Configuring the TwinCAT 3 Interface for Inventor®
Click the Configuration button in the TwinCAT add-in to open the configuration window, in which you execute settings for the axes and sensors.
Settings in the configuration window
You can execute the following settings in the configuration window:
- 1. Click the Configuration button in the TwinCAT add-in.
- The TwinCAT TE1130 Configurator is opened, in which the configurations can be executed. The Actuation configurator tab is opened.
- The default value 40 ms is entered in the input field Sample time.
- 2. Activate the checkbox for Dynamic sample time, so that the sample time adjusts automatically.
- The number of steps in TwinCAT is adapted to the calculation time of the CAD system.
- 3. Activate the checkbox for Automatically initialize, so that the TwinCAT Runtime for the model is automatically initialized immediately when it is opened.
- 4. On the Actuation configurator tab, select parameters as motion axes.
- 5. Activate the checkbox Actuators to filter axes by their name.
- All joints that have the prefix "axis_" in their name are automatically filtered and selected.
- 6. Configuration of collision sensors is performed on the Collision sensor configurator tab.
- 7. Select parameters as displacement sensors on the Displacement sensor configurator tab.
- 8. Activate the checkbox Displacement sensors to filter axes by their name.
- All joints that have the prefix "sensor_" in their name are automatically filtered and selected.
- The more advanced configurations can be found below.
Set sample time
In the TwinCAT Configurator, the sample time is used to set the ticks per sample for the Usermode Runtime. This means that with a set sample time of 40 ms and a base time of 1 ms in TwinCAT, 40 ticks are executed every time new parameter values are written or sensor values are read into the controller. The smaller this value is, the smoother the axes move in Inventor®, but the slower the controller runs.
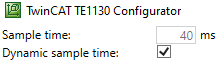
Select axes without filter function
- You are on the Actuation configurator tab.
- The filter function for actuators is disabled.
- 1. To select axes, drag and drop the desired parameters into the right-hand selection area of the configuration window.
- 2. Use the arrow keys to change the arrangement of the axes. This has no influence on the order in which these are created in the I/O master.
- The selected axes can now be used for the simulation.
Selection of displacement sensors without filter
- You are on the Displacement sensor configurator tab.
- The filter function for displacement sensors is disabled.
- 1. To select displacement sensors, drag them from the parameter list to the right-hand selection area of the configuration window.
- 2. Use the arrow keys to change the order of the selected displacement sensors. This has no influence on the order in which these are created in the I/O master.
- You can now use the selected displacement sensors for the simulation.
Setting the filter function
You can use a filter function for configuring axes and sensors, via which the desired parameters are automatically filtered and selected. To use this function, name the desired parameters appropriately with a prefix. For parameters, use the prefix "axis_", for example "axis_xxx". Joints used as sensors are given a name with the prefix "sensor_", for example "sensor_xxx". If you have named the parameters appropriately, they will be selected automatically.
To name axes and sensors appropriately, proceed as follows:
- 1. Select the Assemble tab.
- 2. Select Parameters.
- 3. The Parameters window opens.
- 4. Click in the field with the desired parameter.
- 5. Enter the desired name with matching prefix.
- 6. Confirm with the Done button.
- The parameters have been renamed.
To filter and select axes, proceed as follows:
- 1. Open the TwinCAT Add-In.
- 2. Click the Configuration button.
- The TwinCAT TE1130 Configurator window opens.
- 3. Check the Actuators or Displacement sensorscheckbox.
- The right-hand selection area of the configuration window is grayed out and only the axes and sensors with the prefix are selected.
Range monitoring
Range monitoring is activated and deactivated in the configuration window. The lower and upper limits for range monitoring are set in the TwinCAT project after scanning.
You have two options to activate or deactivate range monitoring:
Checkbox:
- 1. Check or uncheck the Range monitoring checkbox.
- Range monitoring of the selected parameter is now activated or deactivated.
Prefix:
- 1. Enter the abbreviation "rm" in the prefix of the axis or sensor.
- Range monitoring is activated for the axes and sensors with the prefixes "axis_rm_" and "sensor_rm_".
Configuration of collision sensors
In order to use the collision detection, you need to add "sensors" to the configuration.
- 1. Open the Collision sensor configurator tab.
- 2. Click the Add sensor button.
- A sensor configuration is added in the right-hand selection area of the configuration window.
- 3. Enter a name for the sensor.
- From here you have two options:
- 1. Drag and drop the parts that a collision check is to be performed for into the fields Part A and Part B.
- 2. Click the button Select part A in CAD or Select part B in CAD and then select the part in the CAD model.
- This sensor is displayed in the System Manager via the TMC file in the I/O master and can be linked there. You can find the sensors under the I/O group InventorCollisionsSensors.
Settings in the configuration window finished
In the next step, link the axes and sensors together, see chapter I/O master set up in TwinCAT. The TwinCAT project must be activated after linking. The Usermode Runtime can be started and stopped from TwinCAT as well as from Autodesk® Inventor® with the start and stop buttons.