Process data
Parameterization
An EL2068 is parameterized via 2 tabs in the TwinCAT System Manager: the Process Data tab (A) for the communication-specific settings and the CoE directory (B) for the settings in the slave.
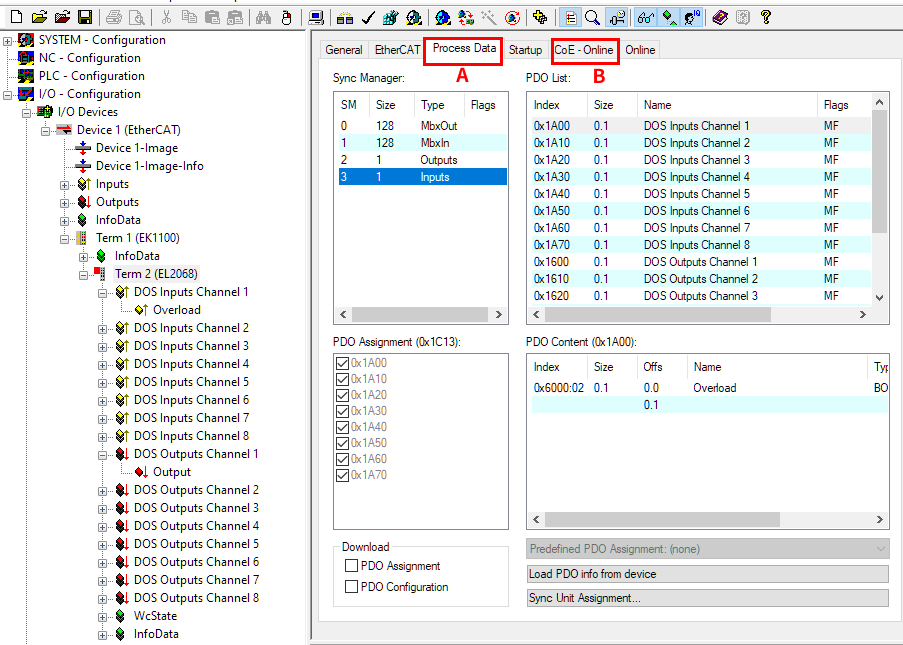
- Changes to the process data-specific settings are generally only effective after a restart of the EtherCAT master:
Restart TwinCAT in RUN or CONFIG mode; RELOAD in CONFIG mode - Changes to the online CoE directory
- are in general immediately effective
- are generally stored in non-volatile memory in the terminal/slave. They should be entered in the CoE StartUp list so that the settings are accepted after a replacement of the terminal. The CoE StartUp list is processed at each EtherCAT start and the settings are loaded into the slave.
Illustration of the process data and structural contents
The EL2068 provides two different process data for transmission:
- the diagnostics per channel “DOS Inputs Channel n” (8-bit),
- the switching state of the outputs “DOS Outputs Channel n“ (8 Bit)
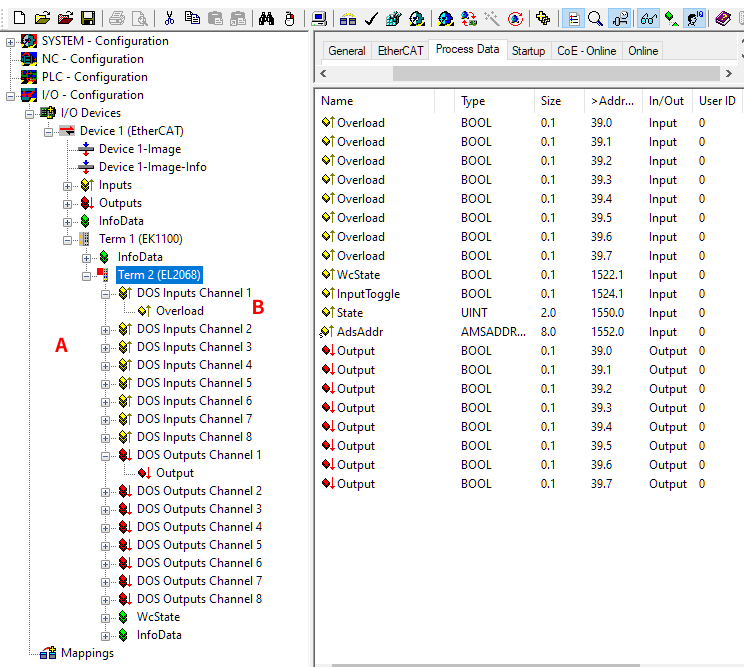
The plain text display of the bit meanings is particularly helpful not only in commissioning but also for linking to the PLC program.
By right-clicking on the Status variable in the configuration tree (A), the structure can be opened for linking (B).