000
N20 G01 X300 Y100
N30 M61 (Type Handshake)
N40 TPM
...
TPM can also be programmed in a dedicated block. In this case the last positioning is checked (of N20 in this case).
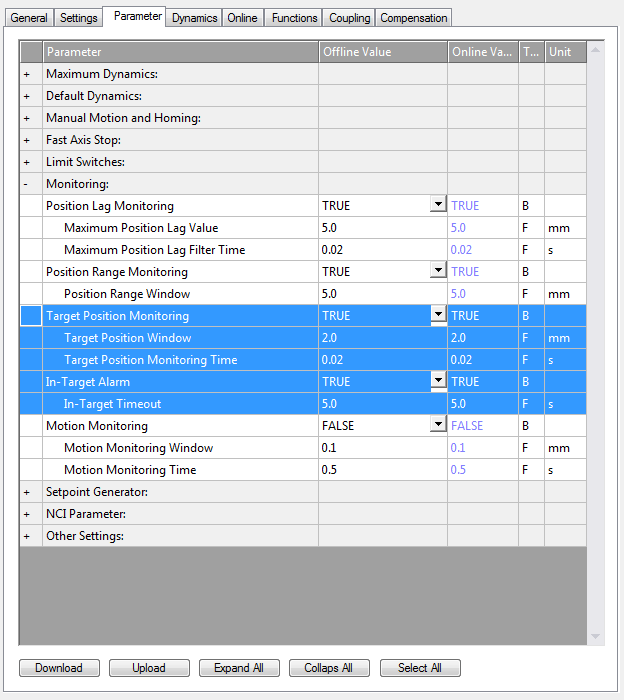
See also accurate stop (G09).