Path velocity at segment transitions
The reduction of the path velocity is explained below by means of an example. The contour of a stadium is particularly suitable for this purpose. The aim is for the feed angle of a tool relative to the path tangent to remain constant.
On the stadium straight, the orientation of the tool remains constant, i.e. the tool is not turned. In contrast, the orientation relative to the base coordinate system must be changed continuously within the circle. Assuming the path velocity in the transition between straight and circle is not reduced to zero, a step change in velocity is inevitably generated for the swiveling axis (but not for the path axes!).
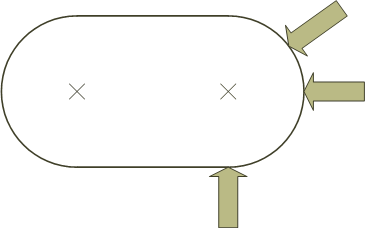
This step change in velocity of the auxiliary axis is freely parameterizable and depends on the machine. Extreme cases would be for the path velocity at such segment transitions to be reduced to zero, or for the velocity not to be reduced at all.
The global axis parameter 'VeloJumpFactor', which can be set individually for each axis, is used for the parameterization. The resulting velocity and the calculation is described in more detail in the TwinCAT NCI appendix on page Parameterisation.
Smoothing of the velocity at segment transitions
As has been described above, step changes in velocity can occur at the segment transitions. The size of these steps can be affected by the VeloJump parameter.
It is further possible for a tolerance sphere to be specified for every auxiliary axis. This sphere is symmetrical with the path at a segment transition. On entering this sphere, the velocity of the auxiliary axis is continuously modified to reach the set velocity at the exit of the sphere. The step changes in velocity are, in other words, eliminated. This does imply that the auxiliary axis is subject to a positional error when it is within the sphere. On entering the sphere the change to the new target velocity of the axis starts immediately. This avoids an overshoot in position, and the position is again precise at the borders of the sphere.
If it happens that the specified sphere is larger than 1/3 of the path, its radius is automatically restricted to that value.
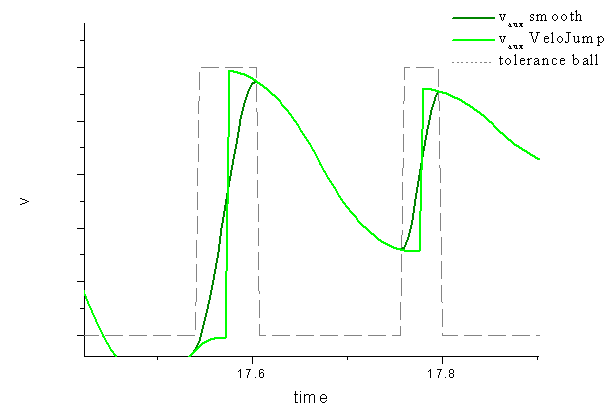
Selection and Deselection
The tolerance sphere of the auxiliary axis is an axis parameter (IO: 0x108). It can be set in TwinCAT XAE axis interface Specification Axes.
![]() | Parameterization of the axis parameters The parameters described here only take effect for axes that are in the interpolation group as auxiliary axes (Q1..Q5). For path axes (x,y,z) the parameters 'Velo Jump Factor', 'Tolerance ball auxiliary axis' and 'Max. position deviation, aux. axis' have no influence. |
Diagnostics
It is possible to record the tolerance sphere of each auxiliary axis and the position error that results from this for diagnostic purposes. It is also possible to access the variables via ADS. They are to be found in the "Index offset" specification for Group state (Index group 0x3100 + ID) (IO: 0x54n and 0x56n).
Effect on VeloJump, if the size of the tolerance sphere is reduced
If the size of the tolerance sphere has to be reduced due to the given geometry, the VeloJump parameter is automatically adjusted for this segment transition. I.e. the path velocity in the transition is reduced more strongly. So the dynamics of the auxiliary axis is not exceeded for smaller tolerance spheres.
Positional deviation of the auxiliary axis if the tolerance sphere has to be reduced
The parameter 'maximum permitted positional deviation of the auxiliary axis' only takes effect if the tolerance sphere would have to be reduced due to the geometry.
The aim is to keep the path velocity high despite the smaller tolerance sphere, as long as the resulting position error does not exceed a threshold value. To this end the velocity of the auxiliary axis is kept constant and the position error is calculated. If the error is smaller than the maximum positional deviation the velocity is maintained for this segment transition, and the resulting position error is compensated in the next segment (the tolerance sphere then becomes unnecessary for this segment transition).
In the event that the position error would exceed the maximum deviation, the reduced tolerance sphere takes effect, including the VeloJump factor. And the path velocity is reduced if necessary.
Example 1:
Initial conditions:
- Set tolerance sphere: 5
- Max. positional deviation: 1
- The given geometry results in an effective tolerance sphere of 0.2, for example
- The potential positional deviation is 0.3
Resultant behavior:
- The path velocity remains at a constant high level
- The velocity of the auxiliary axis is kept constant
- For this transition no tolerance sphere is required
- The resulting positional deviation is compensated in the subsequent segment
Example2:
Initial conditions:
- Set tolerance sphere: 5
- Max. positional deviation: 1
- The given geometry results in an effective tolerance sphere of 1.2, for example
- The potential positional deviation is 1.1
Resultant behavior:
- The tolerance sphere is adjusted
- The VeloJump parameter is adjusted
- The path velocity is reduced at the segment transition
- There is no positional deviation that has to be compensated
Parameterization
The parameterization of the maximum permitted positional deviation is an Specification Axes. By default this feature is switched off (deviation = 0.0)