Tool orientation (TOOL ORI CS)
#TOOL ORI CS Selection of tool alignment (modal)
The first motion block that follows #TOOL ORI CS aligns the tool in parallel to the 3 rd main axis of the current BKS (W0 or MKS are possible, too). Programming the rotary axes in this block overrides the positions that are valid for orientation.
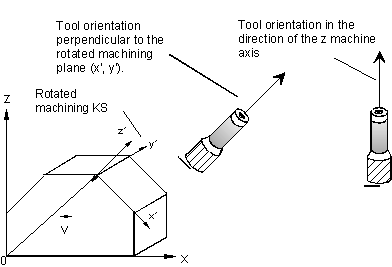
Programming example
N10 B10 C20 (Slanting the tool)
N20 #TOOL ORI CS (In next motion block, align tool in parallel to)
(the Z axis of the current BKS, here MKS)
N30 X0 Y0 (Motion block in the MKS, tool is aligned B=0,C=0)
N40 B25 C-80 (Slanting the tool)
N50 #TOOL ORI CS (Align tool in next motion block)
N60 #TRAFO ON (RTCP selection)
N70 #CS ON[0,0,0,-80,-30,45]
(Transition to a rotated BKS)
N80 X100 (Motion block in BKS. Tool alignm. from N50 refers)
(to the MKS, thus B=0,C=0)
N90 #TOOL ORI CS (Align tool in rotated BKS)
N100 Y150 (Tool is aligned in parallel to the Z axis of BKS)
N110 #TOOL ORI CS
N120 Z100 B45 C10 (#TOOL ORI CS is without effect in programming of)
(rotary axes)
N130 G18 (Change to the Z-X-interpolation plane)
N140 #TOOL ORI CS (Align tool in parallel to the Y axis)
N150 X0 (Tool aligned perpendicularly to the X-Z machining)
(plane)
M30