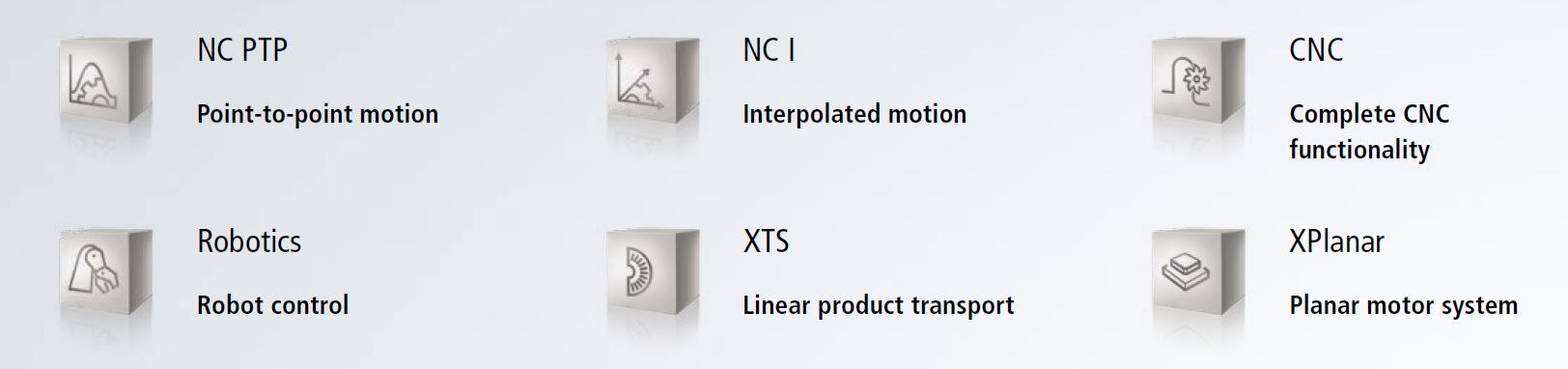
Motion | Overview
The TwinCAT modular system for simple to complex motion tasks
Simple to complex movements have to be realized in manufacturing and assembly processes, in building automation or in the entertainment industry.
TwinCAT Motion Control offers the ideal solution for almost every task. For this purpose, TwinCAT Motion Control, like TwinCAT in general, is composed of a large number of modules, from which the perfect solution can be put together for a specific task.
Overview of the TwinCAT Motion Control areas
TF50x0 | TwinCAT NC Point-to-Point (PTP) can be used to execute movements of individual axes or axis couplings. At the same time, it is the basic function block for further TwinCAT Motion functionalities. By representing axes in axis objects, a separation is made between physical and logical axis, so that rotary and linear, electrical and hydraulic drives can be programmed in the same way. Programming is usually done in the PLC. The Tc2_MC2 library with administrative and motion-initiating function blocks is available here. In addition to the pure movements of an axis from an initial position to a target position, movements of two axes can also be operated in a gear coupling. This is referred to as gearing. A coordinated master-slave motion with non-linear relationships is called cam plate coupling. This can be found in the TwinCAT system at TF5050 | TwinCAT NC Camming. TF5060 | TwinCAT NC FIFO AXES extend the table coupling concept for arbitrary, usually not cyclically recurring processes. In this case, rather than having one master-slave table prescribed in advance, the latest axis positions are constantly "topped up" by a PLC program. A special type of linear coupling is the flying saw, TF5055 | TwinCAT Flying Saw. Here, a slave axis is coupled 'flying' to a moving master axis at a specific position. As the name suggests, such couplings are often used when, for example, a board needs to be cut with a saw on a moving conveyor belt. | |
Interpolated path movements based on G-code are often used in machine tools (turning, milling, grinding, cutting) and 3D printers, but can also be used to move robots. Depending on the required path axes, this can be implemented with TF5100 | TwinCAT NC I or TF52xx | TwinCAT CNC. | |
Various serial, parallel and hybrid kinematic transformations – e.g. for the movement of a robot or a gantry – are available with TF511x | TwinCAT Kinematic Transformation, with new transformations being implemented continuously. Since a large part of the know-how is in the kinematics, users can realize and integrate their own transformations in C++. The movement positions are specified in Cartesian coordinates. The entire TwinCAT Motion construction kit is available to the user for programming – from simple PTP to cam plates to interpolating movements in G-Code. Classic articulated robots with their own controllers can be integrated with TF5120 | TwinCAT Robotics mxAutomation (KUKA) or TF5130 | TwinCAT Robotics unival PLC (Stäubli) in the PLC via a library. | |
TF5420 | TwinCAT 3 Motion Pick-and-Place is especially provided for the simple realization of handling tasks of gantry robots and other kinematics. Motion Pick-and-Place provides special procedures for blending motion commands and enables cycle-time optimized processing of positioning commands. The path movements can thus be executed more smoothly, i.e. more evenly overall. This is the prerequisite for high clock rates, gentle operation of the robot and safe handling of the products. | |
With XTS and XPlanar, Beckhoff has developed two complex drive systems in which a magnetically driven mover can move freely on a travel path or surface. System-specific software functionalities (configurators, track management, gap control, etc.) can be found in TF5410 | TwinCAT Motion Collision Avoidance and TF5430 TwinCAT Planar Motion and enable easy configuration and programming of these systems. |
There is a suitable solution for almost every motion task in the TwinCAT Motion area!