Watchdog mechanism
![]() | Monitoring PLC by CNC, PLC task which triggers PLC’s sign of life alive_rw, must be executed with higher task priority than the two CNC-tasks SDA and COM (s. example TwinCAT). To prevent problems with CNC block preparation and large PLC projects it is additionally recommended to create an extra PLC task for the watchdog mechanism and to set a higher priority only for this task. |
Watchdog, CNC monitors PLC | |
Description | The CNC uses the data of this unit to monitor whether the PLC is still ready for operation. |
Data type | MCWatchDogUnit |
ST path | pMC[channel_idx]^.addr^.HLIHeadChannel_Data.MCWatchDogUnit_mc |
PLC operates functionality | |
Description | By setting this element to the value TRUE, the PLC indicates to the CNC that it supplies to the data for the watchdog functionality. |
ST element | . X_enable_w |
Data type | BOOL |
Value range | [TRUE = PLC supplies the data for a watchdog monitor, FALSE] |
Access | PLC writes |
Signal of the PLC | |
Description | CNC uses this element to determine whether the PLC is still ready for operation. This check is performed if elements PLC operates functionality and PLC present have the value TRUE. |
ST element | . X_alive_rw |
Data type | BOOL |
Value range | [TRUE = PLC signals that it is ready for operation, FALSE] |
Access | CNC detects whether this element changes from FALSE to TRUE within the time preset by element Watchdog cycle time. The CNC sets the value to FALSE after successful detection. PLC writes the value TRUE to this element in each PLC cycle to confirm its readiness for operation. |
Signal PLC not ready for operation | |
Description | If the CNC detects that the PLC is no longer ready for operation, it sets this element to TRUE. |
ST element | .X_alive_state_r |
Data type | BOOL |
Value range | [TRUE = PLC is ready for operation, FALSE = PLC is not ready for operation] |
Access | CNC writes |
Watchdog cycle time | |
Description | The values for the watchdog cycle time must be greater than the cycle time of the PLC to allow practical monitoring of the PLC by the CNC. |
ST element | .D_cycle_time_w |
Unit | 1 µs |
Data type | UDINT |
Access | PLC writes |
![]() | Monitoring CNC by PLC, PLC task which monitors CNCs sign of life alive_rw, must be executed with higher task priority than the two CNC-tasks SDA and COM (s. example TwinCAT). To prevent problems with CNC block preparation and large PLC projects it is additionally recommended to create an extra PLC task for the watchdog mechanism and to set a higher priority only for this task. |
Watchdog, PLC monitors CNC | |
Description | The PLC uses the data of this unit to monitor whether the CNC is still ready for operation. |
Data type | LCWatchDogUnit |
ST path | pMC[channel_idx]^.addr^.HLIHeadChannel_Data.LCWatchDogUnit_lc |
Signal of the CNC | |
Description | The CNC writes the value TRUE in this element in each interpolation cycle to confirm that it is ready for operation. |
ST path | .X_alive_rw |
Data type | BOOL |
Access | CNC writes the value TRUE in this element in each CNC cycle to confirm its readiness for operation. PLC detects whether this element changes from FALSE to TRUE within the time preset by element Watchdog cycle time. The PLC sets the value to FALSE after successful detection. |
Signal CNC not ready for operation | |
Description | If the PLC determines that the CNC is no longer ready for operation, it sets this element to TRUE. |
ST path | .X_alive_state_w |
Data type | BOOL |
Value range | [TRUE = CNC is ready for operation, FALSE = CNC is not ready for operation] |
Access | PLC writes |
Watchdog cycle time | |
Description | The NC kernel writes the cycle time of the interpolator in this element. The values for the watchdog cycle time must be greater than the cycle time of the PLC to allow practical monitoring of the CNC by the PLC. |
ST path | .D_cycle_time_r |
Unit | 1 µs |
Data type | UDINT |
Access | PLC reads |
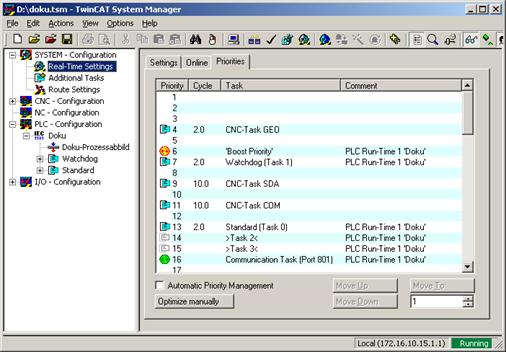