Definition of coordinate systems
Owing to the structure of a machine and owing to the machining programs, it is necessary to allow for various coordinate systems. The totality of a machine represents the reference coordinate system in world coordinates. The individual axes, in turn, themselves, define coordinate systems and the workpiece and tool.
The two different coordinate systems essentially used are described below.
Axis coordinate system acs
Each axis has its own coordinate system. Each axis is mounted either on the machine base or on another axis. This means that the machine base or the corresponding axis forms the basis. The axis coordinate system of an axis is fixed in respect of the mounting point of this axis.
Part program coordinate system pcs
This coordinate system is used within the Geometry Description with DIN 66025 programming language. The data in a part program constitutes program coordinates. Exceptions are G functions referred to direct axis coordinates.
Other coordinate system designations should be listed for the purpose of completeness.
Machine coordinate system mcs
The machine coordinate system represents an abstract coordinate system. It is not bound to a fixed point of the machine. All other coordinate systems refer to this coordinate system.
Workpiece coordinate system wcs
This coordinate system is fixed to a fixed point of the workpiece. The description of the work piece by coordinate information refers to this system.
Tool coordinate system tcs
The tool coordinate system has its origin at the clamping point of the tool. Tool information (geometry) refers to this system. Length compensation is thus specified in tool coordinates. In the case of Cartesian machines, the Z axis may coincide with length compensation.
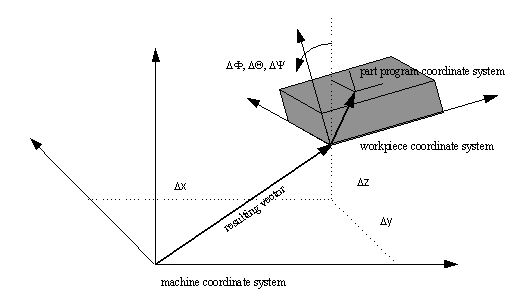
Data or variables described below consequently always refer to a specific coordinate system. Three coordinate systems are shown in the above illustration. The offsets shown ∆x, ∆y and ∆z and the orientations ∆Φ, ∆Θ and ∆Ψ represent the transformation parameters from mcs to wcs. The orientation angles are Eulerian angles.
The naming must be supplemented by means of a further suffix in order to allow for the time aspect. The illustration below shows the machining direction of a machining block. The end position represents the programmed value, the active position represents the current value of the interpolator and the current position represents the actual position including the control error.
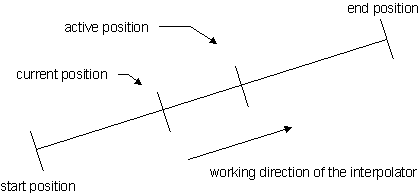