Basics of inductive measuring probes
Inductive displacement sensors are transformers with a special design that are used for displacement recording / path length measurement. They are passive components that are available with different circuit options. A basic common feature is that an alternating voltage excites a coil system. A moving ferromagnetic core affects the inductance in the coils. The inductance change is proportional to the movement of the core and can be evaluated.
The EL5072 can evaluate the following inductive displacement sensors:
- Inductive half bridge
- LVDT (Linear Variable Differential Transformer)
- RVDT (Rotary Variable Differential Transformer)
Operating principle of inductive half bridge position transducers
Electrically, inductive half bridges (differential chokes) represent a Wheatstone half bridge with variable, sophisticated resistances. This consists of:
- two measuring coils
- a movable ferromagnetic core that moves inside the coils
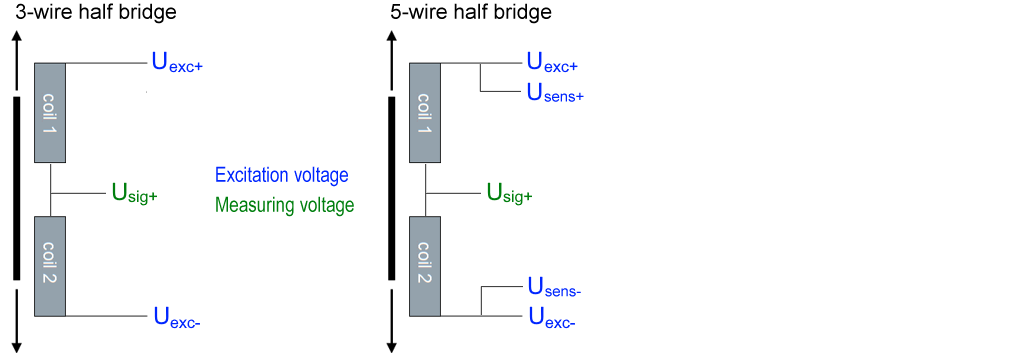
Principle of operation:
An alternating voltage is applied to the two coils connected in series. The ferromagnetic core changes the inductance of the coils when the measuring probe is deflected. In a symmetrical configuration and in the zero position of the position transducer, the impedance of the two coils is the same. If the core is moved from its center position, the impedance in the two coils changes in opposite directions. This results in a linear and absolute displacement signal, which can be measured with the EL5072.
Operating principle of Linear Variable Differential Transformers (LVDTs)
inductive LVDT displacement sensors generally consist of:
- a primary coil used for excitation,
- two secondary coils, which are arranged in phase opposition to each other and
- a movable ferromagnetic core, which serves to couple the primary and secondary coils.
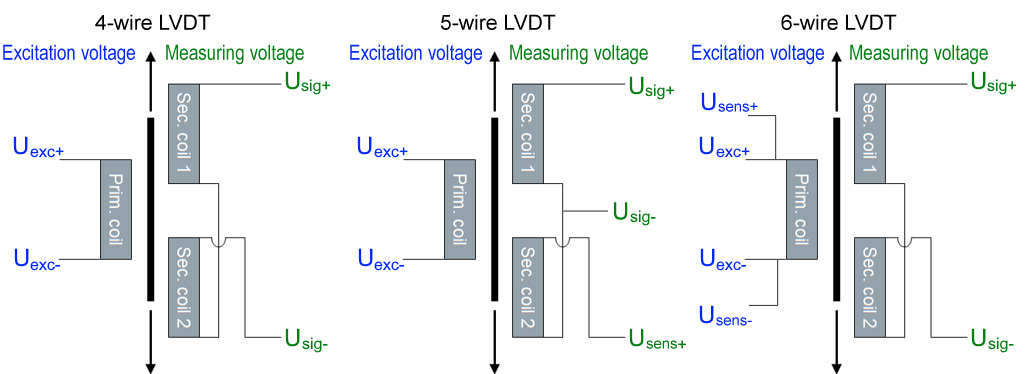
Principle of operation:
The primary coil fed with an alternating voltage induces a secondary voltage in the secondary winding. In a symmetrical configuration, the secondary voltages are equal in magnitude in the zero position of the position transducer but phase-inverted. The resulting signal voltage is zero. If the core is deflected, the induced voltage increases in one secondary coil and decreases in the other. This results in a linear and absolute displacement signal, which can be measured with the EL5072.
The deflection direction of the inductive measuring probe is determined by the movement of the core and the resulting phase shift between the excitation voltage Uexc and the measured signal voltage Usig. The general rule is:
- Negative deflection direction of the core relative to the zero position:
excitation voltage Uexc and signal voltage Usig are in phase - Positive deflection direction of the core relative to the zero position:
excitation voltage Uexc and signal voltage Usig are phase-shifted by 180° - Zero position of the core:
phase jump between excitation voltage Uexc and signal voltage Usig
In addition to the usual 4-wire connection, LVDT probes are also available as 5- or 6-wire versions. The 5‑wire version allows ratiometric measurement on the secondary side.
With the 6-wire version, the excitation voltage fed in is measured back from the sensor, thus minimizing influences on the voltage measurement which could be caused by a voltage drop along the supply lines.
Operating principle of Rotary Variable Differential Transformers (RVDT)
An RVDT rotary encoder represents a special design of the LVDT measuring principle. The main difference is that the LVDT uses a linear displacement of the core, whereas the RVDT uses a cam-shaped rotating core to measure the angular displacement.
To ensure correct output of the measured value, special Notes for RVDTs must be observed.