Self‑heating of RTD sensors
The measuring current through the sensor resistance inevitably and intentionally leads to a voltage drop across it. Thus, power is dissipated by the sensor, heating it and falsifying the measurement. The dissipation of heat to the environment via the air or another surrounding medium, the housing, as well as the object to be object to be measured via surface contact (e.g. by means of adhesive layer), can be a complex process. It is advisable to roughly check whether the self‑heating reaches a level that is relevant for the required measuring accuracy. Depending on the sensor, this can be the case with target accuracies of <100 mK.
Some sample values are used below to illustrate the effect; the method is to be adapted to the specific application if necessary.
About the sensor:
- A sensor may have a specified self‑heating coefficient of 0.5 mK/µW for example, depending on its surrounding medium.
- The power dissipation and the self‑heating can be calculated via the measuring current and the voltage drop across the resistive element. Caution: this is a nonlinear calculation!
About the Beckhoff terminal/module:
- The Beckhoff measuring device generates a measuring current through the RTD sensor (this can be done via an internal voltage source or a current source).
- One possible measurement method, implemented for example in EL32xx, could be the comparative measurement with a known reference resistance, shown here for the following considerations in the 2‑wire connection for simplification:
- If Usupply, Rreference and Umeas are known, then Rsense and thus the temperature T of the module can be calculated in the firmware.
- On the basis of the values given in the device documentation, the effect of the measurement amount on the R/RTD sensor can be calculated.
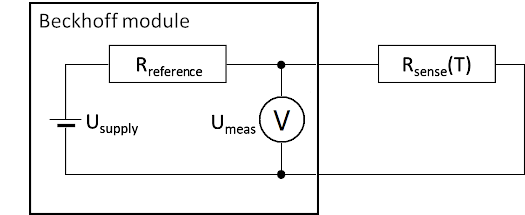
An example in numbers is shown below:
- The objective is to find out in which sensor and in which measuring range of the ELM3704 the least heat develops at a target temperature T.
- A sensor Pt100 or Pt1000 is used and measured from 0 100°C, the resistance range would thus be in the range 100...138 Ω or 1000...1385 Ω.
- The ELM3704 has the following properties (these are only guide values, the values given in the ELM370x documentation are valid):
- measuring range 5 kΩ, Rreference = 5 kΩ, Usupply = 2.5 V
- measuring range 2 kΩ, Rreference = 5 kΩ, Usupply = 2.5 V
- measuring range 500 Ω, Rreference = 5 kΩ, Usupply = 4.5 V
- measuring range 200 Ω, Rreference = 5 kΩ, Usupply = 4.5 V
- measuring range 50 Ω, Rreference = 5 kΩ, Usupply = 4.5 V
- Rreference and Rsense are in series, so the measuring current and thus the power at the sensor in relation to R or T in the possible five measuring ranges of the ELM3704 are simple to calculate:
- Hence, at T = 0 °C and thus RPt100 = 100 Ω or RPt1000 = 1000 Ω, the Pt100 with 0.08 mW transforms only half as much power as the Pt1000 with 0.17 mW. As consequence, a lower electrical power dissipation thus also causes a lower self‑heating.
- Nevertheless, the above sensor would heat itself by 0.17 mW ⋅ 0.5 mK/µW = 85 mK.
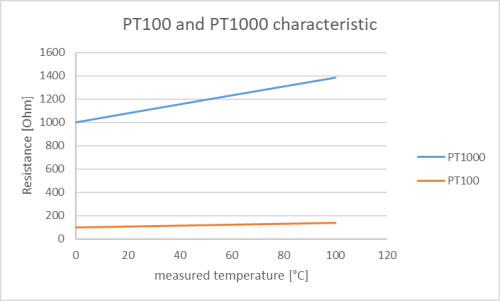
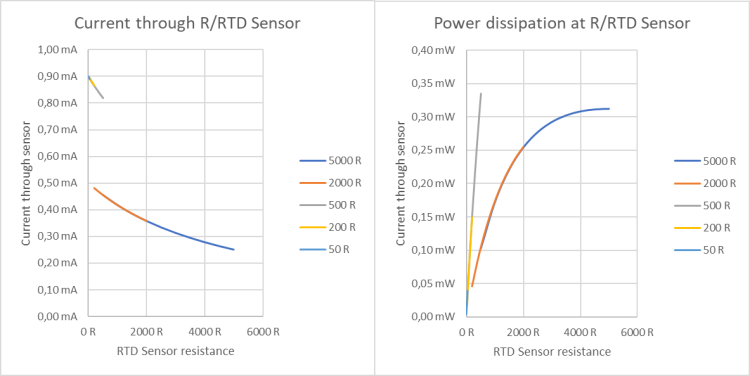
If self‑heating becomes relevant to the process under consideration, consider:
- whether the sensor can be changed,
- whether the thermal connection of the sensor can be improved,
- whether a continuous measurement is necessary or whether the measuring current of the Beckhoff module can be temporarily switched off from the controller, e.g. 1 second measuring, 10 seconds cooling and
- if the effect is numerically tangible and can thus be subsequently calculated in the controller from the temperature value.
However, this consideration focuses solely on the issue of self-heating.
To establish whether the sensor and the measuring range are suitable overall, they must also be checked with respect to other aspects such as noise, measurement uncertainty in the measuring range and the sensitivity of the sensor k = ∆R/∆Tambient.