Configuration via TwinCAT
The TwinCAT automation software is a complete automation solution for PC-compatible computers. TwinCAT turns any compatible PC into a real-time controller, an IEC 61,131-3 Multi-PLC, NC positioning system, the corresponding programming environment and user interface. TwinCAT supports several different CANopen PC cards. Beckhoff recommends the CANopen PCI master card FC5101, which can also be obtained as a two-channel version (FC5102).
System Manager
The TwinCAT system is used for configuring the FC510x CANopen master card. The System Manager provides a representation of the number of programs of the TwinCat PLC systems, the configuration of the axis control and of the connected I/O channels as a structure, and organizes the mapping of the data traffic.

For applications without TwinCAT PLC or NC, the TwinCAT System Manager configures the programming interfaces for a wide range of application programs:
- ActiveX control (ADS-OCX) for e.g. Visual Basic, Visual C++, Delphi, etc.
- DLL interface (ADS-DLL) for e.g. Visual C++ projects
- Script interface (ADS script DLL) for e.g. VBScript, JScript, etc.
The TwinCAT system manager has the following properties:
- Bit-wise connection between server process images and I/O channels
- Standard data formats such as arrays and structures
- User defined data formats
- Continuous variable linking
- Drag and Drop
- Import and export at all levels
Procedure when configuring the CANopen input/output modules
- The corresponding CANopen master PC card is selected first, and inserted into the I/O configuration.
- The baud rate and, if appropriate, the master node ID (for the heartbeat protocol) are now set.
- Following the master card, the bus nodes are then inserted:
- The appropriate Bus Terminals or I/O versions and extension boxes are now appended at the CANopen Bus Coupler, Compact or Coupler Box.
- The communication properties for these bus nodes are now configured:
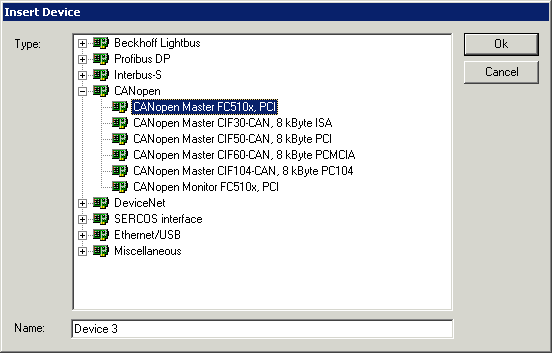
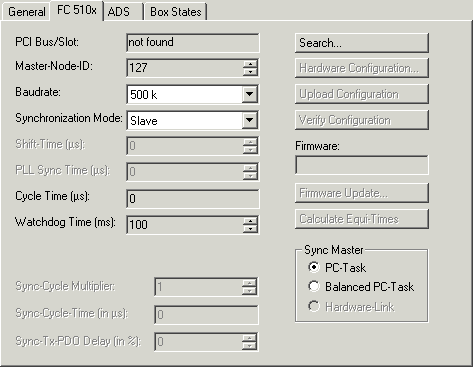
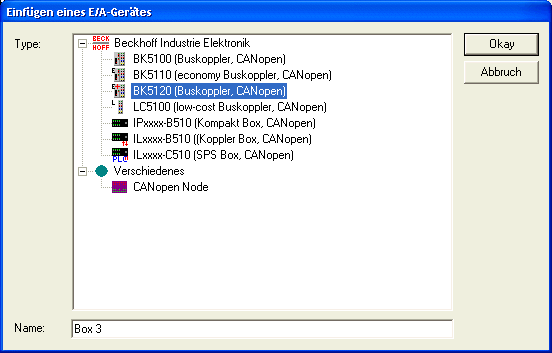

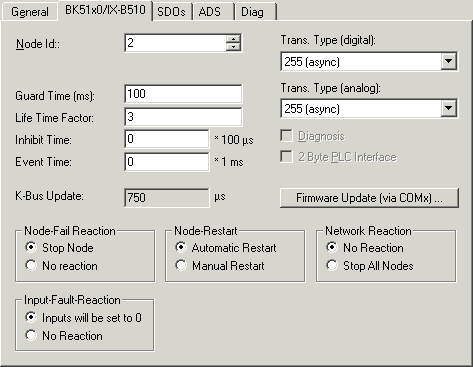
Node Id
Sets the node ID of the CAN bus device (between 1 and 63 (BK51x0) and/or 1 and 99 (IPxxxx-B510)). This value must comply with the value set at the Bus Coupler and/or at the compact box.
Guard time
Cycle time for the node monitoring (node guarding). In the case of the FC5101 this time is used as the producer heartbeat time.
Life time factor
Guard time multiplied produces the watchdog time for the monitoring of the master by the coupler (life guarding). Life guarding is deactivated if the lifetime factor is set to zero. The watchdog time is used as the consumer heartbeat time in bus nodes that support heartbeat.
Inhibit Time
Displays the minimum send interval for PDOs (telegrams) with analog and special signals. If more than digital 64 signals are present, these are also provided with this Inhibit Time.
Event Time
The event time for PDOs 1 and 2 (Rx + Tx) of this node is set here.
K-Bus Update
Calculates the anticipated duration of a complete update of the K-Bus (according to type and number of connected terminals).
Trans.Type
Indicates the transmission type for digital or analog input telegrams. 254 & 255 relate to event-driven transmission, 1...240 are synchronous transmission types. For further details see also BK51X0 manual.
Firmware Update
Enables the updating of the coupler firmware via the serial interface (requires KS2000 software package interface cable).
Diagnostic Inputs
FC510x: Each CANopen fieldbus node contains one diagnostic input byte (Node State), which signals the status of the current slave during the running time and can be linked, e.g. with the PLC. In addition a signal is sent via the "Diag Flag" bit informing as to whether the card contains new Diagnostic Information. This can then be read via ADS READ.
CIF30-CAN: Each CANopen fieldbus box node contains one diagnostic input byte (Box State), which signals the status of the current slave during the running time and can be linked, e.g. with the PLC. In addition there is a further bit ”DataExchange", which indicates whether the node is exchanging data.
The SDOs tab
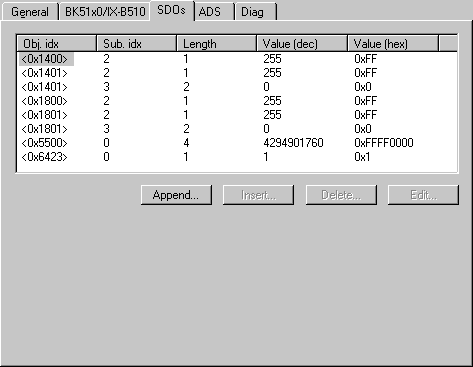
SDO inputs sent to the node at StartUp are displayed/managed on this page. Inputs with an object index in straight brackets are automatically created on the basis of the updated terminal configuration. Other inputs can be managed using Add, Insert, Delete and Edit.
The ADS tab
In order to be able to read and write SDO objects during the running time (e.g. from the PLC), the node (Bus Coupler) can be allocated an ADS port (CIFx0-CAN). The FC510x provides an ADS port at all times for every node since the diagnostic information is transported via ADS. These ports can be used to read and write SDO objects using ADS read requests and/or write requests.
The ADS IndexGroup contains the CANopen object index and the ADS IndexOffset contains the CANopen Sub-Index.
CANopen Emergency Object
Some CANopen status data and emergency objects received from a node can be read by any TwinCAT program via ADS and/or signaled to any TwinCAT program. The data structures and addresses distinguish between the FC510x and the CIFx0-CAN.
![]() | Further documentation More information on the configuration of CANopen bus nodes and master cards under TwinCAT can be found in the TwinCAT documentation or in the manual for the relevant master card. |