Configuring the main parameters - Settings in the CoE register
The specified data apply to an AS 1050-0120 stepper motor and are intended as an example. For other motors the values may vary, depending on the application.
Adaptation of current and voltage
Note | |
The motor may overheat! In order to prevent overheating of the connected motor it is important to adapt the current and voltage output from the stepper interface to the motor. |
To this end set the index 0x8010:01 "Maximum current" and 0x8010:03 "Nominal voltage" in the CoE register to suitable values (see Fig. "Adaptation of current and voltage").
Reduced current can be set in index 0x8010:02. This reduces the coil current when at a standstill (and therefore the power dissipation). Please note that the torque is also reduced.
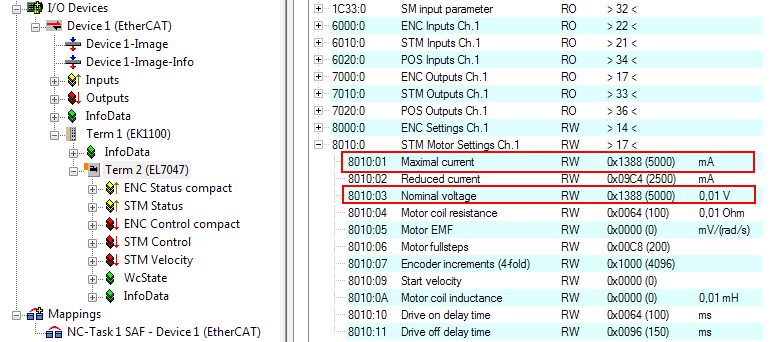
Base frequency selection
Microstepping is set to 1/64 and cannot be changed. However, the base frequency can be changed (default: 2000). To this end select the terminal and select the CoE Online tab. Change the base frequency by double-clicking on the index 0x8012:05 "Speed range" (Fig. "Setting the base frequency").
![]() | Adjusting the reference velocity The base frequency is directly linked to the reference speed of the TwinCAT NC, so that the reference speed always has to be adapted when the base frequency is changed. |
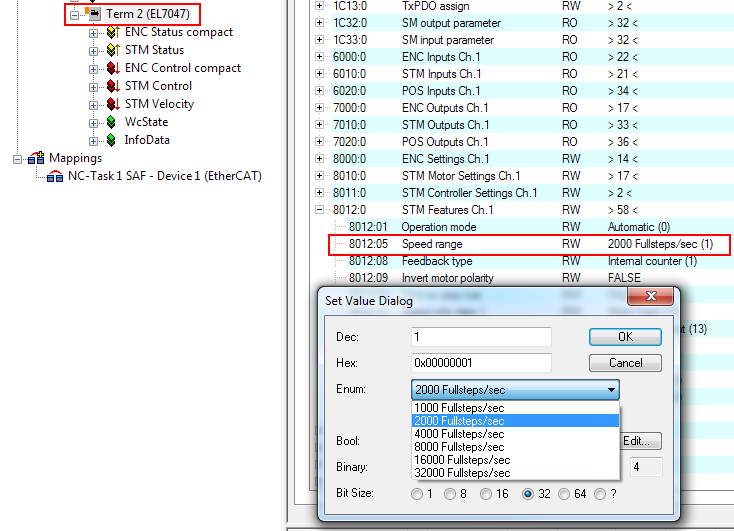
Selecting the feedback system (only for the module with encoder connections)
Two feedback system options are available for selection:
- Encoder: Use external encoder for position feedback
- Internal Counter (default): Use internal counter for position feedback
![]() | CoE "Feedback type" By default, the stepper module is set to internal counter. If an external encoder is used, the setting must be changed by double-clicking on the index 0x8012:08 "Feedback type" in the Enum menu (Fig. "Selecting the feedback system"). |
![]() | Adaptation of the scaling factor The feedback system is directly related to the scaling factor of the TwinCAT NC, so that the scaling factor always has to be adjusted when the feedback system is changed. |
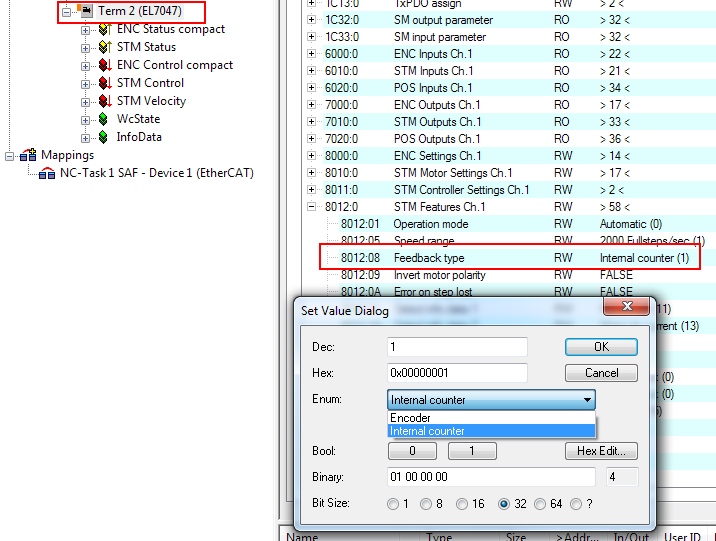