Bus Coupler versions in multi-configuration mode
Structure of a production machine
Production machines often consist of a machine part that is always present in the machine and of machine extensions that may be added as options. This division also usually applies as well both to the software (the control program) and to the hardware (the necessary process signals via Beckhoff Bus Terminals) associated with the machine. A machine, with machine extensions A, B and C, whose process signals are to be read or output over the PROFIBUS DP through Beckhoff Bus Couplers BK3110, BK3120 or BK3520, could be structured as follows.
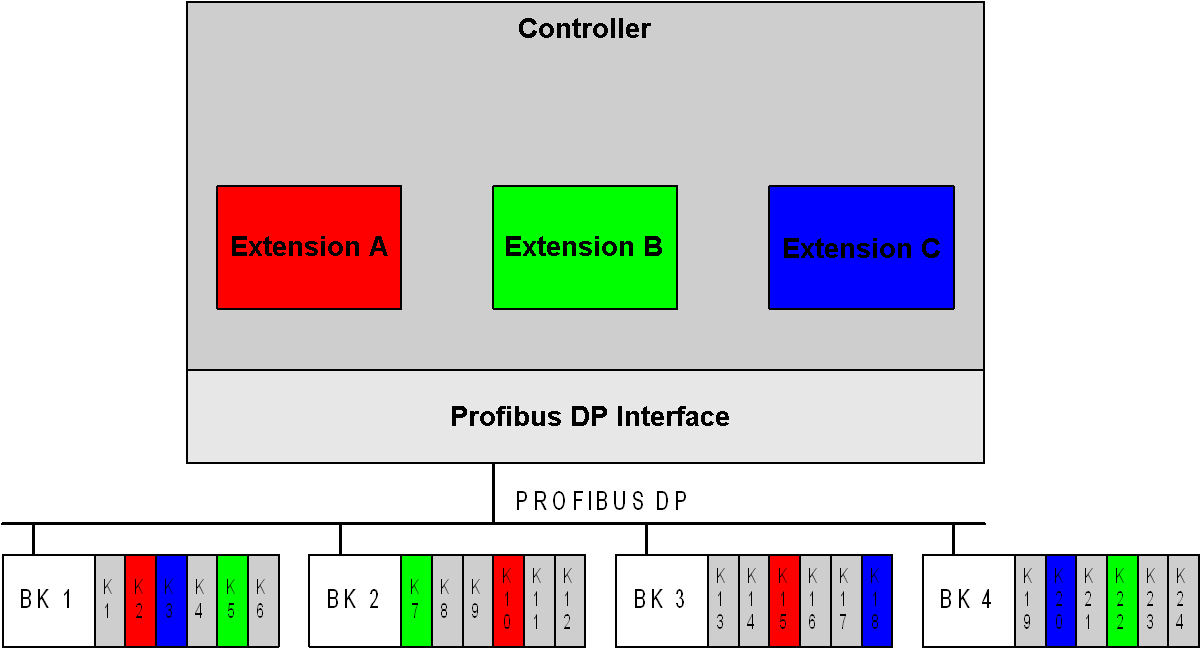
The machine illustrated consists of a controller (e.g. TwinCAT, S7-400, etc.), a PROFIBUS DP master interface (e.g. FC3101, CP???, etc.) that sends or receives the process signals over the PROFIBUS DP, and of Bus Couplers with Bus Terminals that form the interface to the machine process. The areas shown in grey relate to machine parts that are always present. The machine extensions A, B and C are shown in red, green and blue. It can be seen that each machine extension is associated both with software modules within the control program and process signals that are connected to the controller via Bus Terminals.
Because the machine builder will not want to maintain eight different control programs for all possible combinations of the machine extensions, it is helpful if the control program is designed in such a way that the necessary software modules are activated according to whichever machine extensions are in fact being used. In order to create a control program suited to all implementation levels of the machine it is however necessary for the same process signals always to appear at the same addresses in the controller's process image, independently of which process signals are in fact present in the relevant implementation level. For conventional DP slaves, a different configuration of the PROFIBUS DP master interface is necessary in such cases. The following sections explain how this problem can be solved with Beckhoff Bus Couplers, using a single configuration of the PROFIBUS DP master interface.
The advantage of this solution is that two machine configurations only differ in terms of the hardware used (machine components and Bus Terminals), but not in terms of the software. If the machine is upgraded, it is only necessary for the additional Bus Terminals to be inserted and wired-up, and for the relevant extension to be activated (e.g. via the man-machine interface to the machine). Software changes are no longer required.
Process image interfaces
The interfaces between controller, PROFIBUS DP master interface, Bus Coupler and Bus Terminals form process images, in which the process signals are stored according to certain algorithms.
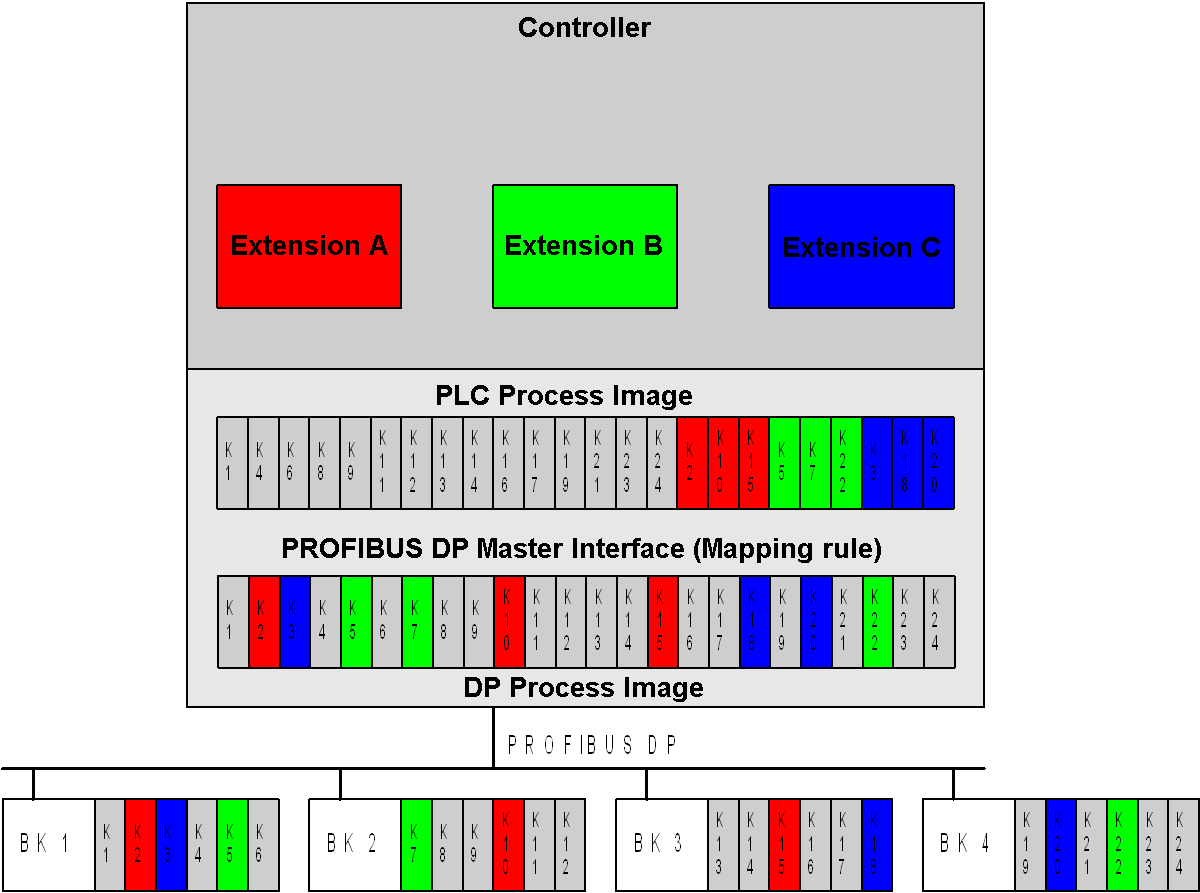
The process signals of a DP slave (Bus Coupler BK3110, BK3120 or BK3520) are always transferred in a Data_Exchange telegram, in which the outputs are sent by the DP master and the inputs are received in the associated telegram response. In the PROFIBUS DP master interface, the process images exchanged with the Bus Couplers are mapped to the process images of the control according to a mapping rule.
Process images of the machine configurations
As shown in the two examples in the figure below, the mapping rule in the PROFIBUS DP master interface changes, depending on which machine extensions are used (there are two examples here).
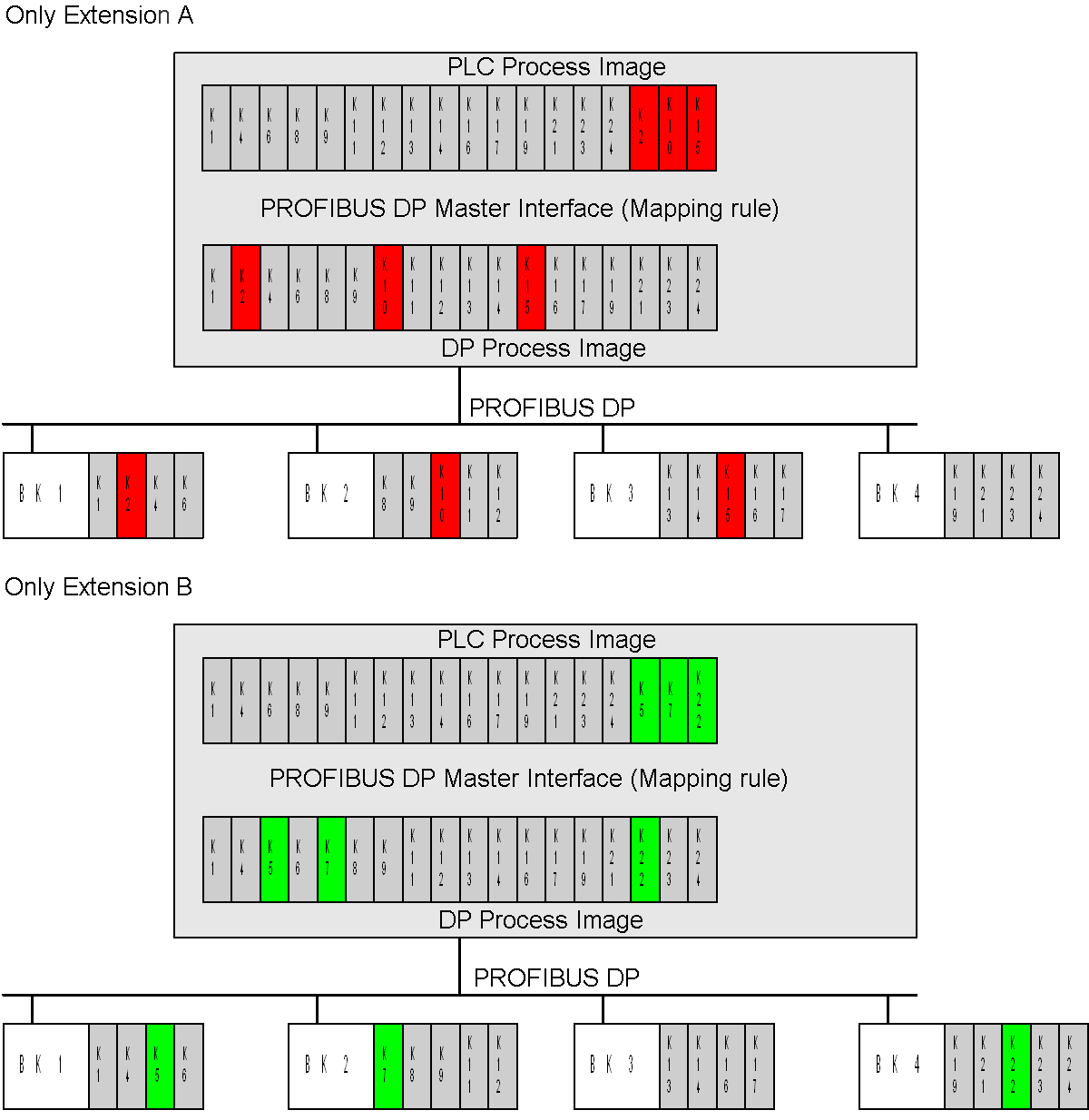
In order to solve the problem of the changed mapping rule, a facility is provided in the BK3110, BK3120 and BK3520 Bus Couplers through which the mapping can be carried out in the Bus Coupler (multi-configuration mode), so that they always exchange the same process image with the PROFIBUS DP master, independently of the Bus Terminals present:
Setting the Bus Terminal extension in the Bus Coupler
So that the same process image can always be transferred between the PROFIBUS DP master and the Bus Coupler, independently of the implementation level of the machine or of the Bus Terminals, the maximum Bus Terminal implementation for the Bus Coupler is always configured in the PROFIBUS DP master under multi-configuration mode. This PROFIBUS DP configuration is sent from the PROFIBUS DP master to the Bus Coupler when the PROFIBUS DP bus is starting up. This then compares the received PROFIBUS DP configuration with the bus terminals that are actually present.
If the Bus Coupler is not already being operated with the maximum Bus Terminal implementation level, the PROFIBUS DP configuration will not agree with the Bus Terminal structure that it finds. So that the Bus Coupler can nevertheless represent the process signals from the connected Bus Terminals in the process image that is to be exchanged with the PROFIBUS DP master, the mapping rule is now required.
Because the Bus Coupler maps the process signals from the Bus Terminals into the DP process image according to a fixed algorithm (first complex, then digital terminals, each in the sequence in which they are plugged in), the only information that is missing is that of which of the Bus Terminals that are included in the PROFIBUS DP configuration are indeed truly present. This information can be transmitted via the acyclic DPV1 Write, or through the 2-byte PLC interface for those PROFIBUS DP master interfaces that do not support PROFIBUS DPV1. The acyclic DPV1 Write is usually available through function blocks (TwinCAT: ADS-Write, S7 400: SFB 52 (read) and SFB53 (write)) from the controller program. The 2-byte PLC interface of the Bus Coupler is mapped directly into the controller's process image. As soon as a machine extension is activated or deactivated, the controller program can therefore activate or deactivate the associated Bus Terminals.
Example as above, where deactivated terminals are marked in yellow:
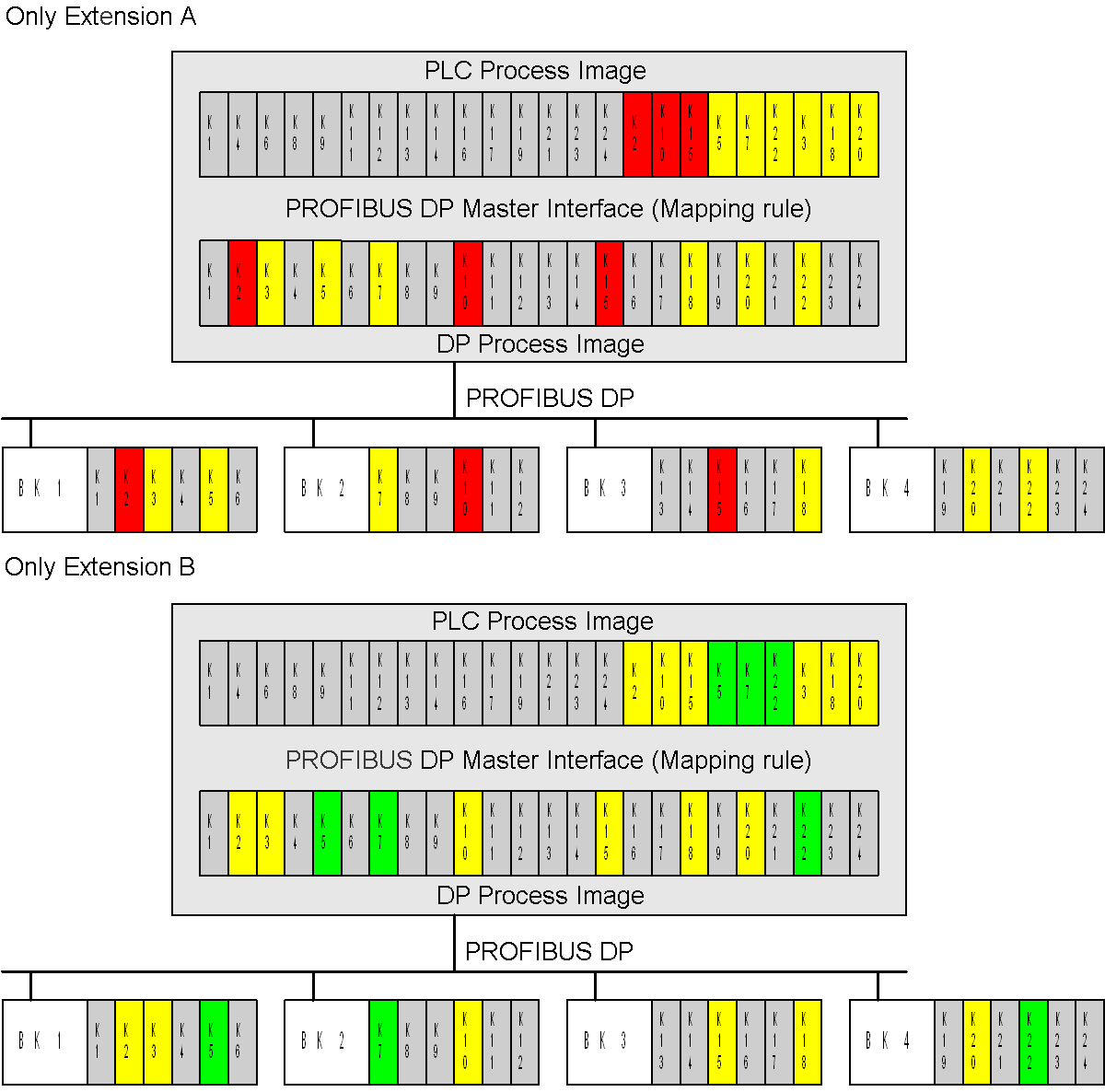
State transitions in the Bus Coupler
If the PROFIBUS DP configuration received does match the Bus Terminal configuration in multi-configuration mode, the Bus Coupler sets the "static diagnostics" bit in the PROFIBUS DP diagnostic data and delays the execution of a terminal bus cycle (I/O RUN LED remains off). As soon as the terminal assignment (activated/not activated) has been written by the PROFIBUS DP master, the Bus Coupler again carries out an examination of the PROFIBUS DP configuration, and automatically enters cyclic data exchange (the "static diagnosis" bit in PROFIBUS DP diagnostic data is cleared, and the terminal bus cycle is executed cyclically (the I/O-RUN LED goes on during the terminal cycle)). Furthermore, the terminal assignment is stored in the non-volatile memory of the Bus Coupler, so that during a restart of the PROFIBUS DP, the PROFIBUS DP master does not have to write the terminal configuration again.
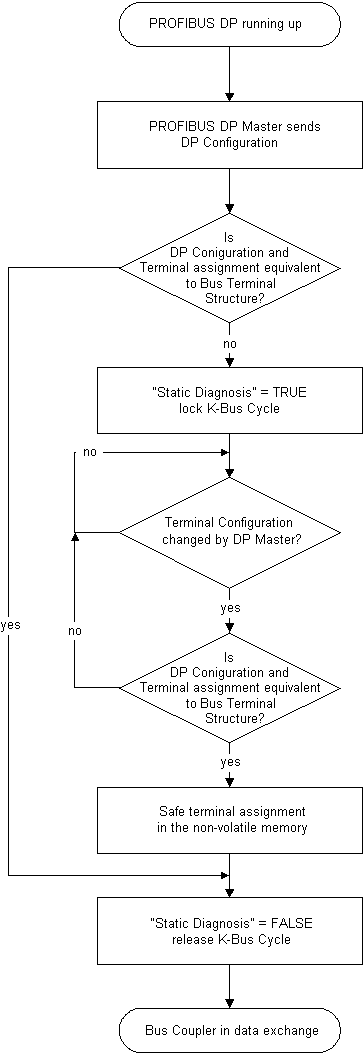