Introduction
In addition to normal contour programming, axes can also be operated as so-called gantry axes. Contrary to the normal synchronous operation, additional position deviation monitoring mechanisms are active and specific error reactions apply.
Notice | |
Prerequisites for gantry operation with several axes
|
Mechanical ("hard") gantry
In the case of the mechanical (also static) gantry, due the machine structure the axes are firmly coupled to one another and are defined by the machine's configuration. (Figure 1-1).
![]() | In the case of the mechanical gantry, the gantry coupling cannot be changed after the control system has been started up. |
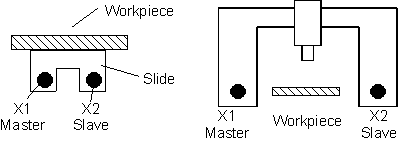
Programmable gantry ("soft" gantry)
Machines that do not require mechanical gantry operation thanks to their basic structure, for example milling machines with two independent slides, can be run in the gantry mode by means of programming. For example, this is necessary when such slides have to be coupled to one another for clamping and machining of large workpieces (Figure 1-2).
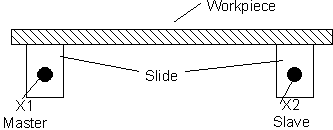
Monitoring functions
The axes specified in the gantry combination are coupled in terms of the setpoint. Coupling is monitored in terms of the actual value.
An offset for coupling can be specified between individual gantry axes.
Two limits can be specified for monitoring.
Absolute monitoring is active after referencing of the axes or relative before referencing.