Sensorless operation
Because the default operation of a stepper motor with a constant load-independent current is not energy-efficient and leads to a permanently high thermal load, efforts are made to reduce this load.
Function
By analyzing the speed-proportional induced countervoltage, it is possible to control the stator current depending on the load with the aid of a machine model (without sensor/encoder), thereby significantly increasing the efficiency.
Since this operating mode requires a minimum amplitude of the magnitude of the induced countervoltage, sensorless control only works in the medium and upper speed range. In the lower speed range the motor is operated in standard mode. The changeover to sensorless operation take place via a programmable, motor-dependent switching speed. The switching speed is usually in the range between half and three revolutions per second (crossover velocity 1).
When sensorless control is activated, the transient phenomenon results in a slight mechanical jerk of the shaft, which is proportional to the load acting on the shaft.
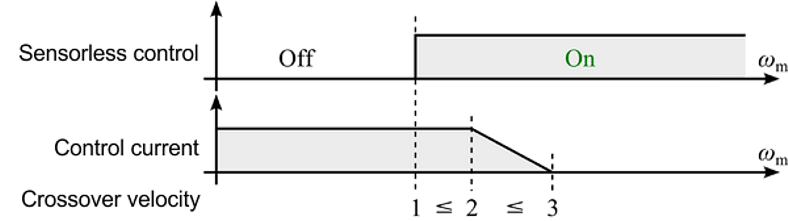
After switching on, the control current remains constant up to a second configurable speed and is reduced to a third parameterizable speed via a linear ramp.
A long control current ramp leads to a stronger stabilization of the transient phenomenon of the control. However, it also leads to a longer flowing constant motor current and therefore slightly higher losses.
Motor dependency
Due to the fact that the control is strongly dependent on the motor parameters, the controller parameters and motor behaviour itself, sensorless operation is limited to Beckhoff motors. This mode is not supported for motors from other manufacturers.
Parameterisation
Compared to the other operating modes, the parameterisation effort is relatively high. However, all the required necessary parameters are pre-specified via a startup list for the respective motor types. All that is required during commissioning is an adjustment of the speed control parameters, due to the given mass inertia ratios of the connected loads in the mechanical system.
For the speed controller, in principle the same dependence on the mass moment of inertia and the torque constant applies as in the Extended Operation Modes. Thanks to the lower-level sensorless control it is, however, possible to achieve a better overall result through different parameterisation.
All parameters required for sensorless operation can be found in the table "Overview of parameter settings for individual operating modes".
Summary
In this mode, above a minimum speed the motor current without encoder is controlled load-dependent. In this way it is possible to realise a particularly cost-effective drive in combination with high efficiency. The achievable dynamic performance of the drive control is slightly reduced compared to the other operating modes.
Advantages compared with standard mode
- Low current consumption (almost full load-dependence)
- High efficiency
- no encoder required
Prerequisites
- relatively high parameterisation effort required (speed controller + additional parameters)
- minimum speed required (if the speed is too low, the motor automatically switches to standard mode)
- dynamic performance somewhat lower than in standard mode
- Only possible with stepper motors from Beckhoff Automation (AS10xx)