Technology
The very compact EL72x1 servomotor terminal integrates a complete servo drive for servomotors up to 276 W.
Servomotor
The servomotor is an electrical motor. Together with a servo amplifier the servomotor forms a servo drive. The servomotor is operated in a closed control loop with position, torque or speed control.
The servo terminal EL72x1 supports control of permanent magnet synchronous motors. These consist of 3 coils which are offset by 120° and a permanent magnet rotor.
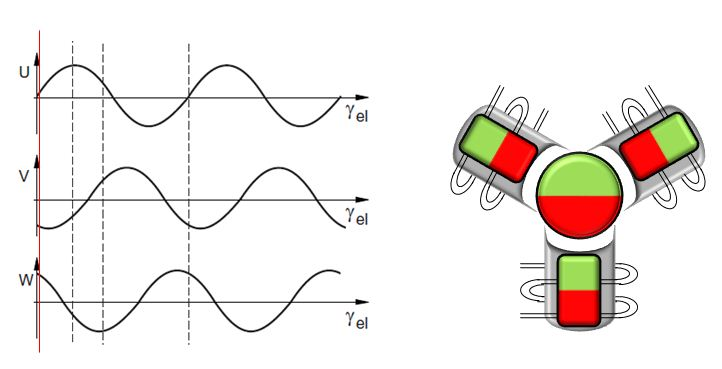
Servomotors particularly demonstrate their advantages in highly dynamic and precise positioning applications:
- very high positioning accuracy in applications where maximum precision is required through integrated position feedback
- high efficiency and high acceleration capacity
- servomotors are overload-proof and therefore have far greater dynamics than stepper motors, for example.
- load-independent high torque right up to the higher speed ranges
- maintenance requirements reduced to a minimum
The EtherCAT servomotor terminal offers users the option to configure compact and cost-effective systems without having to give up the benefits of a servomotor.
The Beckhoff servo terminal
The EL72x1 is a fully capable servo drive for direct connection to servomotors in the lower performance range. There is no need for further modules or cabling to make a connection to the control system. This results in a very compact control system solution. The E-Bus connection of the EL72x1 makes the full functionality of EtherCAT available to the user. This includes in particular the short cycle time, low jitter, simultaneity and easy diagnostics provided by EtherCAT. With this performance from EtherCAT the dynamics that a servomotor can achieve can be used optimally.
A rated voltage of max. 48 VDC and a rated current of max. 4.5 A enable the user to drive a servomotor with a rating of up to 276 W using the EL7211. Permanent magnet synchronous motors with a rated current of up to 4.5 A can be connected as loads. The monitoring of numerous parameters, such as overvoltage and undervoltage, overcurrent, terminal temperature or motor load, offers maximum operational reliability. Modern power semiconductors guarantee minimum power loss and enable feedback into the DC link when braking.
Beckhoff sets new benchmarks with regard to size with the integration of a fully-featured servo drive in a standard EtherCAT terminal – the EL7201 – with a width of just 12 mm. This small manufactured size is possible thanks to the latest semiconductor technology and the resulting very high power factor. And yet, despite the small dimensions, nothing has to be sacrificed.
The integrated fast control technology, with a field-orientated current and PI speed control, supports highly dynamic positioning tasks. Apart from the direct connection of motor and resolver, the connection of a motor holding brake is also possible.
Connection to the control system
A further big advantage of the EL72x1 is the easy incorporation into the control solution. The complete integration into the control system simplifies commissioning and parameterization. As with all the other Beckhoff terminals, the EL72x1 is simply inserted into the terminal network. Then the full terminal network can be scanned by the TwinCAT System Manager or manually added by the application engineer. In the System Manager the EL72x1 can be linked with the TwinCAT NC and parameterized.
Scalable motion solution
The servo terminal complements the product range of compact drive technology for Beckhoff I/O systems that are available for stepper motors, AC and DC motors. With the EL72x1, the range of servo drives becomes even more finely scalable: from the miniature servo drive up to 200 W in the EtherCAT Terminal through to the AX5000 servo drive with 118 KW, Beckhoff offers a wide range including the servomotors.
The AM31xx series was specially developed for the servomotor terminal EL72x1.
Thermal I²T motor model
The thermal I²T motor model represents the thermal behavior of the motor winding taking into account the absolute thermal resistance Rth and the thermal capacity Cth of motor and the stator winding.
The model assumes that the motor reaches its maximum continuous operating temperature Tnom during continuous operation with rated current Inom. This temperature corresponds to 100% motor load. During operation at rated current the motor model reaches a load of 63% after a time of τth=Rth∙Cth and slowly reaches its continuous operating temperature.
If the motor is operated with a current that is greater than the rated current, the model reaches 100% load more quickly.
If the load of the I²T model exceeds 100%, the requested set current is limited to the rated current, in order to protect the motor winding thermally. The load reduces to a maximum of 100%. If the current falls below the rated current, the load falls below 100% and the set current limitation is cancelled.
For a motor that has been cooled to ambient temperature, the time for reaching 100% load with a set current that exceeds the rated current can be estimated with τth∙Inom²/Iactual².
The actual load must be known for exact calculation of the time when the 100% load threshold is exceeded.
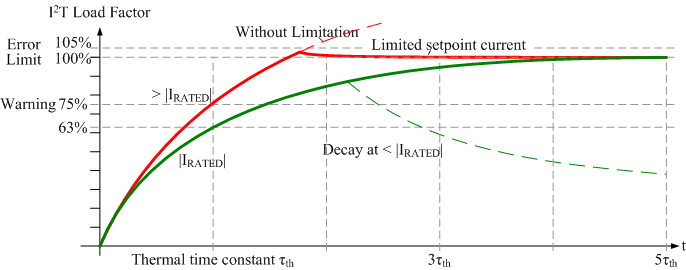