BK3xx0/BC3100 (Profibus)
The BK3xx0 Bus Coupler and the BC3100 Bus Controller are used for Profibus. Those specific properties which distinguish them from other Bus Couplers are described below. For an Overview of currently supported Profibus Bus Couplers BK3xx0, ...see
”Profibus” tab
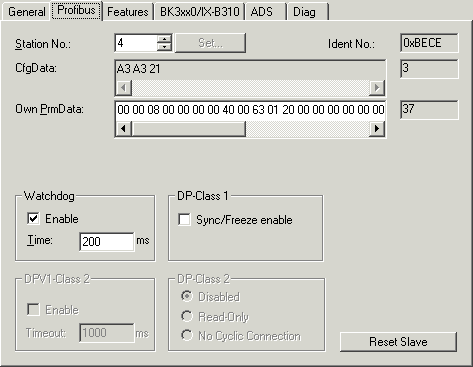
Stations No.: Each Profibus device requires a unique station number.
Watchdog: Switches on a watchdog function. The time (in ms) can be set when communication monitoring is actuated. The communication monitoring period should be at least 6 x greater than the cycle time. The minimum value is 10 ms.
PrmData: Allows you to edit the Profibus-specific parameter data (-> BK3xx0 Bus Coupler documentation). The size of the current parameter data is displayed. The PrmData can be entered either in text form (-> PrmData (text)) or occasionally via tabs ”BK3xx0 / BC3x00”.
CfgData: Displays the current configuration data (produced based on added terminals) and their lengths.
The settings DP class 1, DP class 2, DPV1 class 2, Set and Reset slave are only activated for FC310x (-> PROFIBUS DP slaves at FC310x)
”BK3xx0 / BC3x00” tab
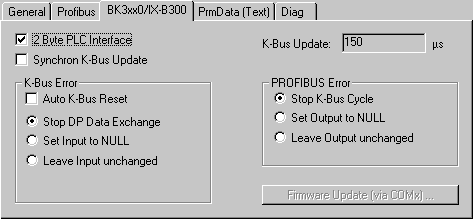
2 Byte PLC interface: Switches on the 2-byte PLC coupler interface. Register settings in the coupler are then carried out by, e.g. the PLC.
”PrmData (text)” tab
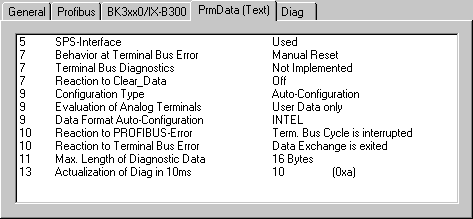
Click on a line to change the current value.
Diagnostic
The diagnosis for the PROFIBUS DP slaves at the FC310x is described in a separate section. The diagnosis for other I/O devices is described below.
Input Diagnosis
Each Profibus slave box contains two diagnostic input bytes which signal the state of each slave during the running time, and which can be linked, for example with the PLC.
Value | Description |
---|---|
0 | No Error |
1 | Error - more precise description in DpState |
Value | Description |
---|---|
0 | No Error - station is exchanging data |
1 | Station deactivated - slave has been deactivated, temporary state during StartUp |
2 | Station not exists - slave does not reply on the bus -> check whether slave is switched on, whether PROFIBUS plug is in, correct station address or bus cables |
3 | Master lock - slave is exchanging data with another master -> remove other master from bus or release slave again by other master |
4 | Invalid slave response - incorrect answer from slave, occurs temporarily if slave has ceased data exchange because of a local event |
5 | Parameter fault - check whether Bus Coupler / GSD file is correct, that station address is correct or that UserPrmData settings are correct |
6 | Not supported - DP function is not supported -> check whether GSD file is correct or whether station address is correct |
7 | Config fault – configuration fault -> check whether the added terminals / modules are correct |
8 | Station not ready -> station starting up, temporarily displayed during StartUp |
9 | Static diagnosis - slave signalling static diagnosis and cannot deliver valid data at present -> check operating state at the slave |
PROFIBUS Diagnostic Data
The Profibus diagnostic data sent by a PROFIBUS slave can be read by any TwinCAT program via ADS and/or signalled to any TwinCAT program. In this case, set ADS parameters as follows:
Net-ID: PC Net ID.
Port: 300
IndexGroup: 0x5000 + Device-ID
IndexOffset: Hi-Word: Station Address, Lo Word: 0x100
Length: 6 - 244
The diagnostic data are structured as described in the DP standard.