Temporary transition to the machine axes coordinate system (MCS)
![]() | In combination with kinematic transformations the use of this feature requires the license for the extension package "Transformations". |
By the functionality MCS, the active kinematics and / or cartesian transformation as well as all offsets included in the axes may be temporarily deactivated, so that the machine axes may be positioned directly. After leaving the MCS, the state being present before activation will be restored.
Tool change, e.g., mostly requires the approach of a definite tool change position with coordinates well known in respect to the machine origin. In a CS the approach of such a machine axes position may become complicated because in the NC-program the CS axes are positioned.
With the following instructions the temporary transition to the machine axes coordinate system will be activated and deactivated
#MCS ON [ EX TOOL ] Activation temporary transition in MCS (modal)
#MCS OFF Deactivation temporary transition in MCS (modal)
EX TOOL On tool change in the MCS the tool offsets will not be included. This takes place with #MCS OFF
In the MCS there are no restrictions concerning the usage of NC-functionality, the activation of RTCP / TLC , CS, ACS and ECS is not possible however.
Programmed offsets in the MCS are also valid only until its deactivation and will not be stored.
While changing the axes configuration by external axis exchange (e.g #CALL AX..) in the MCS, it has to be noted that for reactivating of the kinematics and / or cartesian transformation a definite axes configuration is absolutely necessary.
Programming example
N10 #RTCP ON
N20 #CS ON[1.5,0,32,14.5,0,45] (Activation of a CS)
N30 G01 G90 F5000
N40 X0 Y0 Z0
N50 #MCS ON EX TOOL (Transition to the machine-CS with the option)
(EX TOOL (Tool will be included with MCS OFF)
N60 LL TOOLCHANGE (Subroutine call for tool change)
...
N70 #MCS OFF (Deactivation of the MCS, RTCP and CS will be)
(reactivated again)
N100 #RTCP OFF
N110 #CS OFF
N400 M30
Programming example
Work piece: Cube 100x100x50
UNTERPRG1 (parts program 1) (Face milling of the current machining)
(plane)
N10 G01 G90 X0 Y-10 Z5 F250
N20 Z0 F2000 (Start-up motion )
N30 G91
N40 $FOR P1=0, 5, 1 (P1: Number of infeed motions)
N50 $FOR P2=0, 7, 1
N60 Y90
N70 X3
N70 Y-90
N80 X3
N90 Y90
N100 X-42 Y-80
N110 $ENDFOR
N120 Z-2 (Approach)
N130 $ENDFOR
N140 G90 Z50 (Return motion )
N150 M29
%L UNTERPRG2 (parts program 2) (Circle with centre boring)
N10 X0 Y0 Z10 F1000 (Linear and absolute approach motion)
N20 X0 Y0 Z5
N30 Z0
N40 LL UNTERPRG3 (Circular motion)
N50 Y35.34 (Approach bore location)
N60 X15
N70 Z0
N80 LL UNTERPRG4 (Bore cycle)
N90 M29
%L UNTERPRG3 (parts program 3) (Circular motion)
N10 X7.5 Y35.34 (Approach circle start point)
N20 G91 Z-4
N30 G90 G02 X7.5 Y35.34 I7.5 J0
N40 G01 Z20
N50 M29
%L UNTERPRG4 (parts program 4) (Bore cycle)
N10 G91 Z-5 (Relative bore motion)
N20 Z2
N30 Z-5
N40 Z2
N50 Z-5
N60 G90 Z20 (Lift-off motion)
N70 M29
N55 #TOOL ORI CS (Tool orientation)
N60 LL UNTERPRG1 (Contour machining)
N70 LL UNTERPRG2 (Contour machining)
N80 #CS OFF (De-selection machining coordinate system)
% Main program
N05 #KIN ID[1] (Machine kinematics 1)
N10 G74 Z1 X2 Y3 B4 C5 (Reference point return)
N20 T1 D1 (Tool selection)
N40 #RTCP ON (RTCP selection)
N50 #CS ON[0,-50,51,0,30,-45] (Selection of rot., shifted coord. syst.)
N52 G00 X0 Y0 Z5 (Positioning in new origin)
N55 #TOOL ORI CS (Tool orientation)
N60 LL UNTERPRG1 (Contour machining)
N70 LL UNTERPRG2 (Contour machining)
N80 #CS OFF (De-selection machining coordinate system)
N90 #CS ON[-50,0,51,0,30,-135] (Selection of rot., shifted coord. syst.)
N92 G00 X0 Y0 Z5 (Positioning in new origin)
N95 #TOOL ORI CS (Tool orientation)
N100 LL UNTERPRG1 (Contour machining)
N110 LL UNTERPRG2 (Contour machining)
N120 #CS OFF (De-selection machining coordinate system)
N130 #CS ON[0,50,51,0,30,-225] (Selection of rot., shifted coord. sys.)
N132 G00 X0 Y0 Z5 (Positioning in new origin)
N135 #TOOL ORI CS (Tool orientation)
N140 LL UNTERPRG1 (Contour machining)
N150 LL UNTERPRG2 (Contour machining)
N160 #CS OFF (De-selection machining coordinate system)
N170 #CS ON[50,0,51,0,30,-315] (Selection of rot., shifted coord. syst.)
N172 G00 X0 Y0 Z5 (Positioning in new origin)
N175 #TOOL ORI CS (Tool orientation)
N180 LL UNTERPRG1 (Contour machining)
N190 LL UNTERPRG2 (Contour machining)
N200 #CS OFF (De-selection machining coordinate system)
N210 #RTCP OFF (RTCP de-selection )
N220 Z120 (Return motion)
N230 #TOOL ORI CS (Tool orientation)
N240 X0 Y0 (Motion block because of tool orientation)
N250 X0 Y0 Z120 B0 C0 (Motion in machine co-ordinate system)
N260 M30 (End of program)
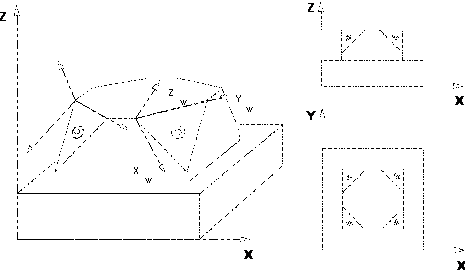