Single-processor operation: the system grows along with requirements
PLC on the PC: programming, run time and field bus as an I/O system
A PC-based software PLC has a programming system, one or several run time environments and an I/O link that is established by a field bus. A user interface is realised with visualisation programs, SCADA etc. or with a Visual Basic / Visual C program.
PLC as software on the PC
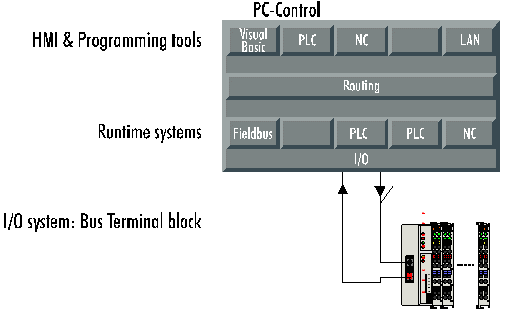
Single-processor solutions - growing system performance
The performance of software solutions for the PLC has long exceeded the performance of hardware PLCs and the measured speed has increasingly dropped with every new PC processor. For example, now only 15 µs is needed to execute 1,000 PLC commands on an Pentium III 600, thus "undercutting" a high-speed hardware PLC CPU by more than four.
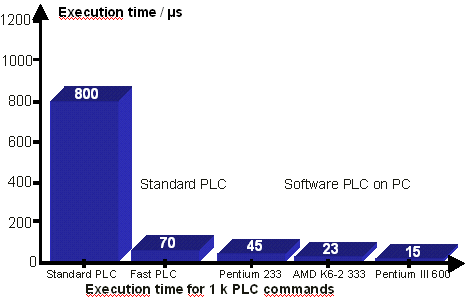
Very wide system boundaries
However, not only speed, but also system boundaries, no longer pose a restriction on the PC: in practice, program size, flag memory and the process image size no longer leave any wishes unfulfilled. The practical boundaries of PC technology are far wider than those of previous PLC hardware: In the 32-bit world of PC technology, PLC programs with a length of 32 Mbytes and with 4 Mbytes flag memory, combined with 64,000 inputs and outputs, are easily possible.
NC on the PC: Positioning on the PC and field bus as an I/O system
A PC-based software NC features a positioning capability (setpoint generation, position controller), an integrated PLC with NC interface, operator control programs for commissioning and an I/O link for axes that is established by a field bus. Data for the position controller is exchanged during the cycle via the field bus to the drives and from the measuring systems; the position controller is computer in the PC's processor. As in the case of PC PLC system, a user interface is realized with visualization applications and SCADA, etc. or with a Visual Basic / Visual C program.
NC as software on the PC
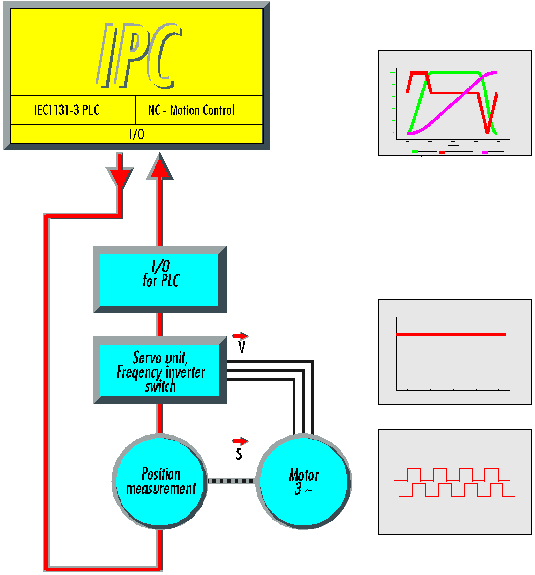
Central NC positioning in the PC processor
Thanks to the performance of the PC, it is possible to move drives with a PC simultaneously to the PLC task and, in doing so, the position controller is computed in the PC's processor: with computing times of less than 25 µs per axis (with a Pentium 200), a few dozen axes can easily be positioned simultaneously.
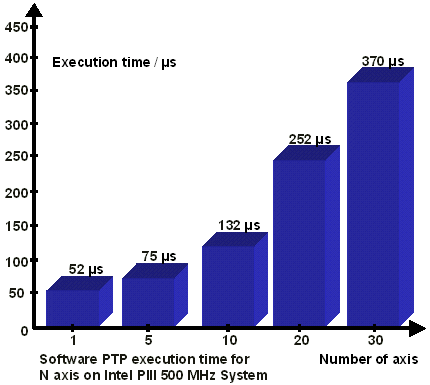
Depending on the number of axes and the chosen cycle time, TwinCAT can execute the operating control programs, the PLC and the NC simultaneously. TwinCAT supports system load design with load display tools.
System boundaries are constantly expanding
The most important item of news, however, is that these boundaries are constantly expanding, i.e. "the controller is growing along with requirements" by virtue of the fact that it is simply realized as software on a standard PC and automatically undergoes the same performance developments.