KIN_TYP_12
The kinematic strut structure (referred to as tripod) consists of three translatory axes in a non-cartesian arrangement. Strut pairs that are parallel to each other carry the tool holder platform. The tool orientation is constant.
Axis configuration in NC channel | ||
Axis designation | X, Y, Z (Z1, Z2, Z3) | |
Axis index | 0, 1, 2 | |
Kinematic structure | ||
| Tool axes | Workpiece axes |
NC axes | X, Y, Z | - |
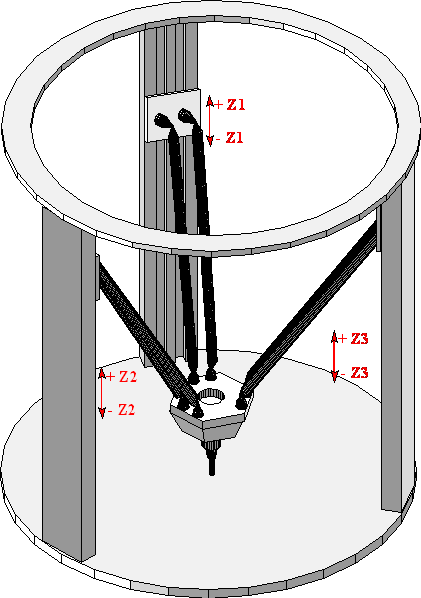
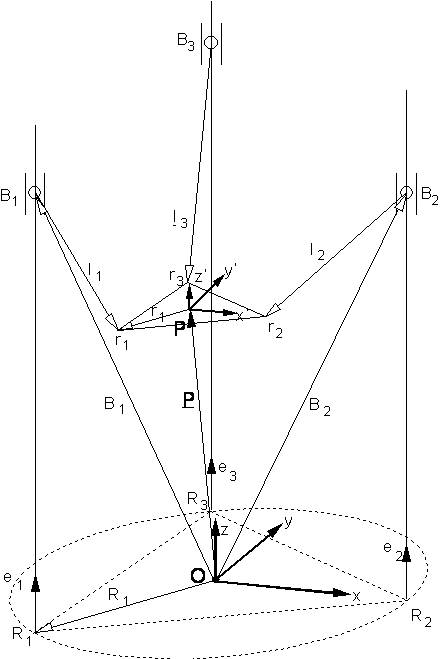
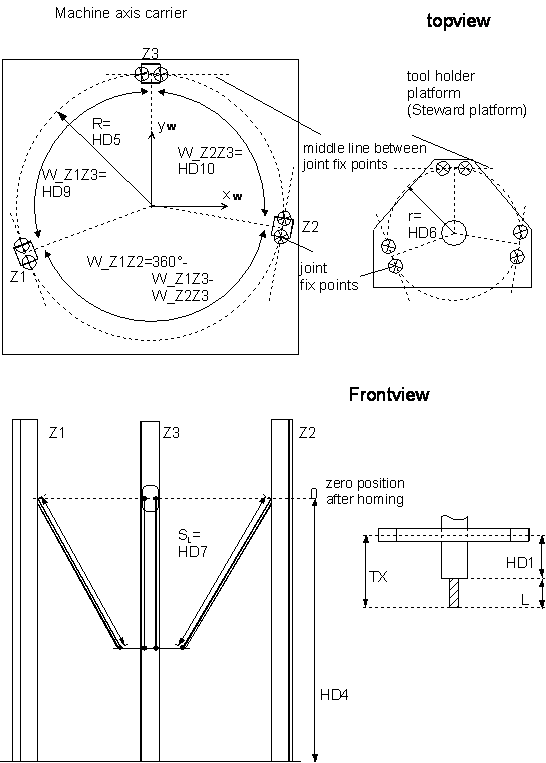
With the Parameter HD8 can be toggled between an ideal (1) and non-ideal (0) Tripod. An ideal Tripod has an angle of 120 ° between each strut. The non-ideal Tripod angles between the struts can be defined with the parameters HD9 and HD10. In this case the third angle is calculated:
Offset data of the kinematic structure:
HD offset | param[i] | Description |
---|---|---|
HD1 | 0 | Tool offset Z |
HD2 | 1 | Tool offset Y |
HD3 | 2 | Tool offset X |
HD4 | 3 | Z offset of machine reference point |
HD5 | 4 | Radius to the center point of the drives joint on each strut (big circle) |
HD6 | 5 | Radius to the center point of Steward platforms joints (small circle) |
HD7 | 6 | strut length to the joint center point |
HD8 | 7 | Switch between ideal or not ideal tripod transformation (makes HD9 / HD 10 available) |
HD9 | 8 | Angle between joint / strut 3 to joint / strut 1 |
HD10 | 9 | Angle between joint / strut 3 to joint / strut 2 |