Reset
PLC reset, axis | |
Description | The PLC can be requested to perform a Reset via this axis-specific interface. For this purpose, the PLC must indicate, by setting element X_Enable, that it would like to be informed of Reset requests by the NC kernel. |
| LCControlBoolUnit, see description Control Unit |
Characteristics | Usage data item |
Access | CNC sets this value to TRUE for tasking a Reset for the PLC. The CNC sets this value to FALSE after the PLC has acknowledged execution of the Reset via element X_State. |
ST path | pAC[axis_idx]^.addr^.LcControlIpo_Data.LCControlBoolUnit_PLCReset |
Commanded Value | |
ST element | . X_Command |
Information flow | CNC -> PLC |
Data type | BOOL |
Value range | [TRUE = Reset request from CNC to PLC, FALSE] |
Return value | |
ST element | . X_State |
Information flow | PLC -> CNC |
Data type | BOOL |
Value range | [TRUE = PLC has performed Reset, FALSE] |
Request | |
ST element | . X_Enable |
PLC Reset, channel | |
Description | The PLC can be requested to perform a Reset via this channel-specific interface. For this purpose, the PLC must indicate, by setting element X_Enable, that it would like to be informed of Reset requests by the NC kernel. |
| LCControlBoolUnit, see description Control Unit |
Characteristics | Usage data item |
Access | CNC sets this value to TRUE for tasking a Reset for the PLC. The CNC sets this value to FALSE after the PLC has acknowledged execution of the Reset via element X_State. |
ST path | pMC[channel_idx]^.addr^.LCControlBahn_Data.LCControlBoolUnit_PLCReset |
Commanded Value | |
ST element | . X_Command |
Information flow | CNC -> PLC |
Data type | BOOL |
Value range | [TRUE = Reset request from CNC to PLC, FALSE] |
Return value | |
ST element | . X_State |
Information flow | PLC -> CNC |
Data type | BOOL |
Value range | [TRUE = PLC has performed Reset, FALSE] |
Request | |
ST element | . X_Enable |
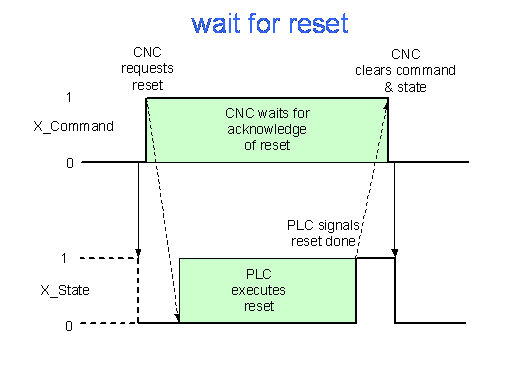
![]() | Before each new request and after receiving reset acknowledge the Signal X_State is cleared by CNC. |