Description
The actual position value system of a machine axis is synchronized with the machine geometry during homing. Therefore, referencing means the time of initialization of the axis with the required axis coordinate system. The entire operation, including referencing up to standstill of the axis is referred to as homing.
Notice | |
The axes are not monitored with respect to their software limit switch positions until after successful referencing. |
![]() | Homing always takes place with the linear slope speed profile. |
Absolute or incremental measurement system
Machine axes generally do not need to be referenced if they are equipped with an absolute measurement system that supplies a unique axis or slide position within the entire travel range of the drive. This can be set by means of the axis parameter P-AXIS-00014 (abs_pos_gueltig).
Notice | |
Homing is necessary for incremental measurement systems. To this end, the axis parameter P-AXIS-00014 (abs_pos_gueltig) must be set to 0. The necessary homing is described in greater detail below. |
Homing strategies
The following strategies for referencing an axis can be realized with the control system:
- Homing with reference cam, referencing with zero pulse
- Homing with reference cam, referencing with cam (without zero pulse)
- Homing (without reference cam) with zero pulse
- Homing with fast or slow reversing
Reference cam
Pre-positioning generally takes place with the reference cam and then the encoder is exactly positioned with the zero pulse. Whether the axis is on or next to the cam is determined by a cam switch. Referencing with the cam and without a zero pulse is also possible. For example, this is a common method in the case of stepper motors besides referencing with "travel to fixed stop".
Repetition accuracy during homing
When modern hardware is used, depending on the homing strategy the axis position is latched either by the cam signals or the zero pulse, thus enabling exact, referencing independently of the speed.
If the hardware used does not support this, the accuracy of a homing operation crucially depends on the speed at which travel to the cam takes place. At a chosen homing speed, the maximum tolerance results from the sampling time of the functionality that detects the position and the cam.
For example, a homing speed of 6 m/min and a sampling interval of 2ms results in a maximum deviation of 200 μm.
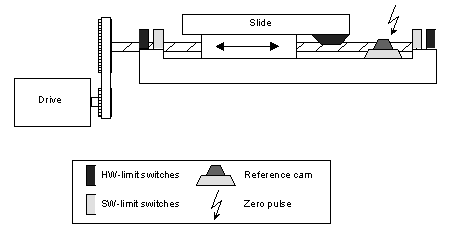
Zero pulse encoder
After pre-positioning with a reference cam, very precise referencing can take place with a zero-pulse encoder if the hardware supports latching of the counter status on arrival of the zero pulse. In this case, the repetition accuracy of referencing is independent of the homing speed. Referencing solely with a pulse which can occur once only, and thus clearly, in the travel range, is also possible. This is frequently used for rotatory axes.
![]() | Fitting the zero-pulse encoder The NC kernel activates searching for zero pulse only when the reference cam is actuated. This is why the encoder should be fitted so that the zero pulse arrives approximately one-half encoder rotation after actuation of the cam. This ensures reproducible reference. If the zero pulse coincides with the cam, it is either detected or not depending on whether the reference switch is actuated before or after the occurrence of the zero pulse. Referencing the axis may therefore be shifted by one encoder revolution. |