MC
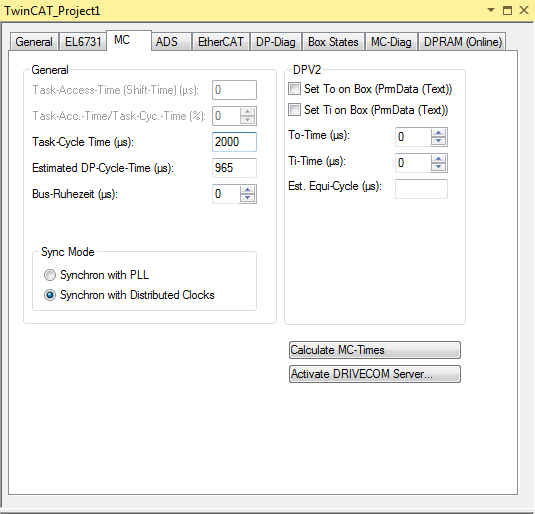
"Task-Access-Time (Shift-Time) (µs)" text box
The NC access time in microseconds is entered in the text box "Task-Access-Time (Shift-Time) (µs)". The NC access time indicates by how much the PROFIBUS DP cycle is offset relative to the TwinCAT cycle. The NC access time must be greater than the sum of the maximum TwinCAT jitter and the maximum mapping time. If the synchronizing task does not update its I/O at the start of the task but only at the end of the task, the task runtime of the synchronizing task is added to this sum, which must be smaller than the NC access time.
Use the "Calculate MC-Times" button to automatically set all equidistant parameters. However, the NC access time must be adapted, if necessary, because it depends on the maximum TwinCAT jitter, on the maximum mapping time and, if the synchronizing task only carries out its I/O update at the end of the task, on the runtime of the synchronizing task. The mapping time is influenced by all devices. Adding boxes or linking boxes to other devices also changes the mapping time. To avoid having to manually adjust the NC access time after the "Calculate MC-Times" button has been pressed, the ratio of the NC access time to the task cycle time can be defined with the "Task-Acc.-Time/Task-Cyc.-Time (%)" NumericUpDown control. A standard value for this ratio is 15 percent.
"Task-Acc.-Time/Task-Cyc.-Time (%)" NumericUpDown control
The "Task-Acc.-Time/Task-Cyc.-Time (%)" NumericUpDown control can be used to set the ratio between the task access time (shift time) and the task cycle time. The percentage of the task cycle time used by the task access time is displayed. If a ratio has been set here, the task access time does not have to be adjusted manually when the "Calculate MC-Times" button is used to calculate the DPV2 times.
"Task-Cycle Time (µs)" text box
The cycle time of the task that synchronizes the PROFIBUS is entered (in microseconds) in the "Task-Cycle Time (µs)" text box. The PROFIBUS runs task-synchronously with a task. This task can be a PLC task or an NC task, for example. The "Task-Cycle Time" should be greater than the "Estimated DP-Cycle-Time" and contain an adequate reserve with regard to the "Estimated DP-Cycle-Time".
"Estimated DP-Cycle-Time (µs)" text box
The "Estimated DP-Cycle-Time (µs)" text box contains a precalculated cycle time in microseconds, which the PROFIBUS is expected to need to pass through one DP cycle.
"Bus-Ruhezeit (µs)" NumericUpDown control
"Synchron with PLL" option
"Synchron with Distributed Clocks" option
"Set To on Box (PrmData (Text))" check box
If the "Set To on Box (PrmData (Text))" check box is checked, the "To-Time (µs)" NumericUpDown control is grayed out and inactive. The "To-Time" is then set individually for each slave device on the "PrmData (Text)" tab.
"Set Ti on Box (PrmData (Text))" check box
If the "Set Ti on Box (PrmData (Text))" check box is checked, the "Ti-Time (µs)" NumericUpDown control is grayed out and inactive. The "Ti-Time" is then set individually for each slave device on the "PrmData (Text)" tab.
"To-Time (µs)" NumericUpDown control
The "To-Time (µs)" NumericUpDown control can be used to set the "To-Time" uniformly for all slave devices if the "Set To on Box (PrmData (Text))" check box is not checked.
"Ti-Time (µs)" NumericUpDown control
The "Ti-Time (µs)" NumericUpDown control can be used to set the "Ti-Time" uniformly for all slave devices if the "Set Ti on Box (PrmData (Text))" check box is not checked.
"Est. Equi-Cycle (µs)" text box
"Calculate MC-Times" button
"Activate DRIVECOM Server…" button
The "Activate DRIVECOM Server…" button opens a dialog for saving a DriveCom server file as an XML file.