KIN_TYP_21
The kinematic structure of this machine consists of three translatory NC axes and one rotary NC axis in the tool.
Axis configuration in NC channel | ||
Axis designation | X, Y, Z, C (X1, X2, Z, C) | |
Axis index | 0, 1, 2, 3 | |
Kinematic structure | ||
| Tool axes | Workpiece axes |
NC axes | X,Y, Z, C | - |
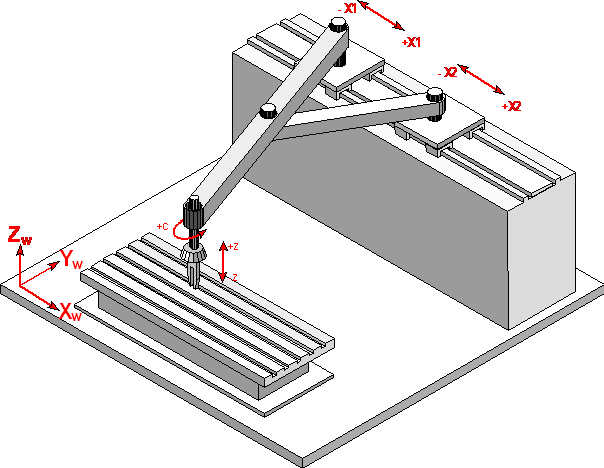
The plane XY kinematic is known as a variant of the shear kinematics. The struts (lengths l2, l1) are connected to the two linear sliders XM1 and XM2 via the rotary joints C and B. On point D these struts also are connected via a rotary joint. The strut CA (length l3) is attached to the strut CD with the fixed angleβ. The C axis is located on the top of this strut. The real tool holding strut (length l4) starts in the rotary point of the C axis and ends in the TCP. Related to the cartesian axes the C axis is not mechanically guided, this means it has to be compensated in dependency of the joint position.
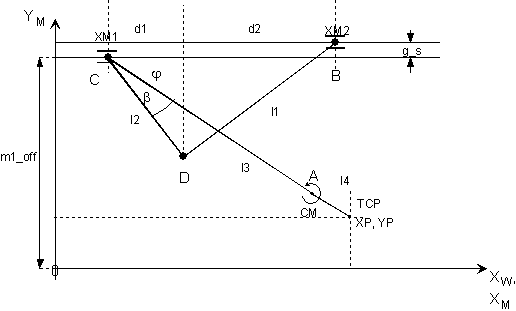
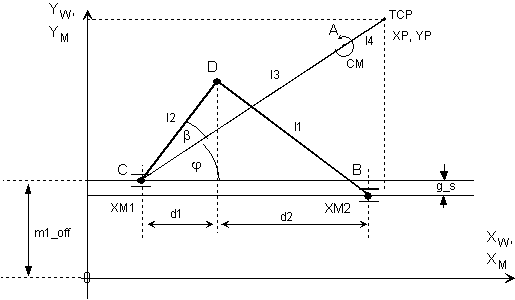
Offset data of the kinematic:
Parameter | Description | HD offset | param[i] |
---|---|---|---|
- | Z offset to the fixing point WZ | HD1 | 0 |
l1 | Strut length 1 | HD2 | 1 |
l2 | Strut length 2 | HD3 | 2 |
l3 | Strut length 3 | HD4 | 3 |
g_s | Offset joint points C to B | HD5 | 4 |
β | Fix angle between strut CD and CA | HD6 | 5 |
m1_off | Y position of drive 1, related to Y zero point WKS | HD7 | 6 |
phi_min | Minimum value for angleϕ(0°) | HD8 | 7 |
phi_max | Maximum value for angleϕ(90°) | HD9 | 8 |
- | X offset | HD10 | 9 |
L4 | Gripper offset | HD11 | 10 |
- | Variant of kinematic | HD12 | 11 |