Encoder configuration
The encoder for the cam controller can be read via a dedicated I/O bus that is operated by the cam controller itself. If the velocity of the standard I/O bus is adequate, the encoder data can also be read by an encoder or a drive at this bus.
Encoder types
The cam controller can operate with encoders with different resolution. The encoder types offered in the selection diagram essentially differ in terms of bit width. An encoder that is not listed can therefore be inserted as a User Defined Encoder, after which the encoder mask must be configured to match the actual bit width (see Global dialog).
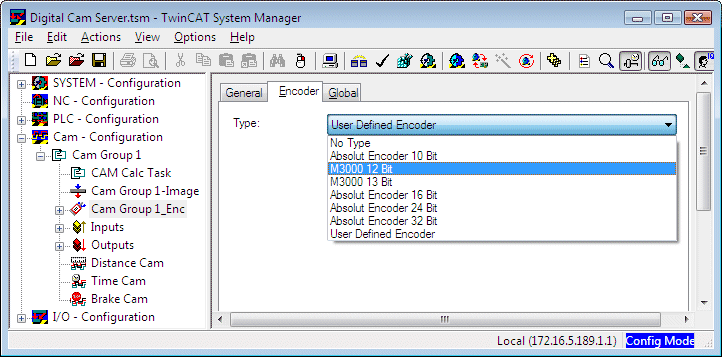
Encoder at standard I/O bus
The encoder data word is linked with the alternative cam controller encoder input.
- Alternative Input: Input for linking the hardware encoder count with the cam controller
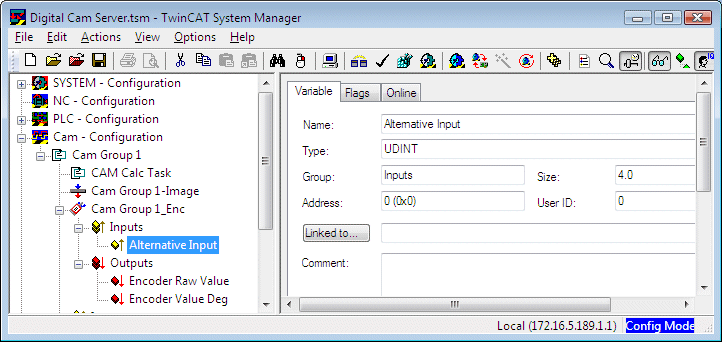
The outputs of the encoder process image can optionally be linked with the PLC.
- Encoder Raw Value: Current encoder count
- Encoder Value Deg: Current encoder position in degrees. The resolution is [1/10°] if the parameter Use Encoder Precision is set to FALSE and [1/1000 °] if set to TRUE.
The encoder parameterisation is specified in the Global dialog.
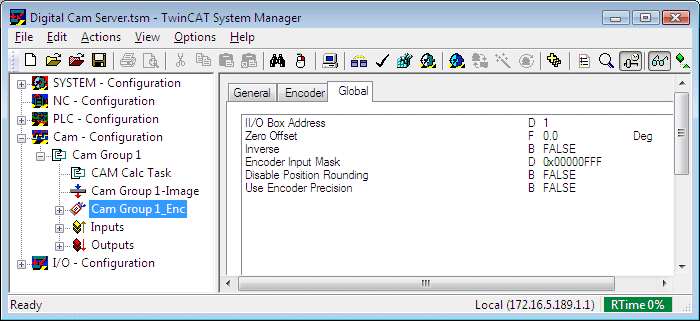
II/O Box Address: not required in this
case.
The II/O Box Address is required if the cam controller has
its own II/O-bus (option with C1200, C1220 or FC2000 card). In this
particular case the bus is managed by the cam controller, and the
address of the output box must be specified.
Zero Offset: Offset for adjusting the 0 degree position of the encoder.
Inverse: Reverses the direction of rotation of the encoder, if the physical count direction does not match the required direction of rotation.
Encoder Input Mask: The encoder value range is determined via this mask. The maximum encoder count is specified as a hexadecimal value. For example, 0x00000FFF is entered for a 12-bit encoder with overrun at a count of 4095.
Disable Position Rounding : Position rounding is used to adjust different encoder resolutions (e.g. 4096 increments) to the cam controller resolution (e.g. 360 degrees in 1-degree steps). Due to the rounding, the actual cam switching point will be within a window around the specified switching position (e.g. 90 degrees +/- 0.5 degrees).
Rounding can be switched off if it is not required.
Use Encoder Precision: The cam controller operates with a resolution of 1 degree, i.e. 360 steps per revolution, as standard. If a higher resolution is required, the cam controller can be operated with the resolution of the encoder. In this case, 65,536 possible switching points per revolution are available for a 16-bit encoder. (The cam switching positions are still specified in degrees.)
Changing this setting will also change the units of process data. The PLC program may be affected!
![]() | High-resolution encoders (from around 20 bits) have a very large number of possible switching points. In this case the router memory (see real-time settings) should be expanded to a larger value. |
Optional: Encoder at dedicated I/O bus
The cam controller can be assigned a dedicated I/O bus for the cam controller. This particular configuration operates with a Beckhoff Lightbus and requires an I/O card of type C1200, C1220, or FC2000. This option was developed for very short cycle times down to 80 µs and operates with an encoder and a digital 32-bit I/O box.
In many cases such a configuration is no longer necessary today and can be achieved through the standard configuration as described above. In any case, a fast I/O bus such as EtherCAT is required.