Data streaming versus automatic program commanding
Automatic program
In the automatic mode, the user generates the program in advance, and essential processes (geometry) are defined in it. After the NC program has been started, it must/can no longer be modified.
Via querying of variables/parameters, the process can still be influenced at the time of program decoding by the user interface or the PLC (conditional branches).
At the time of program execution, the axes are moved in accordance with the programmed geometry and information is sent to the PLC or execution is synchronized with the PLC.
Via specific NC functions, the PLC can still influence the process online:
- Speed: feed hold, override, reduced speed (safety)
- Interrupting/continuing, cancelling, reversing
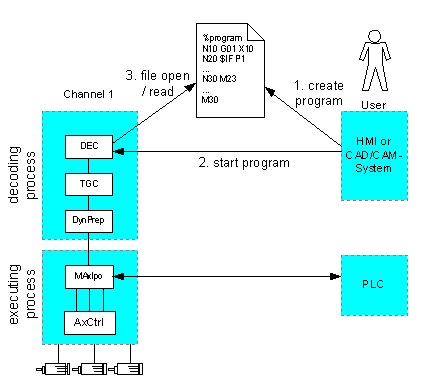
Function/action | Automatic program | Data streaming |
---|---|---|
Starting/initialising the NCX status data | Each time the program is started, the channel's default settings are restored, i.e. programs do not influence each other globally (exception: holding parameter, etc.). | Only at the start of streaming, i.e. status data of the NC remains valid throughout the duration of streaming |
Response to errors | NC reset with reset of the NC status data | NC reset with reset of the NC status data An NC reset without reset of the NC is currently not possible. |
Data throughput | Implicitly given by access to the file system | Given by filling the data stream "in good time", i.e. axis movement can be interrupted by delaying filling. |
Speed planning, look-ahead (HSC) | Cross-block speed planning is fully possible | Planning limited, possibly only possible for the specified blocks |
Process changes | Not longer possible after program starting if branches (e.g. via external variables) are not already considered in the program. | Program parts not yet specified can still be modified. |
Jumps/loops | Jumps to program flags possible, any higher-level language constructs with loops possible | No returning possible, no loop programming possible |
Fast forward | Via block search (jump to block number, block counter, file position) -> system state at forward position is established automatically | By programming system with corresponding omission of forward areas -> system state at forward position must be established manually. |
Reversing | NC functionality, currently possible by PLC command | Via NC functionality or by presetting an inverted data stream |
Automatic geometry changes at the block transitions (phases, radii, blending, splines, etc.) | Possible via standard NC functions | By CAD/CAM system, no consideration of several distance segments in the NC because execution is always enabled directly. Without implicit #FLUSH, also possible by NC |
Tool radius compensation | Standard NC function | To be executed by CAD/CAM system Without implicit #FLUSH, also possible by NC |