Introduction
By means of electronic probe systems or sensors, movements are generated that are to superimpose the axes' programmed positions during interpolation of an NC program.
As a result, it is possible to easily implement distance control (e.g. touching a curved surface of a plate) or height control (e.g. compensation for thickness tolerances of the workpiece) with the control system.
Characteristics
A second measurement system is connected to the control system via a sensor. By means of this measurement system, axis-specific compensation values can be output to an axis in addition to the interpolated setpoint, thus correcting the actual position of the axis.
Distance control is activated or deactivated in the NC program.
Variables relevant to distance control can be parameterised via the axis machine data.
Distance control operates in the control system's interpolation cycle.
![]() | Distance control currently is available for SERCOS, Profidrive or CANopen drives only. |
Parameterisation overview
The movement generated via the distance control can be influenced via machine data.
- Activation of an average filter
- Maximum permissible correction value
- Maximum additive speed of the axis
- Maximum permissible actual value change of the probe system
- Maximum top axis position
- Minimum bottom axis position
- Tolerance value
These are activated or deactivated via the NC program.
Configuration overview
The sensor of the electronic probe system is connected to the controlled axis as a actual value sensor 2. Make sure that the first configured sensor is used for position control of the axis, and the second sensor for distance control.
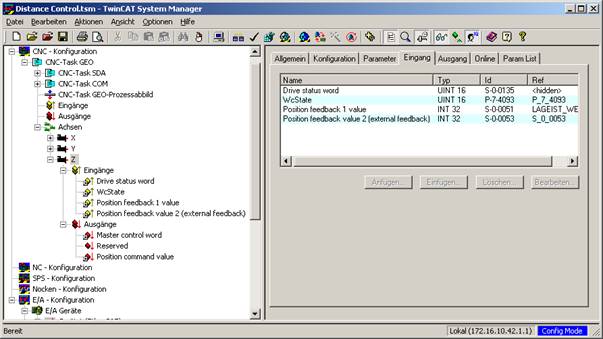
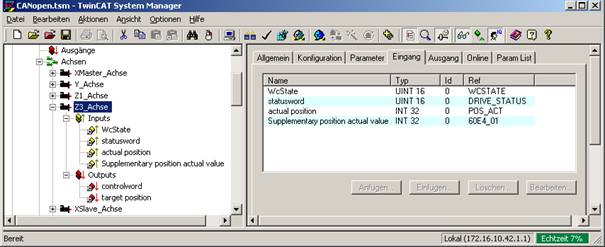
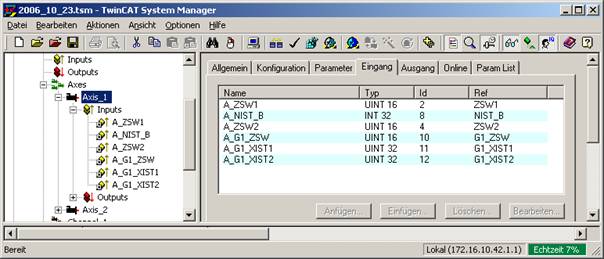
Notice | |
The axis-specific override acts on distance control. When override is 0, distance control is no longer active, and the current value is frozen. |